Self-adhered membranes are popular for waterproofing foundations, pedestrian tunnels and other below-grade concrete work in residential and commercial construction. Available in at least a dozen brands, all offer factory-controlled thickness and easy installation.
Self-adhered membranes—commonly referred to as “peel-and-stick” products—have a long history of being used to waterproof below-grade vertical surfaces. This type of waterproofing is widely available, and is especially popular for waterproofing foundations, pedestrian tunnels and other below-grade concrete work in residential and commercial construction. But it’s also used for specialty applications as well. “This is not only used for foundation waterproofing,” says Paul Bratton, manager of technical services at MFM. “We sell a ton of this to California for use under stucco and even for wine caves.”
Advantages
Self-adhered membranes have a long history, and a long list of unique positive traits.
Grace’s Bituthene membrane was originally launched in the 1960s, and is still used today on projects throughout the world. “The primary advantage of a self-adhered membrane is that it’s a factory-made, factory controlled product,” says Pete DiGiovanni, manager of technical services at Grace Construction Products. “That means you’re going to get the same product at the same thickness every time you open the box.”
Marc Tropper, director of product management and marketing at Henry Co., agrees that the factory-controlled millage is its best advantage, but adds that there are several others as well. “A peel-and-stick membrane, by its nature, is a finished product,” he says. “Because these membranes are fully cured, there are no VOC’s and no jobsite delays. You can backfill quickly without waiting for the waterproofing to cure, and weather-related delays are minimized as well.”
Spray-applied coatings, on the other hand, are known to be finicky. Temperature, humidity, and even the moisture content of the concrete can affect long-term adhesion, so these factors have to be monitored before, during, and after the coatings are sprayed on. Peel-and-stick membranes are far more forgiving.
Tropper also points out that sheet membranes can be applied with a minimum of equipment—there’s no need for an entire trailer of air compressors, drum heaters, spray tips, and endless spools of hoses. “It’s just removing release liner and pressing into place with a roller,” he says.
Bratton adds that peel-and-stick products are typically able to bridge cracks as wide as ¼ inch, regardless of whether the cracks occurred before or after the membrane was applied. He also states that a good waterproofing membrane must be fully adhered to the substrate. “Dimple board doesn’t offer a secure seal to the foundation wall. Air gap products are more of a drainage or water management system.”
Jason Hazen, marketing director at Soprema, says, “Peel-and-stick products typically offer warranties that are longer and more robust than other systems. They work in tough-to-spray tight areas, and across a wide range of substrates.”
They have good chemical resistance, so they’re popular at airports, brownfields, laundromats and other chemical-prone areas.
Hazen says it all comes down to consistency. “All the physical properties you are trying to achieve are based on a tested thickness,” he says. “With peel-and-stick membranes you’re guaranteed a consistent mil thickness, whereas spray applied products leave a lot to the applicator. It can be done successfully, but it’s essentially field manufactured, and you run the risk that the membrane may not perform as advertised.”
Product Makeup
Self-adhered membranes from the major manufacturers consist of the same three layers: The backing, or release sheet, which is peeled away just before application; the membrane itself; and an outer surface film which is left in place.
Most products also require a primer to encapsulate dirt and dust and increase adhesion. The primer can be rolled, painted or sprayed on, depending on the membrane and size of the job. Most are water-based and user-friendly, but a few low-temperature primers are solvent-based. These require additional caution for worker safety. Additionally, solvent-based primer cannot be used on Insulated Concrete Forms (ICFs) as the solvent will dissolve the foam.
Release sheets, which are removed in the construction process, are mostly irrelevant to how the membrane performs. But it should peel from the membrane easily and smoothly to ease installation. The latest version of Bituthene features a “rip cord” that perforates the release liner exactly where the installer intends.
The composition of the surface film, or facer, does vary between manufacturers. Hazen, at Soprema, says, “One of the major differences we see with the various peel-and-stick membranes on the market is the facer used. This facer does affect the physical properties of that sheet, and depending on the facer chosen, can improve or degrade its physical properties.”
The film protects the membrane during installation, increases its tensile strength, and gives it its crack-bridging properties.
“There’s a lot of difference in the type of film used,” agrees Bratton, at MFM. “High polymer films have the elongation, but they don’t have as much tensile strength.” High Density Polyethylene [HDPE] is stronger, but the trade off is in cost and ability to stretch.
Craig Bucher, technical manager at Grace, summarizes, “The carrier has to be tough enough to withstand the realities of installation without creating defects in the membrane.” His company uses a cross laminated carrier film that claims to be more resistant to tear and backfill forces, while remaining flexible enough to wrap around edges of footing and foundations.
As for the waterproofing layer itself, it’s a proprietary blend of waterproofing compounds that is closely guarded by each company. Basically, it’s a rubberized asphalt; most consist of either SBS (an elastomeric modified bitumen) or butyl. SBS is made from less expensive materials, and therefore is more common. Formulations with high-grade rubber and no fillers offer better adhesion.
Variations are available for specific applications. For example, W.R. Meadows offers their Mel-Rol in a low temperature (20° F to 60° F) and extra-low temperature (down to 0º F) version. Grace offers Bituthene in a low-temperature variant, as well as a 4000-series with aggressive adhesion.
Finally, the sheet thickness also varies. Most sheets are 60 mils thick, but some companies offer a 40-mil sheet for cost savings.
The weak point of all peel-and-stick membranes are the seams. “Laps are critical,” says Tropper. “If water’s going to get in, it’s going to be at the lap.”
Manufacturers take different approaches to solving this weakness. Henry’s Blueskin extends the waterproofing compound beyond the edge of the facer film. “That’s important,” Tropper says, “because it ensures you get a compound-to-compound seal. Our product includes a bulge along the edge of the roll that makes sure you’re fully sealed at the overlap.”
Making a Choice
When choosing a membrane, specifiers and applicators are less concerned about its chemical makeup, and more concerned that it will perform as intended.
Bratton says, “First and foremost, check its vapor resistance and permeance. Then see what kind of warranty is on the product, the recommended temperature range, and its puncture resistance and nail sealability.”
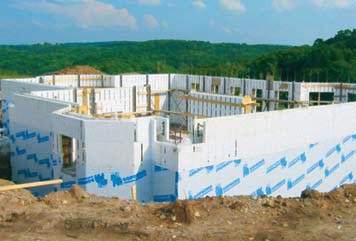
Peel-and-stick products are known for their versatility, being used for poured-in-place, precast, and other substrates (above), even finicky ones such as Insulated Concrete Forms made from EPS foam.
All these performance characteristics are readily available, and can be compared easily because ASTM has standardized testing methods nearly everyone uses. Membranes are also tested to ASTM standards on adhesion, both to the wall (peel adhesion) and to itself (lap adhesion).
But Tropper points out that the buyer wants more than just a membrane.
“In the end, you’re not choosing just a product,” he says. “You’re looking for someone who can back it up with the details, specification guides, and code approvals you need. You’re looking for a company and product with a proven track record, that provides the level of service you need.”
Bucher, at Grace, says that every job has multiple types of waterproofing —underslab, air membranes, etc.—and choosing a company that offers a complete product line-up can simplify the transitions.
Winter 2013 Back Issue
$4.95
Choosing a Peel-and-Stick
New Options for Waterproofing Decks
Keeping Water Tanks Watertight
AVAILABLE AS DIGITAL DOWNLOAD ONLY
Description
Description
Choosing a Peel-and-Stick
Self-adhered membranes are widely available, and have a long history of being used on below-grade vertical surfaces. At least a dozen brands are available, each with distinct advantages.
New Options for Waterproofing Decks
Horizontal surfaces exposed to the weather can be difficult to waterproof due to foot traffic and inadequate slope. However, products are available that seal everything from pool decks to high-rise balconies.
Keeping Water Tanks Watertight
Aging infrastructure and security mandates have created a growing niche market for concrete potable water tanks. Crystalline waterproofing is frequently specified, as it will not affect the quality of the drinking water.
Additional Info
Additional information
Magazine Format | Digital Download Magazine, Print Mailed Magazine |
---|