Mechanical waterstops come in a wide variety of materials, profiles, and sizes.
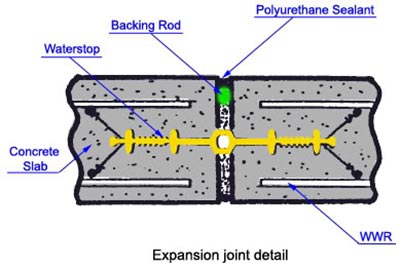
Waterstops are fastened to rebar or form ties to prevent movement during the pour. Ribbed or dumbbell-shaped profiles maximum water-sealing performance. Profiles with a “bubble” in the middle are best for joints with lots of movement.
In many cases, concrete structures are only as watertight as the waterstops used in them. Installed in expansion joints, cold joints, and other seams, they’re available in a wide variety of shapes and types.
Concrete, like all materials, expands and contracts when the temperature fluctuates. To accommodate that change, expansion joints are installed at regular intervals throughout the slabs and walls. And if expansion joints aren’t installed properly, the structure will crack along natural weak points, primarily cold joints and seams. These joints, unless they’re sealed, are likely to allow water into the structure.
That’s why nearly all large-scale concrete structures—water treatment plants, reservoirs, locks, dams, and below grade facilities—usually have waterstops installed during construction.
Residential jobs sometimes use waterstops as well, but usually only at the cold joint between the footer and the foundation.
Selecting a Waterstop
Waterstops could be defined as “a section of flexible waterproof material placed at any joint in concrete to prevent the passage of water.”
Greenstreak, a marketer of concrete construction products with a comprehensive line of waterstops, explains on their website, “Several factors must be considered when selecting a waterstop. They include, but are not limited to, joint type and joint movement, hydrostatic pressure and chemical exposure.”
In order to make sure that the waterstop will perform adequately, they recommend that specifiers verify the following:
- Structure type
- Chemical containment requirements (if any)
- Head pressure requirements
- Joint types
- Joint movement requirements
Types
Literally dozens of different waterstop designs are currently on the market, made from a wide range of materials. However, they can be grouped into two categories, depending on whether the joint is expected to move.
Non-Moving Joints: For non-moving joints, such as the cold-joint between a footing and foundation, hydrophilic waterstops may be a good choice. Most products in this category used expanding Bentonite clay as the active component. The others use materials with similar properties. Hydrotite, for instance, uses a non-Bentonite, modified chloroprene rubber, and Duro-Seal uses an acrylate polymer.
The architectural data sheet for PolyStop, another brand of hydrophilic waterstops, notes that, thanks to its non-Bentonite formula, “controlled swelling cuts risk of concrete spalling and reduces the possibility of premature expansion.”
In any case, all of these products work on a similar principle: Exposure to water makes the material expand dramatically, enough to create a compression seal and stop water from penetrating the joint.
Application technique is usually a simple matter of fastening the rubber strips in or along the joint. Again, because this seal is easily broken, hydrophilic waterstops are suitable for non-moving joints only.
There are few other products on the market designed to seal non-moving joints, although they’re not technically waterstops.
Mastic “waterstops” are basically a joint-sealing flashing. They’re applied with a primer adhesive along the joint to create a self-sealing moisture barrier.
Crystalline products are also sometimes used to waterproof non-moving cold joints. They’re roller- or spray-applied between pours. In the presence of water, the material produces millions of microscopic crystals which grow large enough to seal the joint.
Finally, Fuko Injection Waterstops are installed like a crack-injection or grouting operation, in which super-fine cement or epoxy resin is injected into the joint to seal all cracks and voids in the area. Once again, it’s not a traditional waterstop, but it does seal non-moving joints very effectively.
Joints With Movement: Moving joints require mechanical waterstops, the type that spans both sides of the joint to create a diaphragm. When designers and specifiers are speaking about waterstops, they’re usually referring to mechanical waterstops.
Manufacturers offer a huge variety of mechanical waterstops made from a wide variety of materials. Stainless steel and copper are two options. PVC and rubber are even more common.
According to Greenstreak, “PVC’s outstanding physical properties, excellent inherent elasticity and resistance to many waterborne chemicals has made it the most widely specified waterstop material.” Alternatives to PVC include neoprene and rubber.
Regardless of the material or manufacturer, installation of a mechanical waterstop must be done before the concrete is placed. One side of the stop is embedded in the concrete during the first pour, with the other side temporarily exposed. When the next pour is made, the other half of the waterstop is encased in concrete. The centerline of the waterstop should be aligned with the center of the joint.
Obviously, keeping the waterstop in place, with no folding or movement, requires considerable attention to detail. Usually it is fastened to the vertical rebar or form ties to keep it in place. During the pour, workers must ensure good consolidation around the waterstop, as voids next to the waterstop can significantly compromise its water stopping ability. Horizontally placed waterstops in slabs require particular attention, as it’s difficult to get concrete to flow into the gap between the bottom of the stop and the top of the forming bed.
Most waterstops are ribbed, or have a thicker “dumbbell” of material on the ends to keep them in place and ensure maximum water-sealing performance. Profiles with a “bubble” in the middle of the strip are best for joints with lots of movement.
Uses
The range of projects where waterproofers may encounter waterstops covers virtually all types of commercial construction, as any concrete structure that retains water, or needs to exclude water needs them as part of the larger waterproofing system.
Besides the obvious candidates such as dams, canals, water reservoirs and aqueducts, there’s bridge and deck abutments, culverts and tunnels. They’re even more important in environments with heavily polluted water or corrosive chemicals , such as wastewater treatment facilities, or the primary and secondary containment structures surrounding refineries, sludge ponds, tank farms, and so forth.
Summer 2018 Back Issue
$4.95
Livable Basements
AVAILABLE AS DIGITAL DOWNLOAD ONLY
Description
Description
Additional Info
Additional information
Magazine Format | Digital Download Magazine, Print Mailed Magazine |
---|
How do you recommend you form the slabs you have shown in the expansion joint detail above? So that the bulb waterstop is centered where it is intended, and both above and below the waterstop is a formed surface