By Clark Ricks
Truck-mounted spray pumps are convenient. Some units are small enough that the tank, heater, pump, reel and hoses will easily fit in the bed of a standard pickup. The unit is hard-wired into the vehicle’s electrical system, and use the engine’s coolant system to heat the waterproofing material.
Every waterproofer needs a spray pump. Whether the business specializes in commercial or residential projects, above-grade or below-grade, it’s probably the most critical—and expensive—piece of equip-ment the company owns.
“Foundation waterproofing spray equipment can be the biggest capital expenditure for a waterproofing contractor when they are starting out,” acknowledges Aaron Kuertz at Applied Technologies. “So it’s important to purchase the right piece of spray equipment. Too large of a piece of equipment and it may be difficult to stay afloat. Too small and you may not be able to spray enough foundations in a day for your customers.”
According to Chris Bryntesen at C.J. Spray, a major manufacturer of pumping equipment, the best place to start is to choose the waterproofing product.
“The biggest problem with waterproofing is that you can’t flip-flop products,” he explains. “Waterproofing materials are very thick and very heavy, and don’t flush out of the equipment very easily. I’m not saying it can’t be done, I’m just saying you don’t want to do it day after day.”
John Goodman, National Sales Manager at Spray Equipment and Service Center says, “Our equipment can spray a wide variety of waterproofing products as long as it’s a self-leveling, single material. Commercial contractors will usually spray different products on different jobs depending on what’s specc’d. On residential, typically the waterproofer can use his preferred product.”
Still, both admit that a contractor that does a lot of waterproofing will generally have different pumps for different products.
Kuertz points out that real waterproofing is different than dampproofing. Dampproofing stops water vapor from penetrating into the living area of the basement, but it does not stop water under hydrostatic pressure or bridge cracks in a foundation.
True waterproofing material must meet three criteria:
- It must stop water vapor from penetrating to the interior.
- It must span shrinkage cracks that develop in a foundation wall.
- It must prevent water under hydrostatic pressure from pene-trating into the basement.
Water-Base Vs. Solvent-Base
Waterproofing materials come in two basic varieties: emulsion-based materials that use water as the carrier agent, and solvent-based materials that use naptha or another solvent as their base. Each has its advantages.
Water-based coatings have no solvent fumes, which means less health risks and less personal protective equipment for the applicator. The coating won’t damage plastics or foam, and equipment can be cleaned with water. Perhaps most importantly, water-based coatings can be applied to damp surfaces. This is a major advantage in situations where rain has fallen, or wet soil has been removed to expose a foundation that needs to be treated.
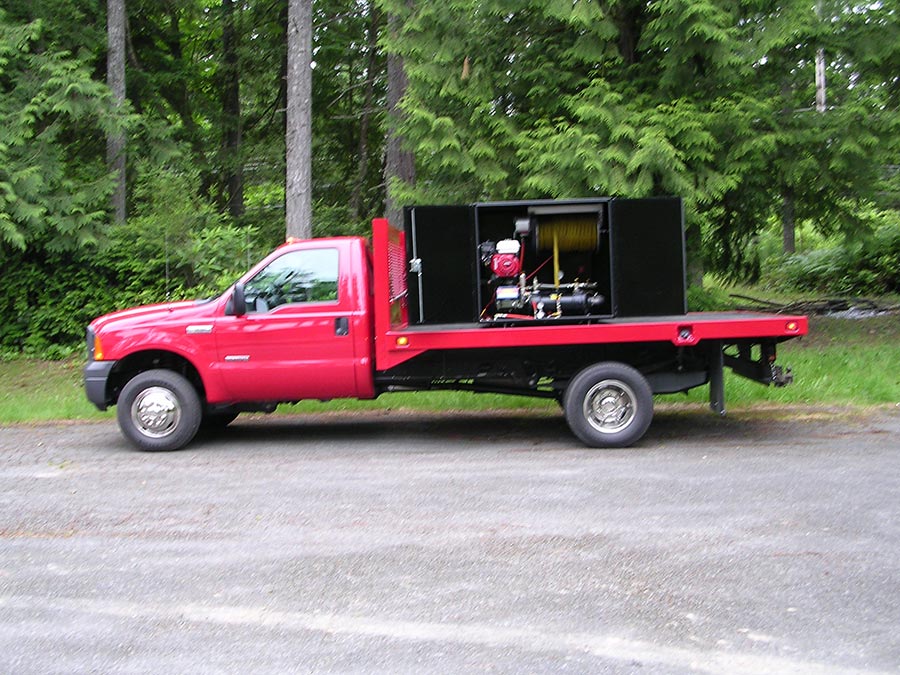
Some units are cabinetized, and have their own engines and heating systems, so contractors can use either a trailer or a flat-bed truck to get them from job to job.
The disadvantage, of course, is that it can be washed off if rain falls before it is fully cured. Also, emulsion-based coatings must be protected from freezing temperatures—in storage, transport, and during application.
Solvent-based coatings, on the other hand, are not damaged by freezing temperatures, which makes them a popular choice in northern climates. But applicators must wear special protective clothing and respirators, and the coatings can’t be applied to damp surfaces.
The critical difference for spray equipment is that solvent-based materials are applied hot. “Emulsion materials require little or no heating of the material,” says Kuertz. “Solvent-based materials usually must be heated to 130-150 degrees in order to spray. Because a basement waterproofing contractor needs a sprayer that will do the job reliably and quickly, the best method of spraying a solvent-based material is to have a heated tank system.”
Solvent-based spray systems have in-tank heaters, insulated hoses, and other components that aren’t necessary for water-based sprayers.
Bryntesen, however, cautions that heaters are a good idea regardless of the type of system is used. “A lot of the asphalt-based guys say you can get by without an heater, but you can work a longer season if your equipment has one,” he says. He says water-based materials gets twice as thick every 20 degree (F) drop in temperature.
“If the material sprays well at 70 degrees, it may not when the temperature drops to 50. So even if the customer is using an emulsion-based system, I’m still going to recommend a heater to him. It lets you spray in colder weather, and it makes it easier to push through 200 ft of hose.”
Components
A spray rig will always have a few basic components: a tank, a pump, some sort of heating system, hose, reel, and spray gun. The equipment can either be mounted on a flat-bed truck or a separate trailer, depending on its size and complexity.
The Tank: These vary from simple 100-gallon totes to truck-mounted giants holding 500 gallons or more. Emulsion-based systems can sometimes be pumped directly from the drum.
Goodman cautions that plastic tanks may not hold up well if the contractor is using a solvent-based material.
The Heater: Nearly all heat exchangers use engine coolant as a heat source. Truck-mounted pumps are connected to the engine’s cooling system. Trailer-mounted spray equipment usually have a separate gas or diesel engine powering the pump, which also provides the heat for the exchanger.
The Pump: The pump determines both the pressure in the tank and the product’s rate of application. On small pumps, gas-mechanical devices are used, since they convert the engine’s horsepower into fluid movement most efficiently. Gas-hydraulic systems are also common, and in larger motor sizes—more than about 12 horsepower—they are the only engine-driven system that lasts.
Many spray rigs use pneumatic pumps. Bryntesen, at CJ Pump, says pneumatic pumps cost less and typically last longer. They also have the advantage of not producing fumes like gas and diesel engines do. The catch is that the contractor also has to transport an air compressor and hoses on-site in order for the spray rig to work.
The Hose and Gun: “For ease of use, a foundation waterproofing sprayer should have an electric hose reel,” says Kuertz, at Applied Technologies. “This will allow a contractor to quickly finish a job and continue to another. Also, the spray hose should be insulated and covered with an abrasion protection sleeve. This will both keep the waterproofing material at the proper spray temperature and protect the hose from damage.” Most rigs come with 150 or 200 feet of hose.
The spray gun should match the viscosity and pressure of the fluid, as well as the desired rate of spray.
Other: “Temperature gauges should be on both the tank and the spray hose so that the contractor knows the temperature of the waterproofing material,” says Kuertz. “A pressure gauge is useful for both correct spraying and in diagnosing any problems that may occur with the pump.”
If the contractor chooses an emulsion-based system, the tank needs to be protected from freezing. A number of enclosed trailers and heavy duty van platforms can meet this requirement.
Selecting a Spray Rig
As mentioned above, the first step in getting a spray rig is selecting a waterproofing product. “Focus on the product,” suggests Goodman, “because the pump is a one-time investment.”
“If he already has a flat-bed truck,” Goodman continues, “We offer a heated cabinetized unit that works really well. It has a 150-gallon tank, heat exchanger, heated and jacketed hose, the reel, spray gun, and a Graco GH230 pump.” This combination sprays 2.1 gallons per minute.
Applied Technologies offers a truck-mounted unit small and light enough to be transported in a standard half- or three-quarter-ton pick-up.
Keep in mind that any truck-mounted spray rig must be tied into the engine coolant system (and electric system as well) so the truck would be dedicated to being a pump truck. It would be committed to that location as long as the waterproofing job lasts.
That’s why many waterproofers prefer trailer-mounted units, which they can drop at the jobsite without having to tie down a truck. These are typically larger units. Spray Equipment’s Spray Hog, for instance, has an 18 horse-power water-cooled diesel engine, and sprays at a maximum pressure of 4,000 psi at four gallons per minute. It comes with a 55-gallon dip tube, or can be adapted to a 330 gal tote. “The advantage is you don’t have to dedicate a vehicle,” says Goodman. “You don’t have to run the truck engine; it can be trailerized. You can drop it off at the site with an applicator, and then get on with your day.”
Applied Technologies’ DTS 240 spray rig offers a unique solution to the difficulties of switching waterproofing products. It comes with dual 118-gallon heated tanks, each with its own heat control and on-off switch so the applicator can use one spray unit for two different materials.
Many pump manufacturers sell components individually, so contractors can configure their own equipment.
Bryntesen notes that spray rigs can often be upgraded or reconfigured quite easily. “We can refit or change a tank, add a heater, or even add an additional pump to bottom of the tank for more viscous products,” he says.
Goodman and Bryntesen note that many times, pumps really are a one-time investment. “I have Graco pumps out on the lot that have lasted 20 years or more,” Bryntesen says.
Purchasing
Typically, if a contractor contacts a waterproofing manufacturer and expresses an interest in becoming a waterproofer, the material manufacturer will come out and do a demo, explain their plan, and the profit potential involved.
“I don’t know of anyone that rents the equipment,” says Goodman. “The manufacturers want a commitment from the contractor”.
A few, including Spray Equipment and Service, lease spray rigs, but Goodman says purchasing is still the most common option. “Most of the time, the guys have the cash, or they have a relationship with a banker in their own community,” he says. “Especially if they’re concrete guys getting into waterproofing, a ten, twelve, or 15,000 dollar system isn’t that big of a deal. I had a guy come in last week and put an $8,000 system on his credit card.”
Bryntesen notes that this year is an especially good time to invest in a spray rig. “The stimulus package expands the 179 deduction to include spray equipment,” he says. “If they’re looking at buying, they have a temporary window in which they can use accelerated depreciation. It’s a good chance to get equipment that’s going to last a long time.”
Summer 2018 Back Issue
$4.95
Livable Basements
AVAILABLE AS DIGITAL DOWNLOAD ONLY
Description
Description
Additional Info
Additional information
Magazine Format | Digital Download Magazine, Print Mailed Magazine |
---|
I’m using a water based elastomeric rubber (liquid rubber Canada foundation seal), I read your article about sprayer rigs and was hoping to get information on a more portable/smaller unit to spray rubber such as the graco 7900 or graco 675.
I’ve already talked about the graco 733,833, and 933.series but once again I start to lose mobility hence the 7900 as an option. Do you think those roof.coating sprayers would work daily for my needs