By Gregory Fahrenbruch
Testing showed that this was brown asbestos-containing glue on the wall.
Asbestos is a scary word for a homeowner to hear because of its reputation for causing harmful lung conditions. Asbestos exists in homes that waterproofers work on, though, so the waterproofing industry cannot overlook this substance. How you choose to address it, or not, reflects and can impact your company’s reputation. Asbestos has the potential to financially impact a waterproofing company in many ways, such as worker health, customer health, it may hit the company’s bottom line through civil suits, regulatory fines, and insurance rates.
Often, waterproofers are looking at older homes that were built before 1980. It’s common to find asbestos in homes built before 1980 because asbestos products were used in more than 3,000 different building materials. You will find them in cement products, troweled coatings, glues (mastics), spray-on coatings, flooring, pipe insulations, plasters, ceiling tiles, siding, tape joint compounds, and even strange-looking panels that look like concrete but when they are painted they look like paneling. These are actually made of Transite, a brand of asbestos-cement products that are more common in commercial buildings.
What Is Asbestos?
There are six types of asbestos minerals which occurred naturally during the formation of the earth. Actinolite, amosite, anthophyllite, crocidolite, and tremolite establish the amphibole family, and chrysotile makes up the serpentine family of asbestos. Asbestos mining took place all over the world. The last mine in the United States closed in 2002 long after attempts to ban asbestos products. You most likely won’t find pure asbestos because it was used as an ingredient in building materials.
Asbestos offers many qualities such as fire resistance, chemical resistance, strength, and durability. Asbestos is typically landfilled for disposal because it cannot easily be destroyed except through ultra-high-temperature incineration. Asbestos disposal is closely regulated and many countries have banned its use. Asbestos is regulated by OSHA and the EPA, and other state agencies.
Working With Asbestos
There are two types of asbestos work which are recognized as class 1 and 2, depending on what category of asbestos products the work is done on. Category refers to the state of the asbestos product. Category 1 products are materials that can easily become airborne. Examples of this are pipe wrap or any paper products. Also included in this is tape joint compounds. Category 2 products are siding, and floor tiles. If a category 2 product is broken into many pieces, it then becomes a category 1 product.
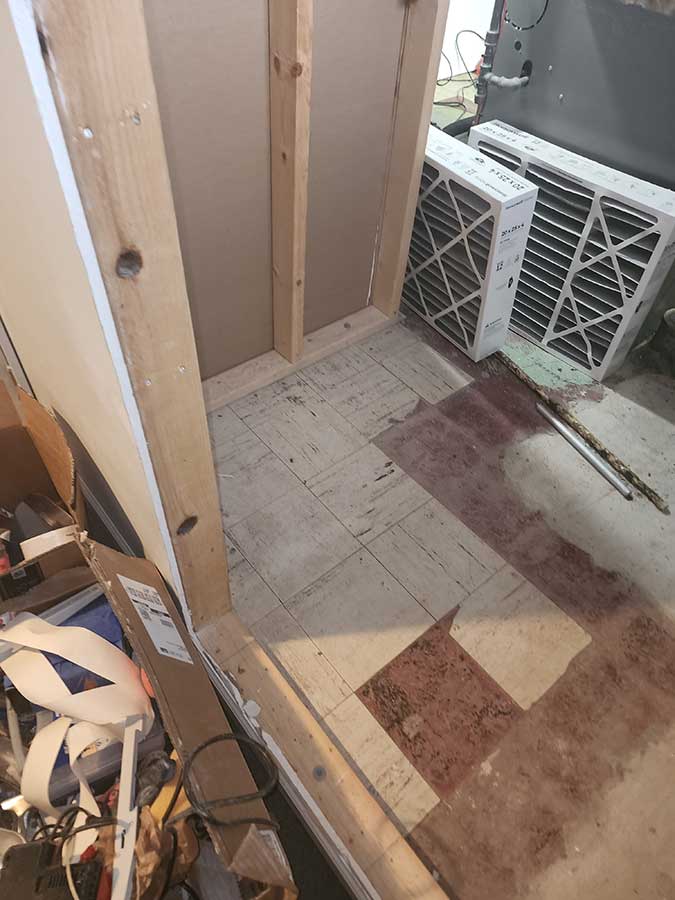
A 9×9 tile is positive for asbestos 98% of the time and mastic is positive about 50% of the time. You cannot tell if mastic or brown paneling glue is positive or negative by looking at it. Photo courtesy of Greg Fahrenbruch
Class 1 work is with paper products. These products are typically found on boiler pipes, insulating paper around ducts, heat shields above furnaces, white tape on duct joints and backers between layers of flooring. Tape joint compounds, popcorn ceilings, plaster, and troweled coatings, and black felt paper are also category 1 materials. These materials meet the definition of “friable materials.”
Class 2 materials waterproofers encounter are floor tiles in any size, siding, and roofing materials. Often, people think asbestos floor tiles are not regulated, but that is not true. Asbestos floor tile removal is regulated. Take heed, as most floor tiles have greater than 1% asbestos. Products with greater than 1% asbestos become by definition an asbestos-containing material. Products with less than 1% asbestos do not meet the definition of an asbestos-containing material, but by regulation, precautions are legally required.
Old siding falls off exterior walls during the building of new additions into the new crawl space, with the new addition built over top the old materials and when waterproofing companies enter into the crawlspace they hit this legal roadblock. Class 2 siding is often found in crawl spaces. It is laying in the dirt from previous remodeling activities. It must be removed or some sort of safeguard must be taken to eliminate exposures to untrained and non-medically monitored employees. This siding in crawl spaces is common.
Class 1 Work
Asbestos-trained workers perform class 1, 2, 3 and 4 work. Class 1 work (working on category 1 materials) means working with materials that can be crumbled or pulverized during removal (Friable). From a regulatory perspective, there’s a fine line when it comes to category 2 materials because during an inspection the material may not meet the definition of friable, but it can be crumbled between your fingers during removal. Certain materials may meet the definition of friable even though they cannot be crumbled between the fingers. This class of work constitutes class 1 abatement work. This type of work will typically require a notification to the state or federal jurisdiction where the work is done, which is cross-referenced during disposal.
Class 2 Work
Class 2 work (working on category 2 materials) is the removal of flooring materials or siding and roofing materials. This class of work constitutes an abatement. During the performance of class 2 work, it could get redefined into class 1 work.
Both class 1 and 2 work must be supervised by a competent accredited and carded supervisor. Often, other certified supervisors will be on the site in case the lead supervisor leaves the site. If only workers are left on the site, the entire operation must stop.
Class 3 & 4 Work
Class 3 work is repairs and maintenance. Class 4 work is generally based on working with asbestos-containing materials but not disturbing the asbestos. Such work may include stripping and waxing floors.
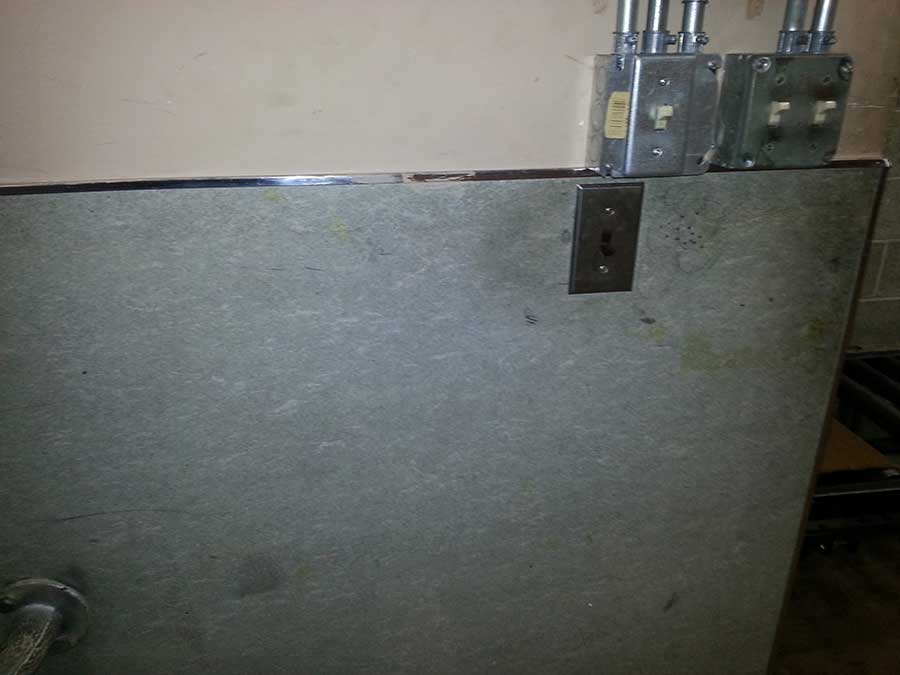
This photo shows Transite, a brand of asbestos-cement products that are more common in commercial buildings. The panels can look like concrete or paneling if they are painted. Photo courtesy of Dan Ventura, Hawk Environmental
Asbestos Worker Qualifications
The supervisor is a trained person who has gone through 40 hours of training to work as a competent person overseeing work activities. A worker works under a supervisor on class 1 and 2 jobs. A management planner oversees asbestos management plans in schools and commercial buildings. Always ask for the management planner before starting work in such buildings. A project designer designs asbestos abatement projects in schools or when work practices cannot meet the regulatory requirements. Air testing professionals are either qualified by the state you work in or they have taken a 582/7400 air testing/microscopy course, but in both cases they need to provide some sort of documentation that shows they meet the qualifications for air sampling.
How Waterproofing Companies Handle Asbestos
Without hesitation, conduct an annual two-hour asbestos awareness class that follows the regulations. Have each participant sign in for documentation, and have them complete a quiz to demonstrate competence. Next, make a written policy and have everyone sign off on the policy. The policy should state the company’s position on asbestos and requirements for employee classifications. Generally, this is a “see possible asbestos containing material (PACM) and stop” policy. At this point, management needs to enforce their written policy.
Waterproofing companies need to make decisions on how to handle asbestos. The first decision is whether they should become a licensed abatement contractor or not. The next decision would be whether or not they are subcontracting the work. In most cases I would recommend not to do in-house abatement or subcontract abatements. Both cases make your company have general supervisory responsibilities which can lead to liabilities. A policy to have a homeowner remove asbestos themselves does not lead to professional results and can delay your project because of the lack of air samples and possible residuals remaining of all PACM materials.
When I go in for an air clearance for a homeowner’s work, I first look for any asbestos residual of any sort that may cause an exposure. They are held to the same level as an abatement contractor. Once it passes the visual inspection for a complete job, then I test the air for fibers.
The Bottom Line
I recommend that waterproofing companies stay away from asbestos. The best way to keep your jobs on track and get the asbestos out of the way would be to develop a solid relationship with an abatement company that can handle your roadblock. Have them provide you a document that states the air quality passed after they abate, then proceed with your work. The management of this process falls on the waterproofing company.
Greg Fahrenbruch
Greg Fahrenbruch founded Restoration Environmental Safety Technologies, or REST, in Ortonville, Michigan, in 2010. He is an industrial hygienist with a degree from Ferris State University with expertise in asbestos removal. He holds state accreditations as an asbestos inspector, asbestos contractor supervisor, management planner, and asbestos-licensed contractor. He also has a background in insurance restoration. Contact him at greg@restenvironmental.com.
Summer 2023 Back Issue
$4.95 – $5.95
Asbestos in the Waterproofing Industry
Choosing and Installing Sump Pumps
Cool Roofing
Case Study: Interior Basement Waterproofing
Description
Description
Asbestos in the Waterproofing Industry
By Gregory Fahrenbruch
Asbestos is a scary word for a homeowner to hear because of its reputation for causing harmful lung conditions. Asbestos does exist in homes that waterproofers work on, though, so the waterproofing industry cannot overlook this substance.
Choosing and Installing Sump Pumps
By Vanessa Salvia
Sump pumps are an essential tool for waterproofing professionals looking to keep a basement or crawlspace dry. These pumps help remove excess water from a space, preventing damage to the foundation and any stored items.
But with so many options available, how do you choose the right sump pump for your needs?
Cool Roofing
By Vanessa Salvia
Cool roofs keep interior spaces cooler, which lowers energy costs, keeps buildings and homes more comfortable, and can reduce carbon emissions.
Case Study: Interior Basement Waterproofing
By ’58 Foundations & Waterproofing
In a Pennsylvania home, a homeowner with a basement was plagued by problems with invasive water. The sump pump was failing whenever the water table got high, and the basement was getting wet as a result.
Additional Info
Additional information
Weight | N/A |
---|---|
Magazine Format | Digital Download Magazine, Print Mailed Magazine |