By Melissa Morton
The problems in a house with a crawlspace—mold, wood rot, pests, cold floors, buckling hardwoods—all can be linked back to moisture problems in the crawlspace.
The old school of thought of adding more vents to circulate outside air through the crawlspace does not fix the moisture problems but actually makes them worse. Ultimately, closing the crawlspace (eliminating the outside vents and lining the ground and walls with a vapor barrier) controls the moisture and is the solution to the crawlspace problems.
Research
Advanced Energy’s pilot study in 2005 gave the industry hard data backing a closed crawlspace system. This North Carolina field study found homes with closed crawlspaces saw energy savings of more than 15% a year on average for heating and cooling. They were also dryer than traditional wall-vented crawlspaces with average daily relative humidity controlled below 70%. This study changed North Carolina’s building codes adding the basics of how to properly close a crawlspace. See the full report on www.crawlspaces.com.
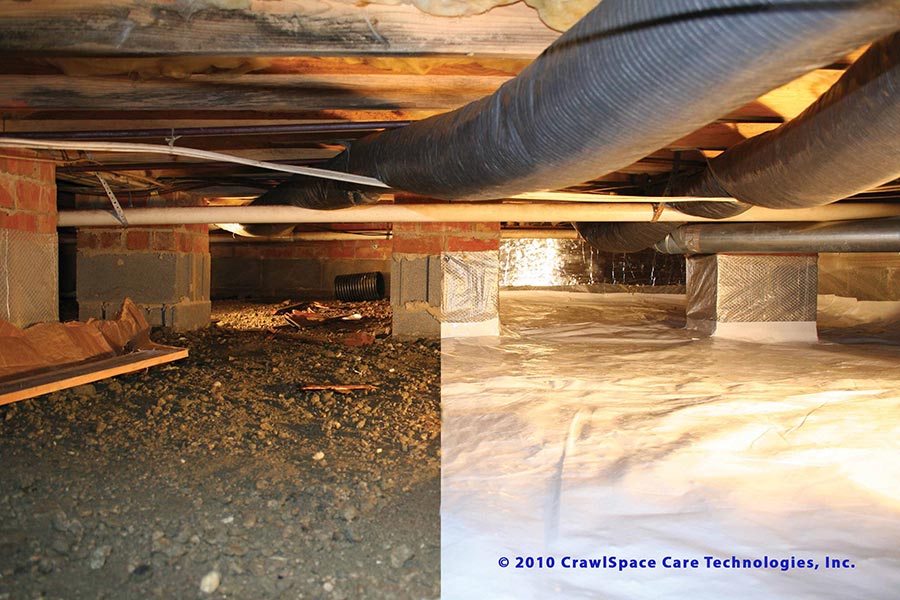
When properly installed, enclosed crawlspaces are cleaner, brighter, and more energy-efficient than traditional vented spaces.
Advanced Energy did another federally-funded study in 2009 with test sites in Baton Rouge and Flagstaff.
“In Baton Rouge, the results were very clear that closed crawl spaces dramatically affect relative humidity,” says Cyrus Dastur, building scientist at Advanced Energy. The Baton Rouge closed crawl space systems controlled crawl space relative humidity closer to 60% on a daily average, while the control group humidity hovered around 80% for most of the spring and summer months.
In Flagstaff’s dry climate even the vented crawl spaces stayed under 70% for all but a few days, but the closed crawl spaces were even drier, with levels around 50% under the same conditions.
Energy savings were dramatic in Flagstaff. The Flagstaff homes with closed crawl spaces and floor insulation saved nearly 20% in natural gas during the winter and a 15% annual energy savings compared to the control group.
An unexpected finding was an increased level of radon in homes with closed crawl spaces in Flagstaff. The elevated level was above the EPA action level so the Flagstaff study was actually discontinued early, says Dastur. “The EPA action level is 4 PPL,” Dastur explains. “The houses with closed crawl spaces were measuring 11, 17, and 22 PPL. That was a situation we wanted to eliminate.”
The soil type in Flagstaff already has a high level of radon. “Gas is hard to block,” Dastur says. “It was just a good warning for everyone to test for radon.”
If your customer wants the energy savings, include a radon mitigation system with the closed crawl space installation.
Dealing with the Water
There are two types of water problems in a crawlspace: flowing water and moisture. “Before you even can talk about closed or vented, you have to deal with the liquid water first,” says Bruce Davis, Advanced Energy’s project director on the first study.
Advanced Energy recommends adding interior and exterior drains for the crawlspace. Crawlspace drains should be separate from the foundation drains.
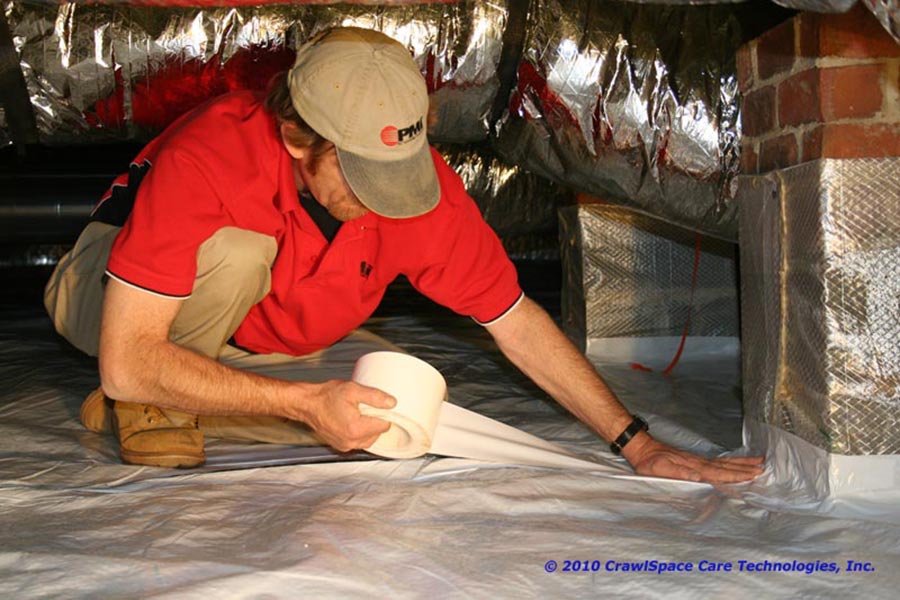
Vapor proof seams and detailing are an essential component of the closed crawlspace.
Mike Trotter, owner of Trotter Company, recommends first making sure the yard and pavement outside slope away from the crawlspace and if seepage is still found after rain, installing interior perimeter drains leading to a sump pump. “Some crawlspace contractors say you only need a sump pump in the low point of a crawlspace for the drainage to be effective,” Trotter says. “If you don’t put drains around the crawlspace perimeter and just let the water flow to the low areas of the crawlspace, you are asking for the building to settle. Unmanaged water will weaken the soil and in some cases undermine the foundation.”
Trotter says you should never allow storm water to flow or pond against the outside foundation wall. “Good exterior drainage is the first requirement of a crawlspace system,” Trotter says.
Closing the Crawlspace and Liners
Once you have dealt with the potential of liquid water coming into the crawlspace, you can deal with the moisture. Moisture or dampness comes into a traditional crawlspace from either the ground or the crawlspace vents. This is where closing the vents and adding a vapor barrier liner comes in.
Some contractors use vent covers to close the vents while others replace the vent with a cinder block. Once they close the vents, they add a vapor barrier to the ground and the walls. “Sealing or encapsulating a crawlspace you have to install the liner up the walls, not just the floor,” says Dan Fitzgerald, Basement Systems, Inc..
The Advanced Energy research shows the minimum thickness required to stop the moisture is a 6 mil polyethylene liner. While a good 6 mil liner will do the job of controlling moisture, it is not going to hold up to much work under the crawlspace. The mil or thickness (1 mil is equal to 1/1000 of an inch) is more about durability.
Tom Saucier, owner of Crawlspace Doctor, says within the whole crawlspace liner world there are not a lot of different liners. Few companies actually produce their own liner. “If installed properly any liner is going to work,” says Saucier. “Most liners look exactly the same if you didn’t see the name. They are usually white polyethylene and string reinforced. The only difference is the thickness or the mil.”
Contractors most commonly use 12- to 20-mil but there are liners all the way up to 60-mil. Emecole makes a 60-mil, lightweight polyethylene foam backing liner. “Usually, the thicker the liner the heavier,” Saucier says. “The thick 20-mil liner is heavy and hard to work with. It is like trying to lay carpet in the middle of the woods. With that logic you would think Emecole’s liner would be heavy but it’s not. Emecole’s 60-mil liner is a dream to work with. It is the ease of use that makes it so nice. It just lays itself.”
The Crawlspace Doctor works mostly in the south eastern states but he sees various climates and types of crawlspaces. “We use all the products from the 10-mil clear liner to Emecole’s 60-mil liner,” he says. “It depends on the circumstance. The different climates, soil conditions, and flood stages make it nearly impossible to use just one product in all the different regions of the country.”
For example, in Michigan the majority of homes have basements below the frost line. If they have a crawlspace it is under an addition to the side of the basement. It is usually about 400-500 square feet with no outside access. The homeowner is going to be more likely to want to store boxes in this type of crawlspace. “So, we would want to install the thickest, most durable liner that would withstand storing boxes and a lot of traffic,” Saucier explains.
“In Southern Indiana, most houses have crawlspaces. The footers are deep in the ground and the crawlspaces are hard to get to. There is usually a well access and most people will never go down there. Do you think they are interested in storing boxes down there? No. “This customer doesn’t need a high durability liner so why would you sell them a product they don’t need?” he asks. “A 10- mil liner will keep out the moisture just the same as a 20-mil liner as long as it is installed properly and it will be cheaper for the customer.”
In Georgia, almost every foundation has footers level to the ground. They have an access door to the crawlspace typically 3-feet by 3- feet and ceilings 4 feet high. “This is unbelievable storage,” says Saucier. “There was one customer who was storing five canoes in his crawlspace. Now, this guy needs a durable liner that can handle storing five canoes!”
“In the liner world, if they are installed properly they are all going to work to control moisture. The question you have to ask is ‘How are you going to use the space after it is finished? What is going to be the end result? Do you ever want to see it again?”
Dehumidification
Basement System’s Fitzgerald says there are four steps to properly closing a crawlspace:
Drainage, Closing the vents, Total Encapsulating Dehumidification.
Most contractors do add some sort of dehumidifier to the crawlspace however that also depends on the climate. Advanced Energy’s researcher Davis says they have run into problems where the relative humidity under the house is actually too dry. “You can over dry a crawlspace,” he says. “If the wood moisture content is drawn down from 60% to 5% you will definitely see shrinkage and cracks in the floor. That is an extreme difference in relative humidity.”
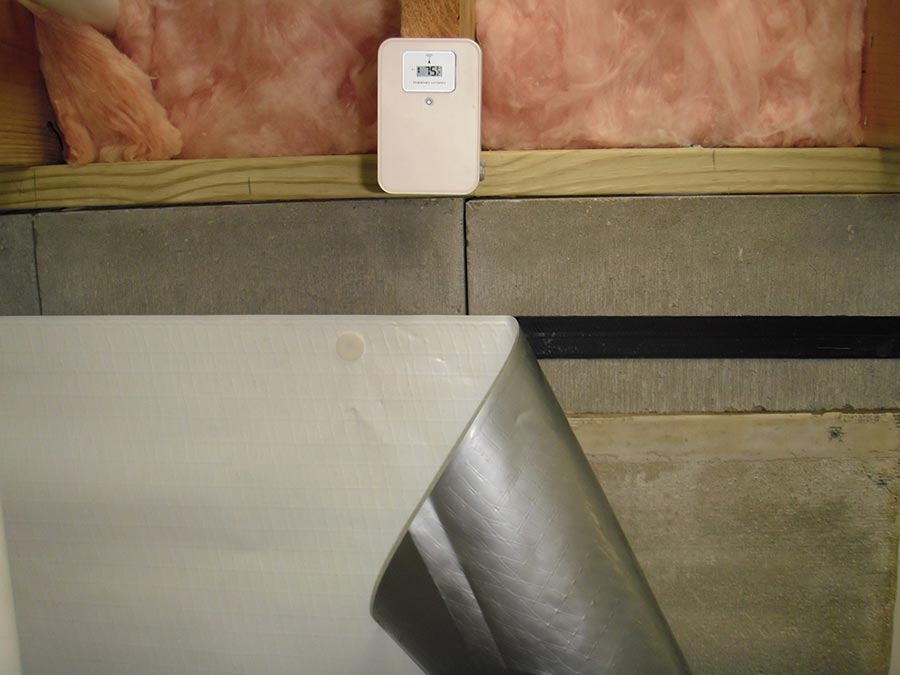
Moisture monitors and radon detectors are useful additions to crawlspace encapsulation jobs.
Davis says Advanced Energy did use a dehumidifier in its research. However if the seams are seald and do all you can to seal the crawlspace completely, the less you will have to do to control the moisture mechanically. It is good practice to place a meter in the crawlspace that will monitor the relative humidity for the homeowner. “There is a radio frequency receiver meter available that can show the consumer the temperature and relative humidity in the crawlspace,” he says. “It shows them when to be concerned and when to add more dehumidification.”
Insulation
In general it is a good idea to insulate the crawlspace. “Whether you insulate the floor or the wall, insulate well,” says Davis. “Don’t let it fall out. “
Davis says the Advanced Energy studies show, in mixed climates like North Carolina, insulating is a wash on energy savings. “However in an area like Baton Rough where it is hot, insulating the walls seemed to have an edge on cooling costs,” he explains. “Where in cold climates, (like Michigan) insulating the floor achieved better energy savings.”
Lou Cole, owner of Emecole, says the biggest shift in the crawlspace industry is that the code is moving to regulating the insulation. If designed right, the Emecole’s crawlspace liner can actually be used as an insulation product itself with an R-value of 4.
Pest Control
Another benefit of a closed crawlspace system is that lowering the wood moisture content lowers insect infestation. Advanced Energy studies saw a 70% reduction in insects.
Billy Tesh, owner of Crawlspace Care Technologies, partnered with Advanced Energy on both crawlspace research projects. Pest control management professionals spend a lot of time in crawlspaces and Tesh saw his share of moisture problems. “We went into crawlspaces that were sweating profusely and the floor joists were rotting,” says Tesh. “Adding more vents did not fix the problem.”
Tesh went to a meeting in 2002 where Advanced Energy was presenting the idea of closing the crawl. “I thought, ‘This is exactly what we need,’” Tesh says. Advanced Energy was looking for contractors to help with the project and Tesh got involved. “I wish I could say that a closed crawlspace was my brain child, but it wasn’t,” Tesh says. “We were just fortunate be involved in the study and learn from Advanced Energy.”
The Stinky Crawlspace
After the crawlspace is closed, some contractors (especially ones new to crawlspace work) may get a callback about odors in the house. Matt Leech, owner of CrawlSpace Concepts, LLC, a nationwide installer network and manufacturer, says they realized that when they closed the crawlspace the soil started acting as it did before the house was there. The soil continues to decompose whatever is in the soil and the off gases rise to the level of the soil and seep into the crawlspace. Leech says their philosophy to fix this problem of a “stinky crawlspace” is to install a vent pipe and fan similar to a radon mitigation system to flush the soil gases to the outside of the house.
This is also another reminder to test for radon and other soil gases to protect the homeowner from harmful gases they can’t smell.
Diversifying Your Business
Since Advanced Energy released the 2005 study results, the crawlspace industry has been forever changed. “We knew there were issues with vented crawlspaces and that is what we were trying to address,” Davis says. “We didn’t know it would turn out to be so business friendly.”
Davis explained that the practicality of the work became beneficial to various industries.
“Waterproofers could get into it. Pest control industries could get into it. Heating, Venting and Air Conditioning contractors could get into it. General contractors, builders and various construction industries could get into it,” he says. “And they all have.”
Closing crawlspace work is especially appealing for waterproofing contractors. “I believe crawlspaces are a great business to get into,” says Trotter. “Virtually, every crawlspace needs to be closed and lined.”
Thanks to Trotter, who challenged a patent on lining crawlspaces in 2008, every contractor can line and close crawlspaces without fear of patent infringement.
“It is our birthright to put liners in crawlspaces,” Trotter says. “Just do your research. Check for radon. If there are gas appliances in the crawlspace, design it to provide make up air. Protect your customers and this can be a good business for you.”
Spring 2011 Back Issue
$4.95
Waterstops, How and Why
Project Profile: Vancouver Library
New Data on Enclosed Crawlspaces
Spray-on Coatings for Above-Grade Work
AVAILABLE AS DIGITAL DOWNLOAD ONLY
Description
Description
Waterstops, How and Why:
Long used for heavy commercial work—especially in tunnels and retention ponds—waterstops are becoming more common for waterproofing light commercial jobs as well.
Project Profile: Vancouver Library
As innovative as it is green, this project showcases a wide array of new waterproofing technologies, from the integral waterproofing in the foundation to the green roof fifty feet above grade.
New Data on Enclosed Crawlspaces
As energy efficiency has become a top priority for homebuilders, enclosed crawlspaces are becoming more common. But the contractor must be careful to avoid the condensation and mold issues that can become problematic in poor quality installations.
Spray-on Coatings for Above-Grade Work
Recent developments in spray-applied coatings make them a top choice for above grade work. Compare the advantages, and find the product that’s best for your next job.
Additional Info
Additional information
Magazine Format | Digital Download Magazine, Print Mailed Magazine |
---|