By Vanessa Salvia
The Cool Roof Rating Council explains that a cool roof is one that strongly reflects sunlight (solar energy) and also cools itself by efficiently emitting any heat that was absorbed.
The U.S. Department of Energy’s document, “Consumer Guide to Cool Roofs,” explains that in the mid-1980s, researchers in the U.S. were measuring the energy savings offered by test rods coated with “solar radiation control coatings.” Today, we know that cool roofs keep interior spaces cooler, which lowers energy costs, keeps buildings and homes more comfortable, and can reduce carbon emissions because if the interior is cooler, people use less electricity for air conditioning. Cool roofs can be either coatings or membranes They are typically white, but other light colors have similar benefits.
How Cool Roofs Work
While there is more awareness now of the concept of cool roofs, they aren’t new. Light-colored and reflective roofs have been in use since the 1960s in Europe, and the 1970s in North America. Cool roofs can be composed of coatings or membranes, and some materials, like light-colored wood shingles or clay tiles, can have cooling elements. Even green, or vegetative roofs can be considered cool roofs because they are cooled by the evaporation of water from plants, and the soil layer provides another layer of insulation.
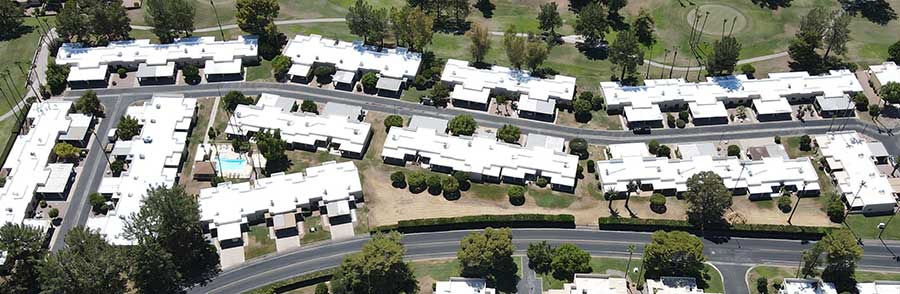
Finished Karnak 670HS Silicone coating over Single Ply membrane in West Palm Beach, Florida. Photos courtesy of Karnak Corp.
An organization called the Cool Roof Rating Council explains that a cool roof is one that strongly reflects sunlight (solar energy) and also cools itself by efficiently emitting any heat that was absorbed. This definition contains the two most important terms related to cool roofs: reflectivity and emissivity. Cool roof materials reflect the solar radiation back into the atmosphere, meaning they are reflective, while cool roof materials also radiate any heat that they absorb, meaning they have high emissivity. These two qualities combined mean that the roof stays cooler, which reduces the amount of heat that transfers to the interior of the building, and the roof effectively radiates away any heat that it did absorb rather than holding on to it. Roofs need to be able to release any heat they absorb back out into the atmosphere. Roof materials with low emissivity mean the materials directly below it retain heat longer, which can eventually reach the interior of the building.
Chris Salazar, chief operating officer for Karnak Roof Coatings in New Jersey, explains that for low sloped roofs or flat roofs, the minimum reflectivity has to be 75%. ENERGY STAR’s emissivity requirement for both low-slope and steep-slope roofing applications, which is greater than or equal to 0.75. While emissivity didn’t have a specific requirement, Salazar says they wanted it to be better than 60%. The Energy Star roof products program launched in 1999 but was sunsetted in 2021 with the rationale that efficient commercial roofing is now driven by codes and voluntary building standards.
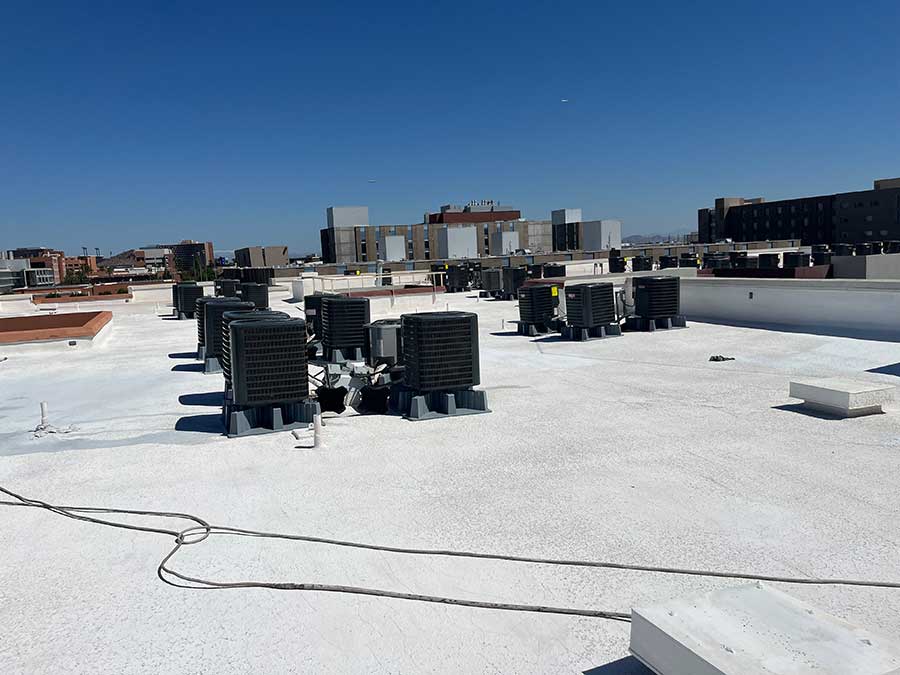
Karnak 502 SEBS Thermoplastic Rubber coating over granulated asphalt, in Tempe, Arizona. Photo courtesy of Karnak Corp.
“A 75% reflectivity rate means that if you have 100% UV light hitting a roof that has a reflectivity of 75%, that roof is rejecting 75% of the heat that was directed at that roof,” Salazar says. “Emissivity is a little different. A roof absorbs heat as the sun shines on it. When you remove the sunlight, a roof that is highly emissive will get rid of that heat very quickly. A roof that has low emissivity will retain that heat for a very long time.”
Salazar explains that black membranes, for instance, start off with very low reflectivity and high emissivity. As they turn gray, both of those parameters invert. Meaning that in black roofs, as reflectivity goes up, emissivity goes down. To Salazar, reflectivity is the most important parameter. “Wind cools roofs down pretty quickly,” he says.
Reflectivity fades over time with some products more than others. Salazar explains that a sloped roof that has dirt accumulated will lose reflectivity. But a low-sloped roof where the dirt either doesn’t accumulate or is washed off regularly will retain its reflectivity. A flat roof that is not maintained will also lose its reflectivity. “Proactive washing is a good idea for any roof,” he says.
Cool Roof Materials
There are many high-performing reflective materials such as silicone and acrylics, and/or SEBS. Reflective materials can be coatings or membranes. Coatings can also be utilized to function as a membrane when used with proper dry film thickness and reinforced. Polyglass manufactures membranes and coatings that are reflective, in comparison with Karnak, which manufactures liquid coatings with reflective properties. Both work in similar ways. Karnak’s 501 Elasto-Brite is an acrylic emulsion coating that has a .86 initial solar reflectance and a .91 thermal emittance (emissivity). Polyglass’s PolyBrite 90, for instance, is a high solid silicone formula that scores 0.87 on reflectivity and a thermal emittance score of 0.89. Styrene-ethylene-butylene-styrene, or SEBS, coatings provide high reflectivity and provide a higher degree of UV protection. According to Architectural Roof Coatings, SEBS reflective roof coatings have a reflectivity of more than 90% at the time of application. The CRRC ratings program also provides scores for the predicted and actual reflectivity and emissivity of materials after it has been in place for different amounts of time.
Polyglass’ Polyfresko G is a polymer-modified membrane that is available in either atactic-polypropylene (APP) or styrene-butadiene-styrene (SBS) versions. “They both have the same reflective finish that’s applied in the factory,” says Steven Wadding, Polyglass’ corporate projects manager. “It’s called Cure Technology, and it is a very thin, reflective finish that’s applied to the granular surface.”
The main function is reflectivity, but Wadding also states the Cure Technology resists staining, is scuff-resistant, is UV-stable, and provides exceptional granule retention — this means that the membrane holds on to the granules that are applied to them, which means that the material resists weathering more effectively. The granularity is a preference for contractors when it comes to capsheets and Cure Technology ensures reflectivity even to a variegated surface, Wadding says.
Membranes vs. Coatings
Both membranes and coatings have advantages. Liquid roof coatings and membranes form a protective layer against environmental conditions. Coatings are not just paint — they are thick enough to create a film that effectively seals gaps and cracks when applied correctly. Both coatings and membranes can form waterproofing and weatherproof barriers. But one main difference is that membranes are a long-term product whereas coatings are generally reapplied. Liquids can fill small gaps and cracks in a roof, but membranes are a best replacement choice for more damaged roofs.
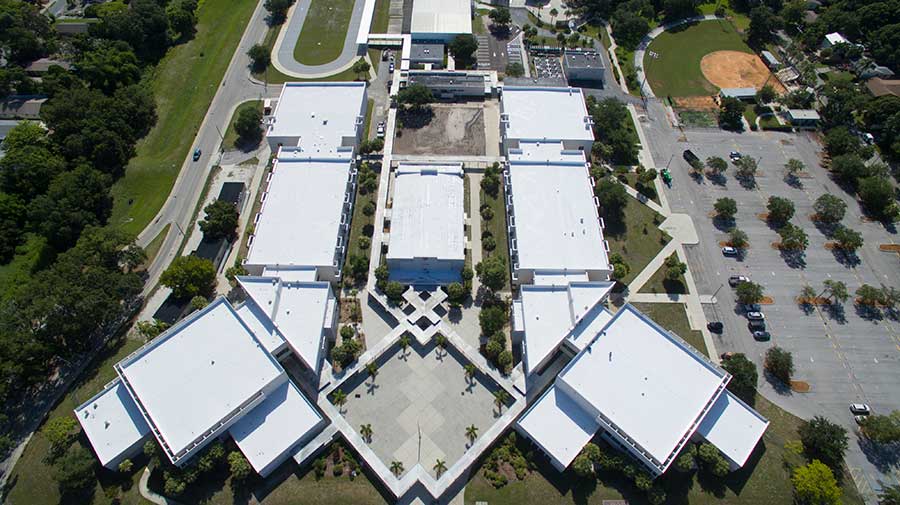
Springer-Peterson Roofing and Sheet Metal based in Lakeland, Florida, recovered the buildings of Sarasota High School in Sarasota using Polyglass’ Polyfresko G cap sheet. Photo courtesy of Polyglass
Salazar explains that the coating acts as a “sacrificial layer,” to protect the roof itself. “They extend the life of that roof by cooling it down,” he says. “For instance, when the sun hits an uncoated, asphalt roof, you’re basically baking the oils out of it. But when you apply a cool coating to it, you’re reducing that surface temperature by up to 30 degrees or even up to 50 degrees, so that extends the life pretty significantly.”
Jacob Schwarz, Karnak’s marketing director, notes that coatings are not typically applied to new roofs, but they are a good way to revive a roof that has lost some of its performance over time. “If you install a membrane, you can put it on a new roof and that will establish that reflectivity from day one of that building,” Schwarz says. “But if the roof is deteriorating slightly or even a fair amount, a coating can make it reflective and turn it into a cool roof, even if it is 10, 15, or 20 years old.”
It’s worth noting, he says, that any repairs the roof needed would need to be done before the coating was applied. “Sometimes, people will put coatings on new roofs,” Schwarz says, “but the majority of the time it is done to bring that roof back to life and get more years of life out of it.”
A membrane serves as a long-term barrier which has puncture resistance and protects the material underneath it. Wadding notes that applying coatings on a regular schedule can be beneficial for facilities managers because they know when the coating will need to be reapplied and they can budget for it. Wadding also notes that membranes are more costly, but return that investment in longevity and durability.
Benefits of Cool Roofs
Another benefit for commercial roof applications is that kilowatt-hour charges for energy are always based on the maximum peak usage which is typically highest in the summer. “If you have a black roof on a commercial facility and you coat it white, several things happen,” Salazar says. “The peak usage goes down and therefore that facility’s energy costs go down for the entire year. That’s a big deal for commercial buildings that use a lot of energy. Also, most of these buildings have very large HVAC units on a black roof that probably run the entire day during the summer. If you coat the roof white, those units can shut down, cool down, and then start again. And that usually extends the life of those HVAC units.”
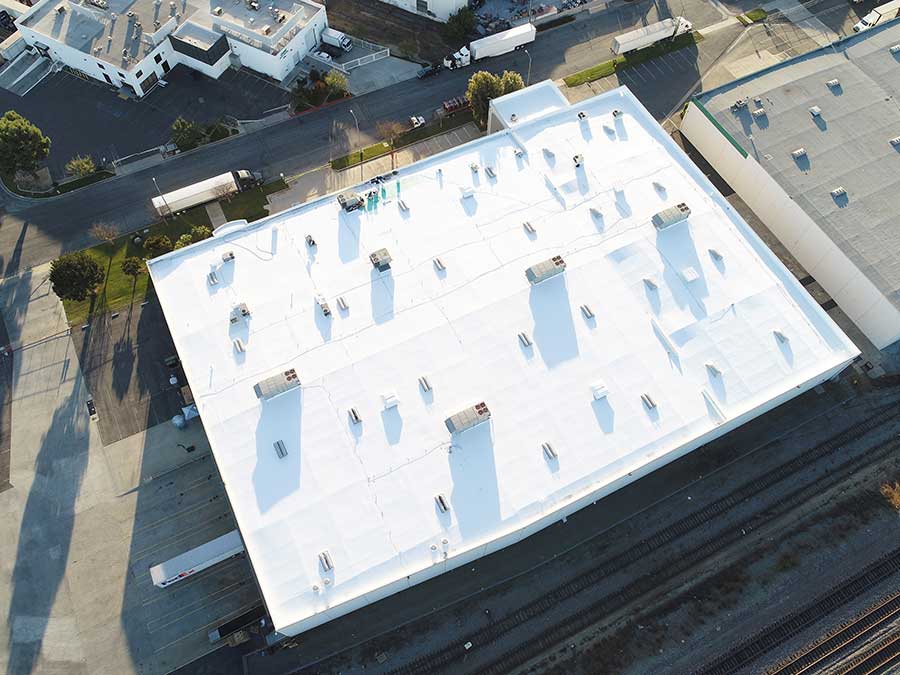
A medical supply firm called ICU Medical contracted C.I. Services for an 80,000-square-foot roof restoration project for one of their warehousing and distribution centers in Santa Fe Springs, California. The team applied Polybrite 98 Primer then Polybrite 90.1 Silicone Coating. Photo courtesy of Polyglass
A roof can always be recoated, provided it is cleaned and prepped properly. If you recoat a roof, Schwarz says you can perform an adhesion test, where you test whatever products you plan on using on a small section. “You embed a piece of cotton fabric into the spot you’re testing, let it dry for a few days, and then you pull it up using a fish scale to determine the force,” Schwarz explains. “Depending on the force that it takes to pull the strip, you can determine whether or not that product is appropriate to use. Typically, two or more pounds of force indicates good adhesion.” (Schwarz says the Karnak website has several blogs written about cool roof coatings and their application.)
When Cool Roofs Are Not Cool
There are some situations when a cool roof does not make sense. Salazar says one thing to look at is whether the cool roof will be applied over an air-conditioned building. “Then I would recommend a reflective coating on those roofs,” Salazar says. “In many cases in something like a commercial warehouse, you have a building that’s not air conditioned but the office is air conditioned inside it. For those, a cool roof wouldn’t reduce the energy used very much, but what a cool roof does do in those situations is it improves the working environment inside that building because it lowers ambient temperatures inside.”
Another situation where a coating would not make sense is if a home has shingles on the roof. The reason you can’t coat shingles is because the shingles have multiple areas of overlap where the water runs down those overlaps. “When you seal the bottom of those shingles, if you miss any of those entry points where water can get in, then you’re actually trapping water in that route,” Salazar says.
In colder regions, there is an energy savings during the summer for reflective roofs, but in winter there is a heating penalty. What this means is that in summer, when it is hot, the cool roof helps keep the building cooler. But in winter when there is less warmth, the same characteristics could cause the building to not absorb and retain heat that you would want in the wintertime. “In that case, it might be preferential to keep a darker coating or a medium coating,” Salazar says. “My opinion is that for colder regions, highly reflective aluminum coatings are better.”
Wadding shared that cool roofs can be beneficial in many climate zones, but users must consider that in cooler climate zones such as climate zones 5 to 7, cool roof requirements help in the summer but not in the winter because you don’t get the same drying effects. “In those climates, some people have mold problems because they add a cool roof but don’t do anything to the remainder of the house to make it suitable for those changes.” He goes on to explain that without the exchange of air, the temperature differentiation isn’t what the building was originally designed for, and the building doesn’t heat up and dry out like it should.
Think It Through
If you are going to consider retrofitting a roof to be a cool roof or installing a cool roof, be sure to think through the temperatures and climate you are dealing with and how that new cool roof will impact the structure itself. “Will it affect something like the mechanical system or something else?” asks Wadding. “Think it through so you get the ultimate benefit from it. Don’t look at a cool roof as one size fits all. Look at it individually, for your circumstances and the goals that you want to accomplish.”
Cool Roofs and Resilience
Whether you say resilience or sustainability, cool roofs will play an ever more important role in the coming years, particularly as climate change becomes more apparent. Summers are getting hotter, winters are getting colder, and building needs will have to keep up. “We think coatings are going to play an intricate part of resilience,” says Salazar. “And the reason being that when you put on a roof, most codes only allow you to put on two roofs. After that, you have to do one of two things: You can restore the roof and maintain it or you have to tear it off and replace it. So with a coating, you can make a good argument that you can extend the life of that roof by another 20 and maybe 30 years with a second set of coatings and you’re not generating waste. You don’t have to increase the amount of insulation that goes on a roof. You don’t have to lift the air conditioners to put on a thicker insulation to be cozy. So there are a lot of factors that I think are going to make coatings a main focus of resiliency in roofing.”
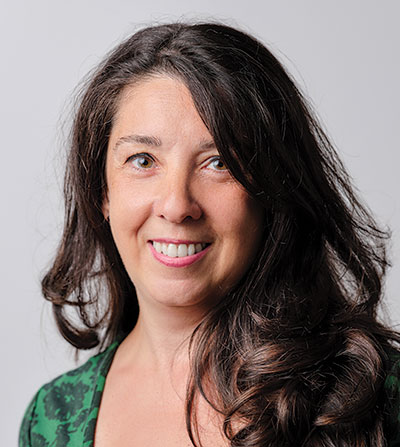
Vanessa Salvia
Editorial Director
Vanessa Salvia Writer, Editor, Content Creator Writer - Editor - Content Creator Over a nearly 20-year career as a journalist, I have learned the importance of telling stories and delivering a clear message. As a content creator, I help businesses build their brands and communicate their messages in the most effective ways.
Summer 2023 Back Issue
$4.95 – $5.95
Asbestos in the Waterproofing Industry
Choosing and Installing Sump Pumps
Cool Roofing
Case Study: Interior Basement Waterproofing
Description
Description
Asbestos in the Waterproofing Industry
By Gregory Fahrenbruch
Asbestos is a scary word for a homeowner to hear because of its reputation for causing harmful lung conditions. Asbestos does exist in homes that waterproofers work on, though, so the waterproofing industry cannot overlook this substance.
Choosing and Installing Sump Pumps
By Vanessa Salvia
Sump pumps are an essential tool for waterproofing professionals looking to keep a basement or crawlspace dry. These pumps help remove excess water from a space, preventing damage to the foundation and any stored items.
But with so many options available, how do you choose the right sump pump for your needs?
Cool Roofing
By Vanessa Salvia
Cool roofs keep interior spaces cooler, which lowers energy costs, keeps buildings and homes more comfortable, and can reduce carbon emissions.
Case Study: Interior Basement Waterproofing
By ’58 Foundations & Waterproofing
In a Pennsylvania home, a homeowner with a basement was plagued by problems with invasive water. The sump pump was failing whenever the water table got high, and the basement was getting wet as a result.
Additional Info
Additional information
Weight | N/A |
---|---|
Magazine Format | Digital Download Magazine, Print Mailed Magazine |