When selecting an underslab barrier, the product’s thickness isn’t the only variable. Performance characteristics—like moisture protection, strength, and longevity—as well as labor and price considerations should be weighed carefully.
In today’s high-performance buildings, underslab vapor barriers have become almost mandatory. Vapor retarders save money and energy by controlling moisture and gas migration through concrete slabs and foundations. They’re also an essential part of any methane and/or radon mitigation system.
Because the primary purpose of vapor retarders is to reduce or eliminate moisture transmission, most of the attention in differentiating barriers is on their thickness, or millage. (One mil is 1/1000 of an inch.) But a close look at the standards reveals that selecting a vapor barrier involves far more than only millage.
Glenn Tench, director of marketing at W. R. Meadows says, “Two properties are equally important when selecting an underslab barrier, and neither of them is millage. It all comes down to permeance and durability.”
Bret Houck, director of business development at Stego Industries, explains, “Specifiers are looking for products that will provide the protection level needed to protect the most sensitive flooring materials, the strength characteristics to make it through the installation activities without too much damage, and the longevity to maintain the necessary protection level for the life of their clients’ buildings.”
To produce these three character-istics—moisture protection, strength, and longevity—at an affordable price point, manufacturers use a wide variety of manufacturing techniques and materials.
Dario Lamberti, product manager at Insulation Solutions says, “One of the most difficult decisions you can be faced with is trying to compare products as true alternatives to each other. Thankfully, testing procedures allow you the ability to compare physical properties side by side.”
Permeability
Obviously, one of the major considerations in selecting a vapor barrier is it’s permeability, or permeance. ASTM (American Society for Testing Materials) has two separate standards for underslab barriers. The more stringent ASTM 1993 is for bituminous membranes. For plastic film vapor retarders, which are the subject of this article, ASTM 1745 sets the minimum requirements. It divides materials into three different classes (A,B, and C), with Class A being the most robust. Surprisingly, the permeance rating is the same for all three classes (0.1 perms).
Most manufacturers far exceed this minimum standard, though. W. R. Meadows’ Perminator, for example, claims a perm rating of 0.0043 for its 10-mil sheet. That’s twenty times lower than required for a Class A barrier. Insulation Solution’s VaporCheck II claims a perm rating of 0.0073 for its 10-mil sheet.
Tench says, “Perm ratings are more geared toward the water vapor aspect of it, but there are also situations where you’re going to want a sheet that can capture methane, radon, and other soil gasses. There are other independent tests for methane, radon, and other gas resistance, but for the most part, a low-perm barrier is also going to resist other gasses.”
To determine the exact perm rating of a particular product, check the manufacturer’s spec sheet, available on their website.
Puncture Resistance
If all three ASTM classes have the same permeance rating, what’s the difference between Class A and Class C? It’s their durability, as measured by their tensile strength and puncture resistance. These are two essential considerations if the membrane is to perform as expected.
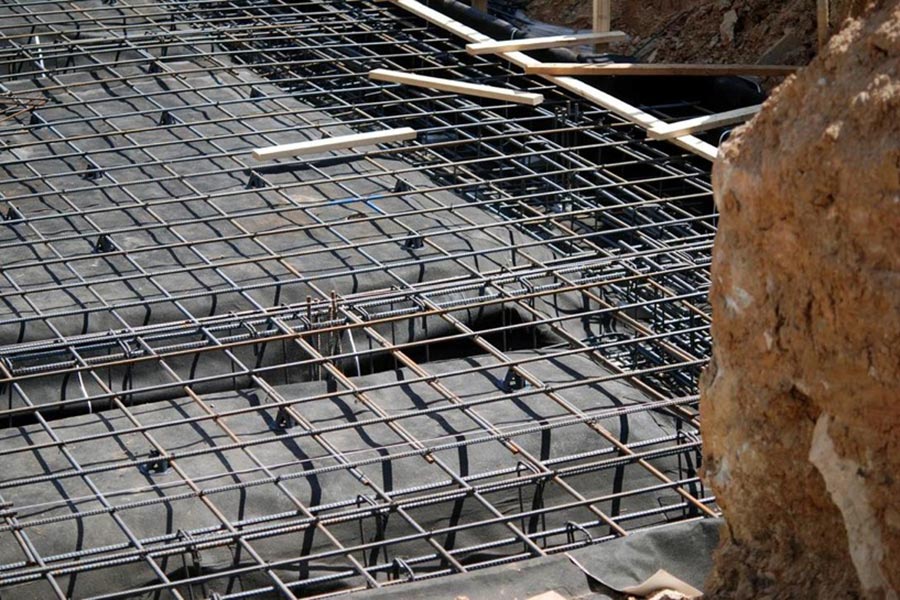
The effectiveness of any moisture barrier plunges to zero when punctured, so special care needs to be taken in jobs that call for heavy rebar (behind) and extensive penetrations (right).
Bryan Coulter, vice president at PolyGuard Products, explains, “On any jobsite, you’re going to have rakes, exposed rebar, wire ties, and foot traffic. In some cases there’s vehicular traffic on the membrane. Your underslab barrier has to be able to stand up to real world conditions.”
Lamberti adds, “If a membrane gets punctured during installation, it’s worthless. The lowest permeance rating in the world isn’t going to do any good if the membrane is full of holes.”
Several years ago, in preparation for writing ACI 302.2, the American Concrete Institute tested how small tears in an underslab barrier affected performance. Tench reports, “They took a standard moisture barrier, and measured the vapor emission rate. Then they punched a 5/8-inch hole through the sheet, like what you’d get with rebar. The test showed that a small hole like that basically rendered the entire barrier ineffective.”
Barriers are tested by dropping a bullet-shaped weight onto an unsupported section of membrane. ASTM 1745 Class A barriers must demonstrate a puncture resistance of 2,200 grams—almost five pounds. Class C barriers must withstand a weight of about 1 pound (475 grams).
Once again, many underslab products far exceed the Class A requirements. The exact specification for any individual product is available on its’ data sheet.
Strength
Closely associated with a barrier’s puncture resistance is its tensile strength, or ability to withstand tearing. “A vapor barrier’s strength is just as important is puncture resistance,” affirms Tench. “Once again, it a matter of being able to stand up to conditions on the jobsite.
ASTM agrees, setting different strength requirements for each class of barrier. Class A materials must have a tensile strength of 45 lbs./inch; Class C barriers must have a tensile strength of 13.6 lbs./inch.

This photograph, taken during construction of the Fairplex Conference Center, adjacent to the Los Angeles County Fairgrounds, shows why membrane durability is important. This underslab barrier—Perminator from W.R. Meadows—had to withstand foot traffic, heavy steel schedules, multiple penetrations, concrete vibrators, and even the weight of the pump truck.
Manufacturers use a variety of techniques to ensure their products will function as intended. Some make a thicker sheet. Others use higher quality resins. Many use some sort of reinforcement.
For instance, Reef Industries’ Griffolyn vapor barriers are reinforced with heavy duty polyester cord. Other products are “core-grid reinforced” with a layer of high-density polyethelene (HDPE). Insulation Solutions’ VaporCheck features a cross-woven core made of tough polyethylene strands sandwiched between two polyethylene extrusion coatings.
“Any type of reinforcement is going to increase the strength,” he admits. “Whether it’s string reinforced, cross-woven, or core-grid reinforced, all will offer good strength.”
Insulation Solutions also makes VaporCheck II, which uses a different approach: virgin resins formulated for strength and longevity.
Tench, at W.R. Meadows, agrees that a manufacturer’s choice of resins does play a major role in the end product’s strength. “The toughness of the vapor barrier comes from the material makeup,” he says. “Polyolefin resins, like we use in our Perminator product, have twice the strength and puncture resistance of some major competitors.”
PolyGuard’s UnderSeal uses yet another approach. While most barriers are between ten and 20 mils, their sheet measures 95 mils thick, with multiple layers and materials to ensure outstanding performance. The product has a puncture resistance of 310 lbs., which is 64 times higher than the Class A vapor barrier requirement.
On the bottom of the “sandwich” is a 20-mil polyethylene sheet, which is topped with a 55-mil layer of a proprietary asphalt-based sealant. A 20-mil non-woven geotextile fabric serves as the top surface. Coulter explains, “When the slab is poured, the slurry will work its way through that geotextile, so the membrane is actually mechanically bonded to the slab. As long as there are no voids at the time of the pour, it won’t matter if some settlement occurs later. Additionally, the heat created by the hydrating concrete will soften the waterproofing layer, so it will self-heal around small punctures like nail holes. We issue a warrantee for waterproofing integrity with this product.”
Longevity
One final concern related to durability is how well the material will hold up over time in the underslab environment.
“Any material manufactured from virgin resins is going to hold up better than those than use recycled materials,” says Lamberti. Products with a higher percentage of virgin material will outlast those with lower percentages.”
Some manufacturers, like Cosella-Doerken’s Delta-MS Underslab, use recycled materials for the membrane core, sandwiched between two layers of virgin resin. This approach provides some recycled content—important to green building certification programs like LEED—while mimicking the performance of products made from all virgin materials.
A few manufacturers used polyolefin resin, a high-performance polyethylene. In accelerated aging tests, this state-of-the-art material has proven to have outstanding longevity.
Virgin resins and high-tech materials cost more, but manufacturers say that it’s worth the extra cost.
“We see very little Class C or even class B material being specified,” says Tench. “The cost differential is insignificant.”
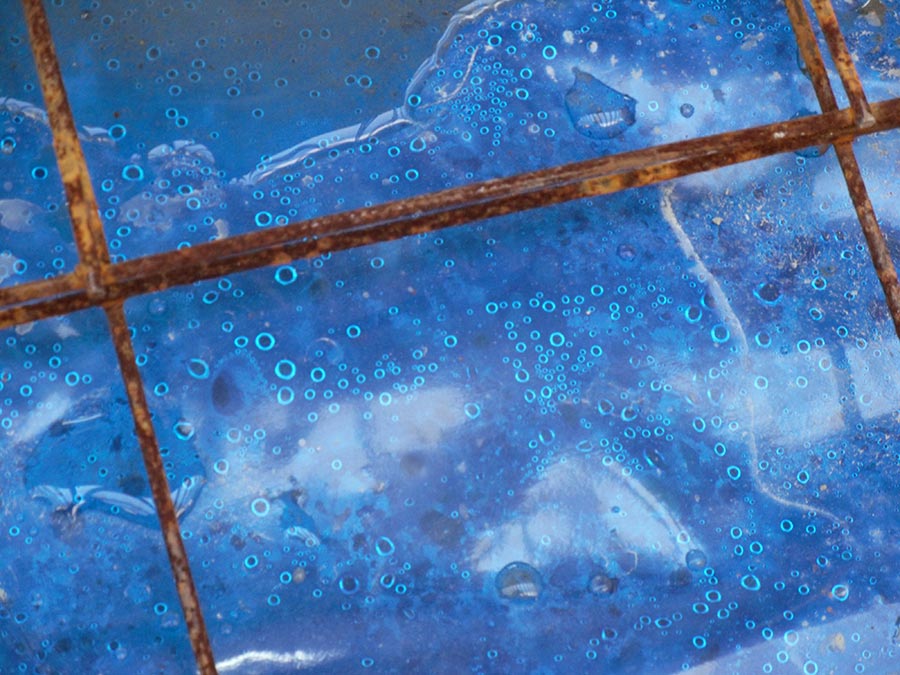
A properly installed membrane can repel not only water, but methane and radon as well.
Labor Considerations
Speaking of price, labor considerations should be considered when selecting a membrane. Large rolls—typically 15’ by 200’—can be unwieldy for small residential jobs, but they’re great for commercial work. Not only do they make it easy to cover large areas quickly, but they can greatly reduce the amount of taping required. Some manufacturers go a step further, and include a pre-taped seam along the edge of each roll. It’s just a matter of setting the overlap and peeling off the protective paper. If the slab will have multiple penetrations, it may be useful to select a product line with detailing accessories such as pipe boot kits.
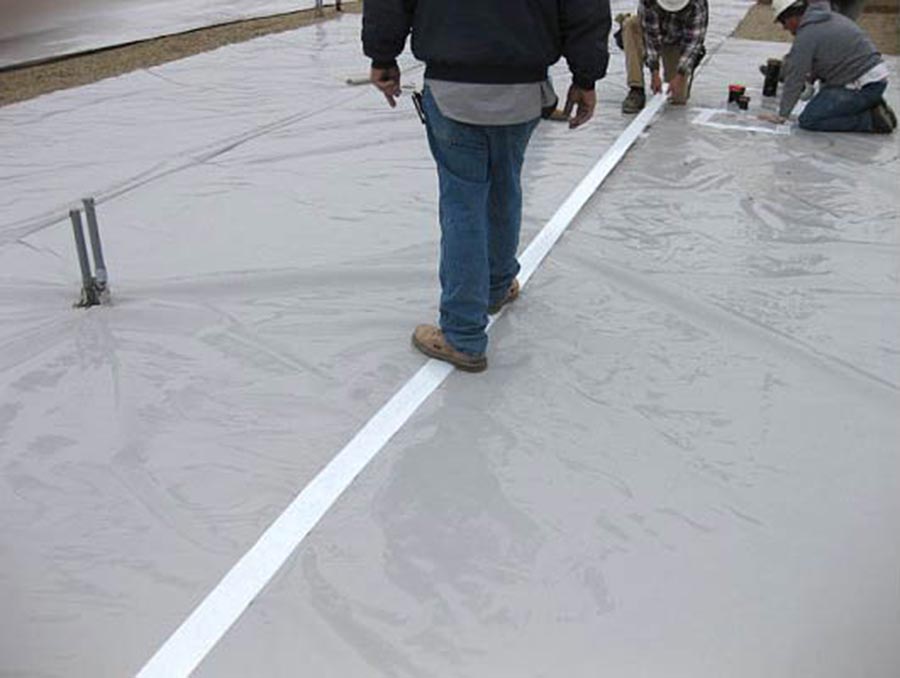
Labor considerations, like the size of the roll (right) and how easily the seams are sealed (center), should be taken into account.
Houck, at Stego, summarizes, “The main characteristics of performance are the quality of materials used to make the material, the quality control during the manufacturing process, and the proper installation techniques for the specific project design.”
Spring 2012 Back Issue
$4.95
Underslab Barriers: Does Millage Matter?
Wind and Fire Standards for Living Roofs:
Taking Your Business Commercial
Sealed Crawlspaces: Concrete vs. Plastics
AVAILABLE AS DIGITAL DOWNLOAD ONLY
Description
Description
Underslab Barriers: Does Millage Matter?
The thickness of an underslab moisture barrier is frequently used as a gauge of performance. But other factors, such as tensile stregnth and puncture resistance are just as important.
Wind and Fire Standards for Living Roofs:
By Kelly Luckett
New standards define what’s needed to keep living roofs safe from wind damage, and prevent the spread of fires. They also prove that green roofs have overcome the final hurdle for acceptance by the design community.
Taking Your Business Commercial
By Melissa Morton
Project size, opportunities, ad profits are all larger in the commercial sector, but so are the risks. Three contractors who have made the leap successfully discuss what you need to know before your residential waterproofing business starts bidding on commercial work.
Sealed Crawlspaces: Concrete vs. Plastics
The new trend in basements is to seal crawlspaces from outside air and soil moisture. The two most popular methods to seal the floor each have unique considerations that if not considered may aggravate moisture problems.
Additional Info
Additional information
Magazine Format | Digital Download Magazine, Print Mailed Magazine |
---|