New drainage options for synthetic turf fields reduce downtime after storms and improve player safety during games.
We’ve all witnessed sporting competitions cancelled because of rain. And whether it’s Major League baseball or a junior-high football game, rainouts are a hassle. At the college and professional level, they can create financial losses of tens or even hundreds of thousands of dollars.
That’s why designers go to such lengths to engineer sophisticated field drainage systems to speed the flow of water off the field. This article focuses exclusively on drainage for synthetic turf surfaces.
Multiple Solutions
There’s no single answer to how the job should be done. “You get as many different opinions as people you ask,” says Greg Wood, product manager at Colbond. “Everybody does it differently, and a lot of it depends on where you are geographically and the individual architect.”
Climate and rainfall play a major role in system design, as does the budget.
“It used to be that you’d get a bond for building a field,” says Brian Oliver, National Product and Sales Manager, Sport Division at JDR Enterprises. However, the bond market is so depressed right now that they’re forced to use fundraisers. Costs are extremely tight on most projects, so if you can build a better field at a lower cost, it translates to a huge advantage.”
Jim McAffee, a Texas A&M professor that specializes in optimizing field performance, uses these criteria in selecting a drainage system:
- How much water will need to be removed from the field?
- What is an acceptable time frame to remove this water?
- What types of soils are on the field?
- What is the budget for the drainage system on this field?
Grading
Synthetic turf installations are extremely exacting, and native soils introduce too much variability, so the first step in any installation is to excavate the site, usually to about 12 inches lower than the desired height of the final
playing surface. This is then carefully graded to exacting specifications, compacted, and graded again until the perfect slope is reached.
Athletes want the field as level as possible; gravity demands that the field have at least some slope to ensure drainage. As a compromise, the subgrade is usually sloped at 1% to 1.5%. On a football field that’s 50 yards wide, that translates to being nine to 12 inches higher in the center of the field than at the sidelines.
The crown can be like a turtle’s back—falling away in all directions—or simply sideline-to-sideline or endzone-to-endzone. Baseball fields are crowned with a subtle ridge extending from home plate over the pitcher’s mound to the outfield. Alternately, it can be graded with the ground falling away in all directions from the mound.
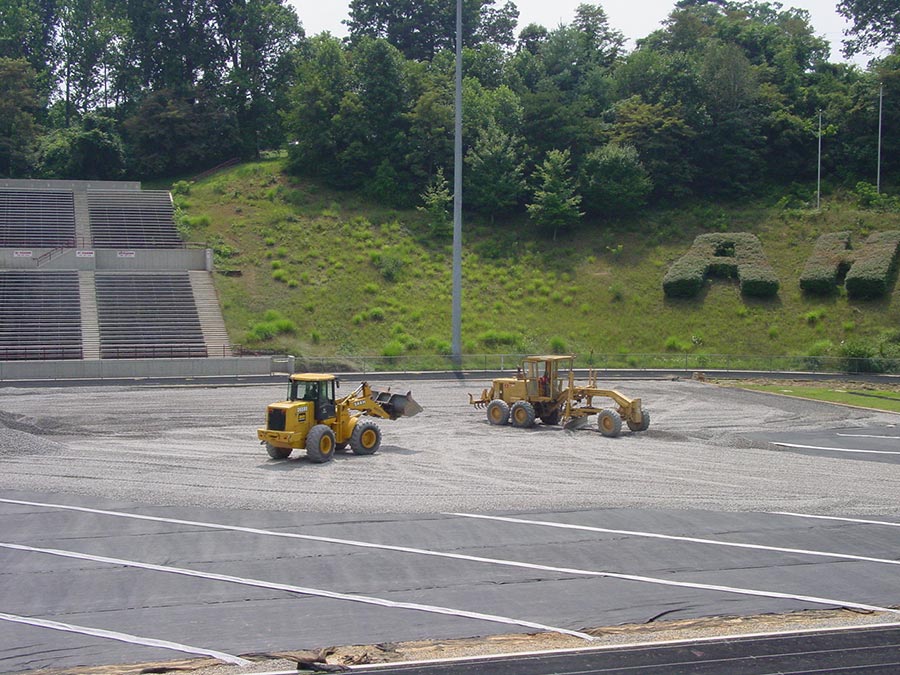
Between the sheet drain and the playing surface, a layer of course rock is installed, which has been carefully engineered to maximize drainage without compacting or shifting during use.
Regardless, this crown is built into the field at the sub-base to ensure water leaves the playing area. Oliver notes that the smoothness, or planarity, of the field is extremely exacting. “On a synthetic turf field, tolerance for planarity is +- 1/8 inch over 10 feet. The only way to get that kind of exactness is to use GPS- or laser-guided earthmoving equipment.”
McAfee says the importance of proper grading cannot be overemphasized. “The most common drainage problems I see are the result of poorly graded or uneven fields,” he says. “Improper grading may render the installed drainage system useless. Many times, the field is designed correctly and has enough slope to move water but the unevenness of the final grade causes water to pond or not get into the installed drains. Proper grading is the critical factor for a well-designed and installed field to drain efficiently.”
Strip Drains and Rock
After excavation, crowning, and compaction, workers install a geotextile fabric to ensure complete separation between the natural soil and the engineered system above it. In most areas of the country, a pervious liner is used. In regions with heavy clay or expansive clay soil, an impervious barrier, like a 20-mil PVC membrane, is sometimes used.
After the membrane or geotextile is in place, workers install perforated pipe around the perimeter of the field, and strip drains are installed in a herringbone pattern across the entire playing surface. Unlike natural turf fields, where the drains are installed vertically, on synthetic turf installations, the drains are laid with the widest dimension facing down. The exact dimension varies with the brand, but most are about a foot wide and an inch tall. Some installers physically connect the strip drain to the perforated pipe. Others rely on washed gravel to make the connection.
The zig-zag spacing of the drains depends on the climate. In arid regions like Southern California, the drains are laid out at about 20 feet on center. In wetter climates like the Northeast, spacings of 10 or 15 feet are common.
The drains are then covered with a layer of coarse rock, typically 4-8 inches of ¾” drain stone. Oliver notes that this drain stone is carefully chosen for an optimum mix of permeability and non-compaction. “It has to be fractured, and in some areas is not easy to come by, which is why there’s money saved on synthetic drain layers.”
The course stone is covered with a layer of finer rock to ensure that the field is as smooth as possible. Some field designers specify that the top playing surface of the field be dead flat; they claim that the sloped sub-base will move the water off the field. Others grade the top “choker” layer of stone to match the crown of the sub-base.
“That decision depends on the field owner, the turf manufacturer recommendations, and so forth,” says Oliver. “Both approaches are fairly common. In general, I think the flatter field is better from a playability standpoint.”
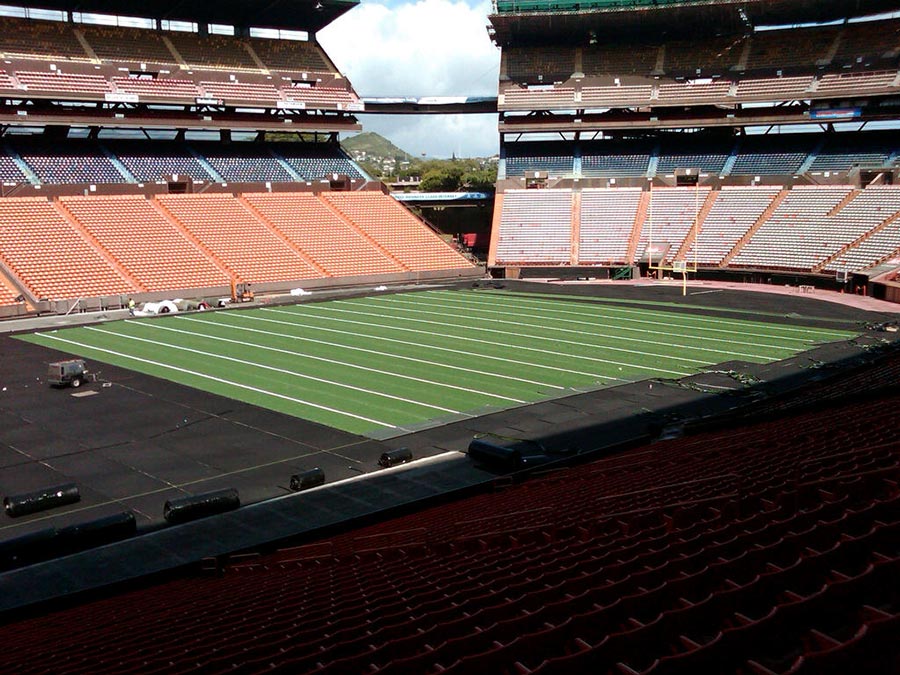
When Hawaii’s Aloha Stadium was renovated in 2011, J-Drain’s CoreTurf system was used for drainage. The new field is significantly safer, too, because the product made the field slightly softer.
Safety Considerations
In recent years, player safety has become a major focus of all levels of sports, and guidelines for shock absorption have been tightened considerably.
“Demand for under-turf shock pads has been growing exponentially over the last few years”, says Robin Gregory, marketing communications manager at Colbond, Inc.
“In Europe, it’s a very common thing. FIFA [the organization governing world soccer] has very strict guidelines for shock attenuation. In the U.S., field designers are becoming more interested in the shock pad due to safety concerns and litigation.”
Oliver says that as professional stadiums have lowered their maximum acceptable Gmax, college and high school athletic fields have followed suit. And since the vast majority of playing surfaces are multi-use facilities associated with public schools, virtually every field designer is now looking for ways to hit the desired Gmax range without compromising drainage rates.
Wood explains that ASTM standards have specified for years that playing surfaces should not exceed a Gmax of 200. However, many field designers prefer a Gmax much lower. “A well-maintained, manicured natural turf field will measure between 90 to 100 Gmax,” says Wood, “so that’s a standard that synthetic fields try to match. Some sports prefer a little harder surface, so 90-120 Gmax is a good number to shoot for.”
The standard method to achieve this figure is to install a shock pad, usually made of a pervious rubber, between the upper layer of rock and the turf. In these fields, the drainage challenge is usually trying to find a way to get the water through the shock pad into the drainage layer.
Some have approached the problem by adding rubber to the “topping,” an inch-thick layer of sand added on top of the turf to create traction for cleats and simulate the feeling of playing on real grass.
Gregory says her experience indicates toppings alone won’t get the Gmax low enough, “You’ve got to have some kind of shock layer under synthetic turf,” she says.
A Better Way
Recently, at least two companies have developed products that greatly simplify synthetic turf installations.
Gregory says, “What’s happening now is that instead of strip drains, companies are installing full field drainage systems.” Colbond has developed a new product, based on their signature entangled polypropylene mesh, that serves as both drain layer and shock pad. JDR Enterprises, makers of J-Drain, has developed a product with similar advantages that’s based on their dimple drain sheet.
Both drain exceptionally well—in excess of several hundred gallons per hour. In fact, they shift the drainage bottleneck to the turf itself, which is usually rated at 75-100 gallons/hr.
Colbond EnkaDrain ShockPad
The heart of Colbond’s EnkaTurf Drain is a half-inch-thick core of entangled polypropylene mesh fibers. This is sandwiched between two non- woven fabrics; one is polypropylene other is nylon-sheathed polyester. It weighs in at only 31 oz./sq.yd.
The product is laid out on top of the stone, but prior to the artificial turf. It not only eliminates the need for a separate shock pad, but also eliminates the strip drains beneath. “What it does is double as the drainage layer and shock absorbing layer,” says Wood, the product’s technical manager. “Depending on the final field design, there’s also the possibility of reducing the volume of rock needed.”
The product is so new that shock attenuation figures haven’t been finalized. But Wood says preliminary results are extremely promising. “We tried a 2:1 ratio of sand to rubber topping mix over concrete, and it gave us a Gmax of 125-130. The 1:1 ratio tested right at 100,” he reports. “We were using only one or two inches of infill, so it’s possible that this system could also save money by allowing for the use of a shorter synthetic turf.” The ratio’s weigh 4.5 lbs./sq. ft. and 5 lbs./sq. ft. respectively.
JDR’s J-Drain TurfCore
The J-Drain product has a number of advantages over stone-and-shock-pad systems. For starters, the system almost completely eliminates the need for specialized fractured stone.
“We’re able to use nearly all the native soil, because the TurfCore does all the drainage,” says Oliver. “Once the roots and organic matter are out, that’s usually all that’s needed. We can use soil stabilizers to stabilize the existing base and get a good compact surface. It eliminates a tremendous amount of excavating, hauling off, hauling in, and so forth,” he says.
The TurfCore system does use a 3” layer of Class 2 road base to get planarity, which is followed by TurfCore, which is installed in eight-foot wide rolls. The synthetic turf goes directly on top of the drain.
“By using a synthetic base, you can avoid a ‘choker layer’ which can clog the drainage,” says Oliver.
The CoreTurf system was used in the 2011 renovation of Aloha Stadium, site of the NFL Pro Bowl. Installed over the rock sub-base, it lowered the field Gmax by 20 points.
“Not only are you getting better drainage, but the product doesn’t clog like a stone base would,” syas Oliver. “It allows us to calculate drainage in advance, and guarantee to the owners what that drainage is going to be the first day, and ten years from then. With a natural stone base, the guarantee is usually one to two years. With our products, we offer a ten year warranty and the probability that the drainage system will last more than one turf cycle.”
The Future
With concerns about player safety, maintenance budgets, and sustainability, it seems that synthetic turf fields with combined drainage/shock-pad layers are the direction field construction is headed.
“Synthetic just has so many more applications,” says Wood.
These new drainage systems work equally well with new installations and on renovations of stone fields, and the older asphalt-sub-base systems. They reduce construction time, materials needed, and the carbon footprint of the installation.
As word of this type of product spreads, new applications are being discovered. Oliver says recreational areas and running tracks on rooftops are doubling or tripling every year.
Fall 2012 Back Issue
$4.95
Don’t Call the Game: Drainage Systems for Synthetic Turf Fields
Options for Finishing Basements
Waterproofing Techniques for Bored Tunnels
AVAILABLE AS DIGITAL DOWNLOAD ONLY
Description
Description
Don’t Call the Game: Drainage Systems for Synthetic Turf Fields
High-tech materials and creative engineers make it possible to keep teams on the field in otherwise impossible conditions. Some drainage solutions also improve player safety as well.
Options for Finishing Basements
By Ron Greenbaum
An acknowledged expert explains why it’s critical to verify a basement is dry before finishing it, and the basic components every basement finishing job should include.
Waterproofing Techniques for Bored Tunnels
Waterproofing bored tunnels deep below the surface is one of the most challenging jobs in the industry. The pressures, depths, and lack of repair options make doing the job right even more critical than usual.
Additional Info
Additional information
Magazine Format | Digital Download Magazine, Print Mailed Magazine |
---|