By Mario Baggio
A vertical, below-grade application of biochemically modified gel.
In the ongoing search for a waterproofing system that not only protects but also extends the lifespan of a concrete structure, the focus has shifted from short-term surface coatings to products that actually waterproof the concrete from the inside. These long-term integral waterproofing products fall into two fundamental categories: crystalline technology and modified silicate gel technology.
Some of the gel-based waterproofing systems only require a one-time application, meaning they can save an owner hundreds of thousands of dollars over the course of a structure’s design life—by not having to continually re-apply short-term waterproofing solutions, and all of the headaches that go with it.
In this article, we’ll explain why these integral waterproofing products cannot be damaged or prematurely deteriorate like membrane coatings, and also explore the pros and cons of their differing technologies.
Crystalline vs. Modified Silicate Gel For Existing Concrete Structures
Both of these technologies fall into the integral waterproofing category, which means they do their protective work inside the concrete matrix. In other words, they actually waterproof the concrete itself.
As a result, they are protected from the physical, environmental, and trade-related damage and deterioration that surface-applied membrane coatings frequently experience. Because they work inside the concrete, you won’t have to worry about a snow plow scraping off the new traffic coating membrane that you just applied a few months ago.
The advantages of using either of these integral waterproofing technologies instead of external membrane systems include:
- Long-term waterproofing solution
- Becomes an integral part of the substrate, not subject to deterioration
- Protects reinforcing steel from corrosion
- Low applied cost and an extremely good life cycle cost
- Environmentally friendly; allows recycling after demolition
- Absence of seams that could potentially split apart or leak
- Negative or positive side application
- Cannot be compromised by poor site conditions or worksite damage
Both technologies are well-proven, having been used on projects around the globe for 30+ years. The active ingredients in both of these waterproofing technologies use water to transport them into the cracks and pores present in the existing concrete. Both technologies leave latent chemicals behind (embedded in the concrete) that will react with any new intrusion of water. This reaction allows the concrete to self-heal when new microcracks, etc. form over time.
One notable difference between them is that the gel-based products are capable of sealing cracks that are five times as wide as the cracks the crystalline products can seal (2.0 mm wide vs. 0.4 mm wide).
Crystalline Technology
Active ingredients in crystalline waterproofing use the process of diffusion to absorb into the concrete, reacting with calcium hydroxide and other by-products that were formed during the concrete hydration process that occurred when the concrete was first formed.
This chemical reaction creates an impermeable network of crystalline structures that helps to block and plug existing microcracks and voids. Ultimately this prevents moisture, chemicals, etc. from deteriorating the concrete itself, or corroding the steel reinforcement bars.
There are three common ways to apply crystalline-based products to provide the waterproofing properties that concrete structures need to help avoid deterioration.
Admixture: Where the crystalline powder is added to the concrete as it is being mixed, prior to the pour (new construction)
Dry Shake: Involves broadcasting the product onto the surface of freshly installed concrete (new construction)
Surface-applied: Multiple slurry coats, using an air compressed sprayer or by hand using a stiff broom or masonry brush (existing structures)
These products are hydrophilic, which allows them to use any future water that penetrates into the concrete through new microcracks to react with chemicals sitting dormant in the structure. They are also VOC-free and are recyclable after demolition.
Crystalline waterproofing products can be used on concrete structures that are designed for the containment of potable water. Here is a partial list of waterproofing applications these products are commonly used on:
- Waterproofing of foundations, slabs, and walls
- Water storage tanks in municipal and industrial wastewater applications
- Potable water tanks and facilities
- Elevator shafts and parking garages
- Basements
- Secondary containment centers
- Swimming pools
Crystalline Technology—Admixture For New Construction
Unlike waterproofing systems that are applied/installed after the concrete is already in place, using admixtures to waterproof the concrete adds almost no labor cost at all. The chemicals can be mixed into the concrete at the plant or on-site, just prior to pouring.
Once the concrete hardens, and the initial waterproofing has occurred, the active ingredients in these admixtures remain dormant inside the concrete and will reactivate to block future microcracks and voids, if water and air find their way into the concrete again. These admixtures cause no visible change to the appearance of the concrete surface.
Crystalline Technology – Dry Shake For New Construction
These crystalline products typically come in a dry powder form, which can be shaken on top of the concrete surface. The active ingredients penetrate into the concrete, using water as a transport mechanism. They then react with the calcium hydroxide and other by-products that were formed during the concrete hydration process to form impermeable crystalline structures that effectively plug and block the micro-cracks, pores, and capillaries that naturally occur as the concrete is formed.
Crystalline Technology – Brush or Spray Applied For Existing Structures
This variation is applied as a cementitious slurry coat to above-grade or below-grade concrete surfaces. The product is installed either horizontally or vertically, by either manually applying with a brush/broom, or spraying it on with an industrial-grade spray rig. It generally involves a two-coat application process, and care must be taken to apply the correct thickness of product, so that it does not delaminate from the surface.
The use of this product prevents the penetration of water, or other liquids from any direction by causing a catalytic reaction that produces a non-soluble crystalline formation within the pores and capillary tracts of concrete.
Pros include:
- Becomes an integral part of the substrate; not subject to deterioration
- Can seal hairline cracks up to 0.4 mm
- Resists extreme hydrostatic pressure
- Breathable
- Resistant to aggressive chemicals
- Non-toxic
- Can be applied to the positive or the negative side of the concrete surface
Cons include:
- Applications are very slow and labor intensive
- Slurry coat is applied to the concrete surface, changing its appearance
- Brush application is slow and labor intensive
- Spray application of these products requires specialized spray equipment
- Does not react well to substantial building movement
- The two-coat application has a potential danger of the material peeling off
Modified Silicate Gel Technology
At this year’s World of Concrete convention in Las Vegas, one of the modified silicate gel products won the Most Innovative Product Award as voted by the concrete industry in the Materials for Concrete Construction category. It was a pretty amazing feat, considering this “innovative” product has already established a 40-year track record of successfully protecting concrete structures around the world. What it really says is that this amazing technology just hasn’t been fully recognized yet by many of the influential owners, specifiers, and contractors in the North American market.
Modified Silicate Gel (Flexible)
These gel-based products are spray-applied liquids that penetrate into the structural concrete matrix, using water as a transport mechanism. The products are sprayed on the surface of the structure, and travel deep into the concrete by process of diffusion. As with most waterproofing products, any needed repairs and surface preparation must be completed prior to the application, to ensure the system is installed properly.
Once applied, these products form an impermeable and flexible waterproofing layer below the surface of the concrete itself. This gel interacts with calcium hydroxide and other by-products left over from the hydration process that occurred when the concrete was initially poured to block capillaries, cracks, micro-fractures, etc. As mentioned before, at the time of application the gel will bridge cracks that are five times wider than those that crystalline technology products can: 2.0 mm vs. 0.4 mm.
In addition to fast application rates, these products are easy to apply, requiring only basic spray equipment. On fairly open project areas, contractors can easily apply 15,000 to 20,000 square feet of product per hour. They can cover substantially more area in one hour than a crystalline products crew can cover in a full day.
Clear and colorless, these products do not change the exterior appearance of the concrete surface. In addition to filling and blocking the microcracks and voids inherent in the existing concrete, it also has the ability to “self-heal,” as future stable cracks occur in the concrete structure. This in effect, creates a permanent waterproofing solution.
The result is an integral waterproofing system that cannot be damaged or deteriorate like surface coatings. The layer of waterproofing gel effectively blocks water and chemical penetration, and protects the steel reinforcement bars for the life of the structure.
These gel-based products are very resistant to hydrostatic pressures and can be used where there is extreme exposure, such as tunnels, dams, pools, subways, etc. They are very effective at protecting the concrete from chloride ion penetration (salt water and ice melt) and help prevent scaling, ACR (alkali-carbonate reaction), and ASR (alkali-silica reaction) from occurring.
The gel products are applied using a simple spray system, and completely absorb into the concrete, leaving the surface of the concrete unchanged. This can be a critical factor in projects where maintaining “the look” of a structure is important (historical structures, restorations, highly visible structures, etc). The surface of the concrete can still be painted or coated with an aesthetic coating after the waterproofing has been completed. These gel products also do not affect the “slip resistance” of the concrete surface.
The gel-based products also act as a densifier for the concrete surface. For example, a concrete pour that was initially tested at 3,500 psi would test at roughly 5,000 psi after the gel had fully formed within the concrete matrix. Also, the modified silicate gel-based products perform more effectively than crystalline products in structures that experience building movement or high-thermal stress, due to their inherent flexible characteristics.
Pros include:
- Improves the durability and sustainability of concrete structures
- One-time application saves owner money over the life of the structure
- Fast application rate resulting in far less down time, saving owners money
- Seals “stable” cracks up to 2.0 mm wide when applied and also seals future cracks up to 0.4 mm wide
- Vapor permeable; allows concrete to breathe (outgassing) and does not trap moisture within the concrete
- Highly resistant to chemicals and chloride ions
- Acts as a densifier; increases hardness of the concrete surface
- Excellent hydrostatic pressure ratings (1,300 feet / 400 meters)
- Can’t be damaged, deteriorate, or delaminate; long-term solution
- Gel formulation handles thermal stress very well
- Non-toxic and VOC-free; concrete stays recyclable
- No surface priming or leveling needed
- Lower applied cost than most other methods
- No mixing of products on-site; eliminates error factor
- Can be applied on positive or the negative side, although it’s highly recommended to be applied to the positive side.
Cons include:
- Concrete surface must be dry to the touch in order to begin application of the gel-based waterproofing products
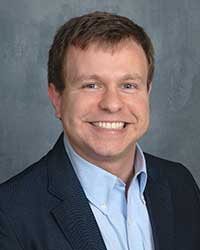
Mario Baggio
Mario Baggio is the CEO of Alchemco in the United States. Over the last 30 years Alchemco has used many different products and services to solve the problems associated with moisture protection. With the development of new technology and manufacturing capabilities, Alchemco evolved into becoming a world leader in the moisture and surface protection market. Before joining Alchemco, Mario Baggio served more than 10 years in the concrete protection and waterproofing industry in multiple countries.
Fall 2020 Back Issue
$4.95
Cast-In-Place Concrete vs. Shotcrete: The CIP Advantage
Gel Waterproofing
Effective Waterproofing for ICFs
A Green Roof for Liberty Island
AVAILABLE AS DIGITAL DOWNLOAD ONLY
Description
Description
Cast-In-Place Concrete vs. Shotcrete: The CIP Advantage
By Stacy Byrd
Below-grade concrete can be cast-in place using forms or high-pressure shotcrete. A waterproofing expert evaluates the advantages of each method.
Gel Waterproofing
By Mario Baggio
Crystalline waterproofing and modified silicate gel-based approaches may look similar, but they work in different ways, and each has its own advantages.
Effective Waterproofing for ICFs
By Brian Corder
Insulated concrete forms (ICFs) become increasingly popular and are incompatible with solvent-based waterproofing. Manufacturers recommend water-based or self-adhered systems.
A Green Roof for Liberty Island
By Linda Velazquez
In New York Harbor, a new Statue of Liberty Museum in the shadow of the iconic statue boasts a state-of-the art sloping green roof.
Additional Info
Additional information
Magazine Format | Digital Download Magazine, Print Mailed Magazine |
---|
Interested in knowing more have been in the Waterproofing industry commercially and residential for 15 years.
Interested in possibly becoming a distributor and installer.
Lloyd Warr
905-921-2211