Carbon fiber makes basement structural repair easier and more profitable. Whether the job calls for straps, staples, or whole sheets of material, there’s a product on the market to fit your needs.
In terms of weight-to-strength ratio, carbon fiber is currently the best material that our civilization can produce. Far stronger and less bulky than steel, carbon fiber is transforming a broad range of industries, and waterproofing is one of them.
Thanks to carbon fiber’s amazing properties, basement structural repair is easier and more profitable than ever before. Whether the job calls for straps, staples, or whole sheets of material, there’s a product on the market to fit your needs, and a manufacturer to back it up and make sure they will perform.
What it is
Todd Jackson, technical director and co-founder of Fortress Stabilization Systems, says most of the carbon fiber on the market today is basically “cooked rayon,” a simplistic but accurate description of how the material is made.
Thin strands of poly-acrylo-nitrile are introduced into an oven, where they’re roasted at nearly 500 degrees Celsius. This burns off the hydrogen, and forms the carbon atoms into chains. Then the heat is increased to 1200 degrees Celsius, near the melting point of steel. At these temperatures, the remaining impurities—mostly nitrogen—are driven off and the material that’s left is almost pure elemental carbon. The secret to its strength is that during the final heating process, the carbon atoms bond to each other with extremely strong force to form a series of hexagons, similar to a honeycomb or chicken wire.
The microfibers that leave the oven measure about 5 micrometers in diameter. (The average human hair, by comparison, is 50 micrometers.) These are spun into threads, which can then be woven or embedded in a variety of foundation repair materials.
Advantages
Carbon fiber has one of the highest tensile (pull) strengths known to exist. Even under incredibly high tension, carbon fiber will not stretch or break, which comes in handy when repairing below-grade structural concrete. Whether it’s used as sheets, straps or staples, carbon fiber can keep basement walls from bowing and cracks from expanding.
For instance, a steel I-beam used in foundation repair can resist 30,000 to 40,000 lbs of tension, and can stop a wall from bowing. But a four-inch wide carbon fiber strap can withstand 8 to 10 times that much pressure, and is less 1/8-inch thick.
Homeowners appreciate a fast, non-invasive solution that gives them more living space, and improves resale possibilities. Also, the repair is nearly invisible when complete.
From the contractor’s perspective, the system eliminates the need for jackhammers or backhoes. There’s no crew hauling out buckets of concrete. Everything fits into the back of a pick-up truck, and most jobs require no more than two workers. The job is done in less than a day, so there’s less labor and significantly more profit in the job.
Luke Secrest, a basement repair specialist who markets and installs carbon fiber systems, gives this cost breakdown:
Complete carbon fiber kit $140.00
Metal Beam Installation
13# Steel beam installation $96.00
Bolts and Hardware $6.00
Wood for blocking $8.00
Bag of Concrete $5.50
Grout for back side of beam $7.00
Total cost $122.50
“By the time you factor in the additional labor, equipment, transportation costs, wear and tear on truck, damage to wall getting the beam in the basement, and potential workers comp claims, I really don’t think you’ll be saving anything,” Secrest says.
Andre LaCroix, who markets the StablWall line of carbon fiber repair products, agrees. “As a material, it’s slightly more expensive than steel beams, but factoring in the lower cost of labor, the lower cost of tools and faster completion times, and you’ll be surprised how affordable it really is.”
Carbon fiber is durable, too. Even outdoors in harsh weather conditions, there is no deterioration, no corrosion, no rotting, and no movement. (While steel will stretch six percent before breaking, carbon fiber stretches less than one percent.)
Application is easy and flexible. It can stabilize virtually any clean, dry substrate: CMU, poured concrete, even brick and clay tile. Three-dimensional shapes like columns, pillars, and rough-hewn stone are no obstacle.
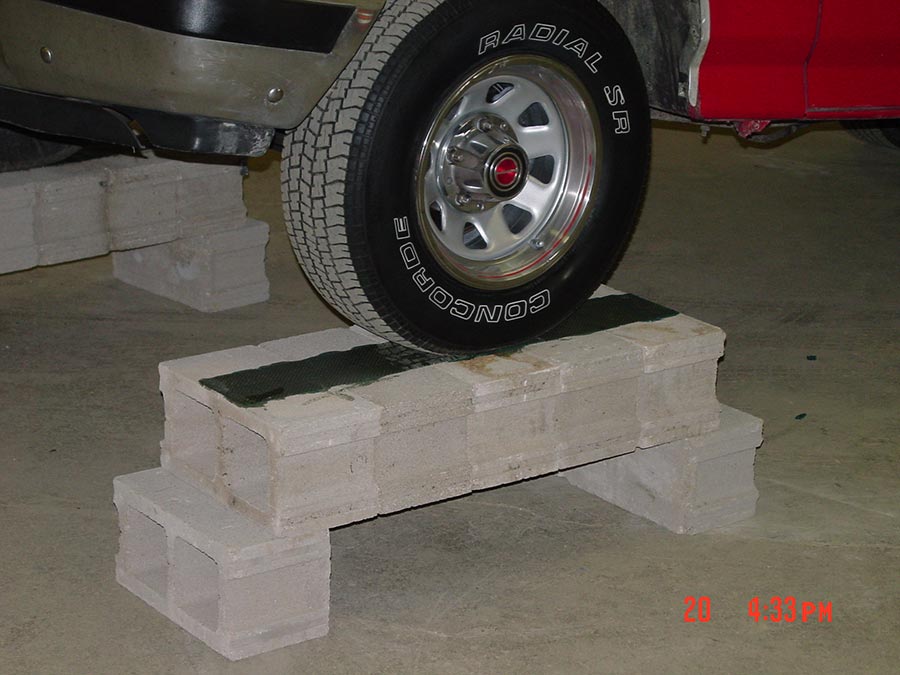
A single carbon fiber strap, attached to the top and bottom of these blocks, is enough to support the weight of full-sized truck.
Drawbacks
Despite its incredible tensile strength, carbon fiber has very little compressive or sheer strength. Unidirectional products, like straps and staples are prone to fail unless steps are taken to ensure they remain constantly in tension. Typically, this means filling cracks with epoxy or mortar. Polyurethane foams are usually too soft to prevent movement.
“The Achilles’ Heel of carbon fiber is that the contractor needs to pay attention to tuck points,” says Jackson, at Fortress. If the wall has an inch of deflection in the middle of winter, when the repair was made, and the contractor didn’t tuck point it, the wall will move backwards in the spring and the strap will bubble or pop off.”
Carbon fiber will not resolve structural failings. Any settlement problems must be resolved before turning to carbon fibers.
“It’s not designed to straighten walls, or withstand sheer loads, or stop settlement,” says Bob Thompson, owner of Nationwide Reinforcing. “If we see a wall that has bowed in excess of two inches, it’s not suitable for carbon fiber.”
“Two inches is a good rule of thumb,” agrees Jackson. “Our product will hold more than this, but it would be hard to sell or refinance your home [with a bow that’s so visible]. Our product is warranted up to a two inch bow.”
In the past, walls that tilted in from the sill plate or footer were off-limits, too, but a new line of products from Rhino Carbon Fiber Wall Supports claim to have solved that problem.
Installation
Carbon fiber is applied much like fiberglass.
The first step is to determine where the reinforcing is needed, and marking those locations on the wall. For a typical bowed CMU wall, that means a strap every four feet. (According to ACI standards, reinforcements of any kind should not be placed further apart than four times the thickness of the wall.) For reinforcing epoxy crack repair, it means a staple every 12 to 24 inches.
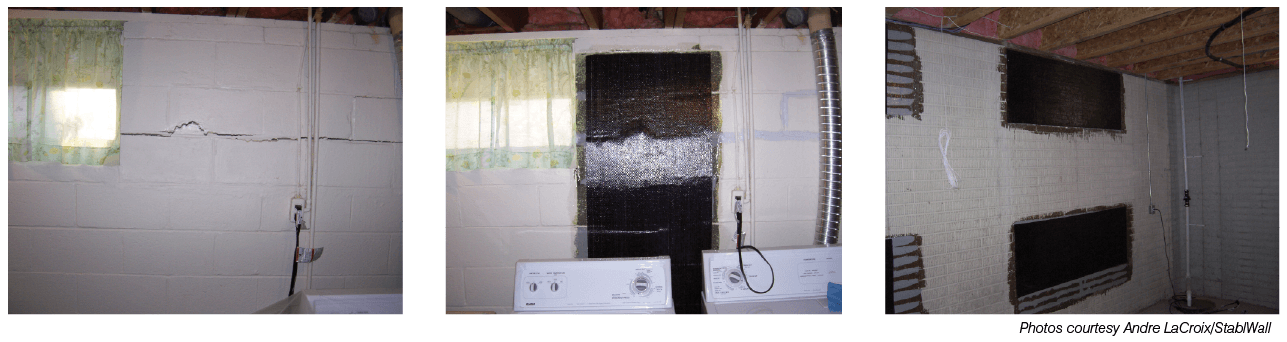
Carbon fiber can easily work around windows, water lines, and electrical routes (above). Sheets can also be applied horizontally (above right) to maximize the tensile strength of the material.
Next, the contractor grinds off any paint, dirt, or other residue in the area the carbon fiber will be applied. Many manufacturers recommend filling cracks and mortar joints with epoxy or grout. This not only eliminates wall movement, but provides a smoother surface for maximum adhesion. The goal is to get a smooth, clean substrate.
Surface prep is very, very important,” says Jackson. “You want to remove the lantance [cured cement paste near the surface] and get down and expose the actual aggregate.”
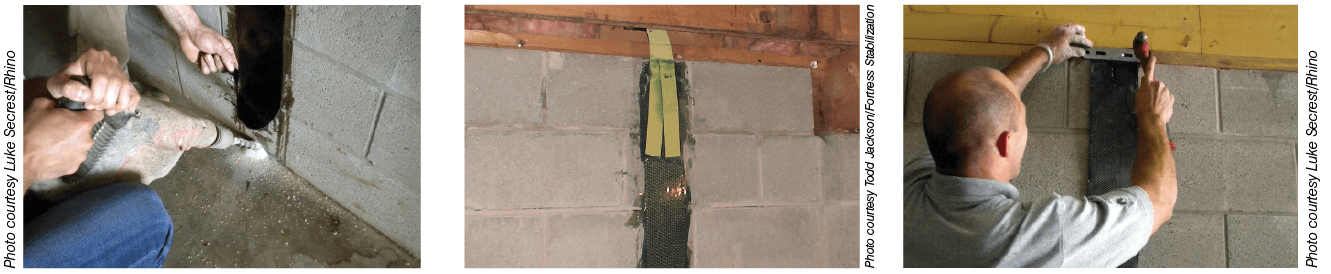
Even if cracks are near the top or bottom of the wall, carbon fiber can create an incredibly strong, permanent repair. Options include Rhino’s carbon fiber footer pin (left) for the wall base. For cracks near the sill plate, there’s Fortress’ Kevlar “Necktie” (center) and Rhino’s bracket system (right).
After the aggregate is exposed and smoothed, and cracks are filled, a primer coat of epoxy is applied to the wall and to the back of the carbon fiber product, which is carefully attached to the wall. The carbon fiber material must be completely impregnated with epoxy. Some products are “wet-laid” at the jobsite. Others come “pre-preg” so a primer coat is all that’s needed. A few manufacturers require a second coat of epoxy to ensure good adhesion; with others, the primer coat is all that’s needed.
Basement Repair Applications
At least half a dozen companies market or manufacture carbon fiber products specifically for basement repair. These include straps for bowed walls, staples for crack repair, large sheet-sized column wraps, pre-cured plates to take the place of steel, and a number of specialty products for corners and joint reinforcement.
Straps—Perhaps the best-known carbon fiber repair product is The Reinforcer, made by Nationwide Reinforcing. Concrete block (CMU) walls are notorious for bowing, and carbon fiber straps can stabilize the wall more quickly than nearly any other solution.
The Reinforcer is four inches wide, and is applied from nearly floor to ceiling. Unlike a steel beam, which would contact the wall only in the middle of the bow, The Reinforcer provides support along the entire length of the strap, locking the wall into place.
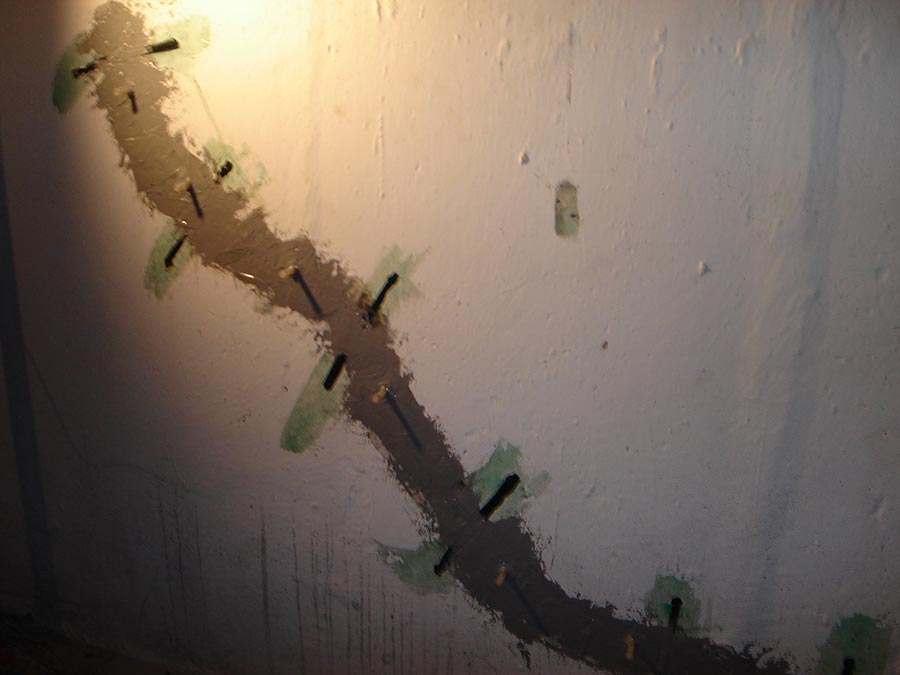
Carbon fiber staples add only a few dollars to the cost of a crack repair job, but virtually eliminates call-backs because they transfer stress away from the fracture.
“When the Reinforcer is applied to basement foundation walls, it counteracts further outside pressure on the wall,” explains Thompson, inventor of the product. “It keeps the inside face of the wall from stretching, and if it won’t stretch, the wall can’t bow.”
The Unidirectional Carbon Strap System from Fortress Stabilization Systems is also designed for this situation. The carbon fibers are encapsulated in a thermal set resin and cured under pressure during manufacturing process, so after the wall is primed, it’s basically a peel-and-stick product. It’s available in 2-, 4-, and 6-inch widths.
One potential problem with strapping is that it shifts pressure to the top and bottom of the foundation wall. To address this problem, Fortress has invented the “Necktie,” consisting of an aluminum bracket and Kevlar webbing. The bracket is screwed to the sill plate and the webbing epoxied onto the wall below it to prevent movement.
Rhino Carbon Fiber Wall Supports goes a step further. The Rhino system provides continuous carbon-fiber strength from the foundation all the way up to the house framing. Rhino is fastened above the sill plate with a galvanized bracket and secured to the footing with a massive carbon fiber stake.
Secrest, who markets the system says, “Transferring soil loads to the top and bottom of the wall may eventually cause additional damage, resulting in more repair work needed. Rhino eliminates this possibility.”
Sheets—Knowing that uni-directional straps will not perform under sheer loads, a number of companies manufacture carbon fiber sheets.
We wanted to come up with a carbon fiber product that would work in 95% of basements,” says LaCroix, at StablWall. His solution is a 2-foot by 5-foot woven sheet of carbon fiber. “We can run those sheets horizontally, vertically, or even on the diagonal to make sure we’re perpendicular to the crack and maximizing carbon fiber’s tensile strength.”
Nationwide Reinforcing makes The Reinforcer Shield, for jobs better suited to sheets. According to the website, it’s best for jobs that require “flexural and shear strengthening.”
“If it’s a unidirectional load, any [carbon fiber strap] will do what they’re supposed to do,” explains Jackson. “But in the real world, you could have sheer loads that the foundation is not set up for. Minor settlement, for example. Sheet goods provide multi-directional strength that could carry the load to a certain point.”
Fortress markets a woven carbon-fiber/Kevlar sheet. Kevlar offers better multi-directional strength than carbon fiber, and is used for the horizontal fibers to produce considerable resistance to tensile and sheer forces.
Carbon fiber sheets are not mechanically attached to the sill plate or floor, but are a great choice for eliminating bowing and cracking in nearly all situations involving CMU walls.
For LaCroix, the biggest advantage of sheets is customer perception. “The advantages are first and foremost, the customer’s impression and confidence level. They feel better about having a wider footprint on the wall,” he says.
Installation is similar to the strap products already mentioned. Because the fibers must be completely saturated in resin, most products of this type require a second coat of epoxy once the sheet is adhered to the wall.
Sheet goods can solve many problems straps cannot. For instance, they’re more flexible so they conform better to irregular shapes, making them a perfect choice for circular or square columns.
“We’ve had contractors use our product on above-ground parking garages, and basically wallpaper the failing concrete with 30-foot sheets,” says LaCroix. “It’s been used on pilings and beams for bridges and overpasses. It’s much less expensive than traditional remediation because it doesn’t involve jackhammers, closing lanes of highways, etc.”
In residential settings, sheets can be used to repair cracking near the corners of the foundation, or cracks emanating from doors and windows.
Fortress and Rhino make pre-preg, pre-cured corner straps based on steel plating systems. They follow ACI design guideline in being slightly less than 90 degrees. “The advantage over wet lay-up systems is that the bend is certified in factory,” says Jackson.
Staples— For poured walls, carbon fiber staples can be a major benefit.
Significant cracks in poured walls are typically filled using low-pressure epoxy injection. Epoxy is stronger than the concrete, and literally glues the wall back together. Lou Cole, owner of Emecole, says the problem is that if any movement occurs, it will crack again at the concrete/epoxy glueline. Carbon fiber staples can eliminate the problem.
Emecole offers carbon fiber crack repair staples measuring 10” long and 3/8” wide with 1” leg. Cole says they add very little cost to entire crack repair, and install in five minutes. Just mark off the series of holes perpendicular to the crack line, and epoxy them into place when the crack is being injected.
“The staple becomes the friend of the foundation repair contractor for one good reason: It dramatically reduces call-backs,” says Cole. “By adding carbon fiber staples to the repair, it transfers load away from the glue line.”
The problem is that if the wall shifts at all, and there are no staples, it will crack right next to the glueline. Even though it’s a new problem, it’s often considered a “call-back” for the contractor because it’s so close to the previously repaired one. Staples transfer the load away from the repair, so the homeowner can see that it’s a new problem, not a re-appearance of the old one.
Cole says, “By adding a few staples it becomes an opportunity, not a callback.”
Profit Potential
While carbon fiber products may cost more than traditional materials, they save so much in other expenses that they can usually be bid quite cost effectively. No messy equipment, no concrete, no heavy steel beams. No excavation.
Thompson notes that the homeowner will save additional money if the basement is ever finished, and have an easier time selling the home if he ever chooses to move.
“Instead of a 4- to 6-inch I-beam, this is the thickness of a dime,” he says. “Aesthetically, your options are still virtually unlimited. You can paint it, furr it out, or just leave it the way it is. I hear from customers, if they go to a basement and see beams, they think there’s a problem. If they see carbon fiber, it’s less of a detriment.”
Many of the products discussed in this article come with a lifetime warrantee. A few are fully transferable if the home is sold.
Fall 2010 Back Issue
$4.95
Underslab Radon Barriers
Working With Carbon Fiber
Roof Pitch and System Selection
AVAILABLE AS DIGITAL DOWNLOAD ONLY
Description
Description
Underslab Radon Barriers
In some areas of the country, radon barriers—a variation on the underslab moisture barrier—are a great way to improve the livability of the building and add additional income to the company’s bottom line.
Working With Carbon Fiber
Stronger and less bulky than steel, carbon fiber is making basement structural repair easier than ever before. Whether its carbon straps, staples, or sheets, we explain what the options are, and how to make sure they’ll perform.
Roof Pitch and System Selection
Flat roofs obviously require different treatment than steep ones. We’ll look at the role roof pitch plays in determining how a rooftop waterproofing membrane will perform.
Additional Info
Additional information
Magazine Format | Digital Download Magazine, Print Mailed Magazine |
---|
Trackbacks/Pingbacks