by Clark Ricks
The largest solar panel array in Western New York is installed on the roof of a student dormitory at the University at Buffalo. The 6,300 sq. ft. of photovoltaic panels will produce enough power to meet the annual electrical requirements of 10 average households.
Rooftop solar panels are becoming increasingly popular. Rising energy prices, combined with concerns about pollution, global warming, and sustainable building practices have made the technology more viable than ever before.
“As any technology expands, price comes down,” says Patrick Howard, CEO of the Howard Company, a supplier and consultant to both the waterproofing and solar panel market. “This is especially true of photovoltaics, and now there are all the green energy incentives coming into place as well.”
In San Diego, for example, solar integrated roofing systems have been installed, or installation is in progress, on 14 city schools, with more scheduled in the coming two years.
Benefits
The school system expects to save millions of dollars in energy costs over the next 20 years, in addition to helping the state make progress toward the goal of generating 20% of its electricity with renewable sources by 2017.
Howard cites cases where Southern California Edison has approached large building owners to essentially rent their roofs. In one instance, they leased back roof space on a 100,000 sq. ft. Montana facility to install solar panels and sell the electricity back to the users.
Photovoltaic roofs also help buildings qualify for certification with green building programs. Under the U.S. Green Building Council’s current LEED criteria, a building can gain up to 3 points by using solar energy.
Most solar roofs, especially in the commercial sector, are more properly called “photovoltaic panels.” These systems convert light into electrical energy using thin wafers of silicon. (The other type of panel is basically a solar hot water heater.)
For rooftop waterproofers, rooftop panels create additional challenges, as the mechanical attachments, cables, pipes, and other penetrations need special attention. Recently though, several new technologies promise to radically simplify installation, and make solar energy generation more cost-effective than ever before.
Built-In Panels
Frito-Lay, the snack food maker, installed a photovoltaic roof on its 65,000 sq. ft. facility near Los Angeles, California.
The decision was partially driven by the chronic power outages that plagued the state in 2000 and early 2001. Electrical blackouts and record high energy bills made business difficult. The company also has a reputation for being environmentally conscious. So when the distribution warehouse needed to replace the existing built-up roof with a durable, long-lasting alternative, they chose to include solar panels.
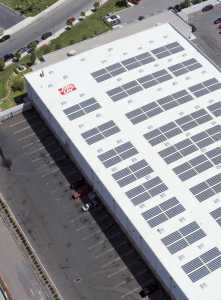
The Frito-Lay Distribution Facility in Los Angeles uses a new technology that combines a waterproofing membrane and solar panels into a single flexible product.
“The LADWP [Los Angeles Department of Water and Power] was offering a substantial incentive to install solar photovoltaic roof systems,” says Chris McKenna, electricity manager at Frito-Lay. “That made the project economical for us.”
The project was the first to use a new product from Solar Integrated Technologies (SIT) called SR-2001. The design combines an impermeable waterproofing membrane with photovoltaic cells in a single sheet.
SR-2001 uses a 60-mil single-ply thermoplastic membrane from Sarnafil as a base, then laminates a dozen flexible, thin, lightweight photovoltaic modules onto it.
Peter Chaitkin, account executive at Solar Integrated Technologies, says they chose the membrane due to its performance history and heat-welded seams. “It provides the owner with a durable roof that lasts for decades,” he says.
The 10-ft-by-40-ft photovoltaic roofing panels are then hot-air welded to an installed Sika Sarnafil EnergySmart Roof. Each panel generates approximately 1,500 watts. The result is a photovoltaic roofing system that protects the building interior from the elements while generating power for its electricity needs.
Southern California Roofing got the nod to install the system.
First, we arranged the photovoltaic modules according to the customer’s request for kilowatt power,” said Chuck Point, project manager at Southern California Roofing. Since Frito-Lay wanted a 100 kilowatt system (100,000 watts), the roof needed 70 of the 10x 40 panels. He says the actual installation went smoothly, noting that the company has installed Sarnafil products for more than 20 years and the workers are very familiar with it.
The outer face of the membrane is white, which increases the panels’ efficiency.
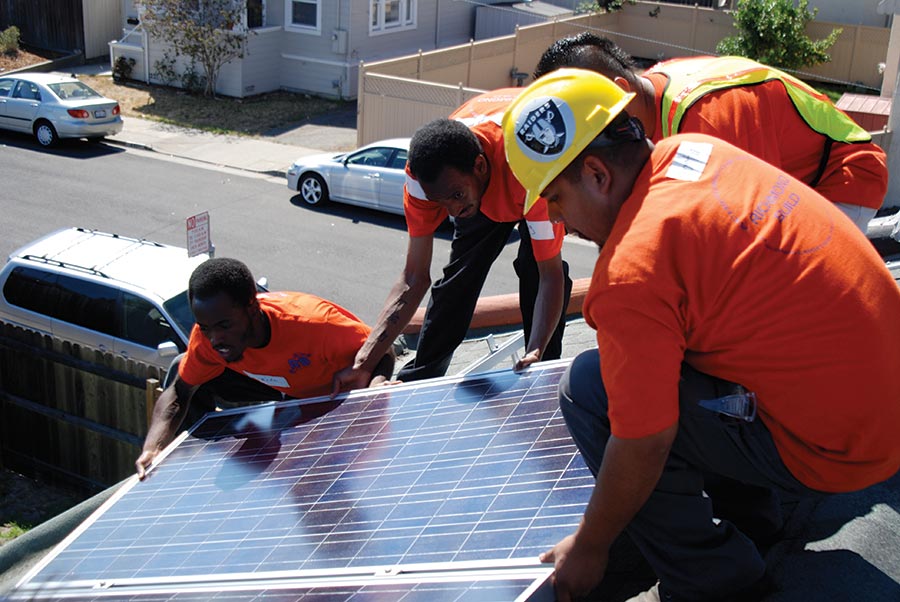
Conventional solar panels are rigid, and sit above the roofing membrane. The penetrations, supports, and flashings these require need special attention to ensure the roof remains impermeable.
“The membrane’s reflectivity allows the flexible photovoltaic panels to absorb more of the sun’s rays in less-than-optimum conditions,” said Chaitkin. “The EnergySmart Roof membrane reflects the sun’s rays, reduces heat absorption into the building, decreases cooling costs, and actually increases the productivity of the solar panels.”
Energy from the panels is collected in wires and routed to inverters that convert the DC power into alternating current that Frito-Lay can use to run computers, lights, air conditioners and other equipment.
Completed in 2003, the roof generates about 186,000 kilowatt hours of clean energy annually, enough electricity to power 28 homes.
“The system works so well that during some periods of the day, we are producing more power than we need,” said McKenna. “When that happens, the extra power gets fed back into the utility grid.”
The company has since installed another system on its Sylmar, California distribution center roof, and anticipates additional installations in the future.
“The Most Exciting Project I’ve Worked On”
The same SR-2001 panel was also used on the National Archives and Records Administration (NARA) building in Waltham, MA. The facility stores thousands of irreplaceable federal documents, so when its EPDM roof started failing, it was critical to find a new roof.
“We had considered different types of roofing systems, including TPO, PVC and EPDM, but we wanted an Energy Star ‘cool roof’,” says Roman Piaskoski, regional energy coordinator for the government agency overseeing the project. “When we heard of this system that uses flat thin film, flexible, amorphous silicon panels integrated with a Sarnafil EnergySmart Roof we thought ‘Hey, this could be it!’”
In addition to saving the GSA about $67,000 per year in electrical costs, the built-in photovoltaic (BIPV) system will also result in substantial greenhouse gas reductions. “This is one of the most exciting projects I’ve worked on in my 17 years with GSA,” Piaskoski stated.
Metal Roofing Options
Built-in photovaltaics are becoming quite common, and are available for many different roofing systems, including metal roofing.
SolarPower Restoration Systems markets SolarSeal PV, a metal roof system that combines photovoltaic technology with high-performance elastomeric coatings. According to Michael Gunn, company vice-president, it creates a leak-proof, energy-generating roof over any standing seam or R-panel industrial metal roofs.
“Commercial buildings with metal roofs use industrial R-panel roof panels or the newer architectural standing-seam roof panels,” he says. “Both R-type roof panels and the architectural snap seam metal panels are waterproofed using elastomeric coatings designed to work with each specific type of metal roof surface.”
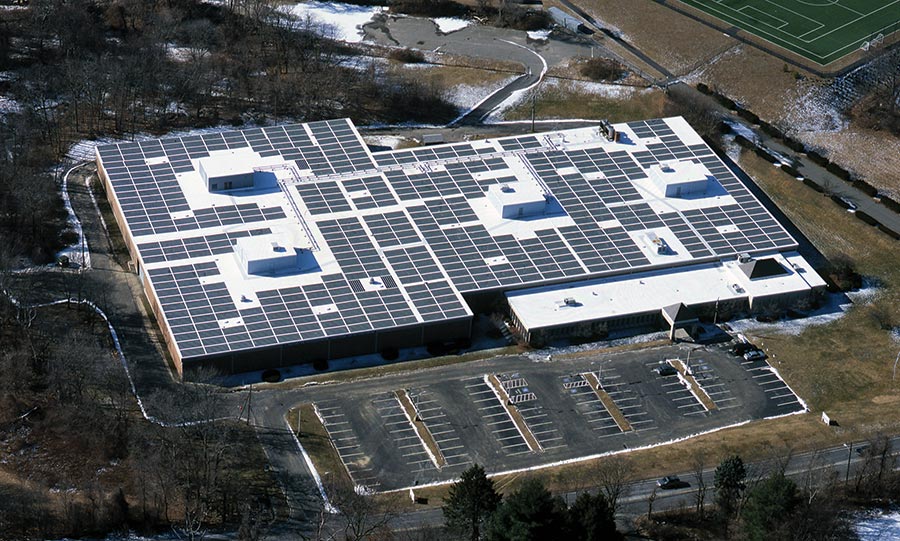
Built-in photovoltaic (BIPV) roofing is becoming quite common—and lucrative. The roof of the National Archives Building in Maryland (above) is literally covered with BIPV panels. They were attached to the existing membrane using hot-air welding (below). On sunny days, excess energy is sold back into the power grid.
Once the roofs are waterproofed, solar modules are applied to the coated metal surface. Materials such as synthetic textiles, polymers, insulation or radiant water modules are used to bridge irregular metal panel surfaces and exposed fasteners. Photovoltaic modules are bonded to the components and flashed and sealed, creating a continuous, seamless, waterproofed roof surface.
“The SolarSeal Roof System is a long-term solar waterproofing solution for metal roofs,” says Gunn. “They’re easy to maintain and can be renewed without affecting the photovoltaic system’s power production.”
He adds that, like SR-2001, the white elastomeric coating reduces metal roof surface temperatures and lowers cooling cost.
Summer 2009 Back Issue
$4.95
Solar Roofs: Challenges and Waterproofing Solutions
Foam in Waterproofing Systems
Sump Pumps: Advances and Installation
Green Sealants at the Bottom of the World
AVAILABLE AS A PDF DOWNLOAD ONLY
Description
Description
Solar Roofs: Challenges and Waterproofing Solutions
The popularity of green building, coupled with significant price declines in photovoltaic systems, has led to a significant increase in solar roof installations. Here are solutions to ensure the roof is leak-free.
Foam in Waterproofing Systems
Whether used as a drainage board, underslab insulation, or in roofing systems, every waterproofer deals with foam board. Polystyrenes and polyurethanes each have their own advantages and special application techniques.
Sump Pumps: Advances and Installation
Sump pumps are a critical component of below-grade waterproofing in many areas of the country. New technologies and installation methods make them more fail-safe and affordable.
Green Sealants at the Bottom of the World
Princess Elisabeth Station was built in one of the world’s harshest and most remote regions. Designers also insisted on extremely demanding green building standards
Additional Info
Additional information
Magazine Format | PDF Downloadable Magazine, Print Mailed Magazine |
---|