By Matthew Sands
Photos courtesy of Renolit
Aquatic facilities are continuously looking for new waterproofing options for the surrounding deck area of the pool as well as wet areas such as locker rooms at commercial athletic facilities, YMCAs, private clubs, and the like. Decks around swimming pools and splash pads are often plagued with cracks, chips, broken tile, peeling paint, flaking, and delamination. This is also common in changing and locker rooms.
One of the most cost-effective solutions to renovate and waterproof decks in aquatic facilities (including interior locker room flooring) is to cover the existing deck or flooring with an 80 mil thick, reinforced PVC deck membrane that will provide a seamless, attractive, waterproof, and slip-resistant deck that is both safer and provides superior comfort for the bare feet of patrons.
This reinforced PVC membrane solution was created to renovate and waterproof decks at any type of aquatic facility—from water parks and wave pools to athletic facilities or community pools. Reinforced PVC deck membrane provides long-term ease of maintenance and a terrific solution for common deck problems.
PVC pool deck membranes provide a long-lasting waterproof solution that does not require recoating and comes with far less maintenance than traditional decking solutions. Unlike concrete decks, PVC membranes for pool and spa decks can be installed in almost any temperature. In fact, the PVC membrane eliminates the common cracking problems in concrete that occur with freeze-thaw weather. PVC membrane decking can be installed on concrete surfaces, tiled floors, or even over wood decks.
Structural Benefits
Having a fully waterproofed deck has many advantages, including long-term structural advantages. For example, if the pool deck is not properly waterproofed, the water left by swimmers exiting the pool, splash-out, or deck cleaning can penetrate the floor and infiltrate the substrate, causing future maintenance issues to the structure. Over time, water on the deck that does not drain properly can infiltrate the structure and deteriorate the pool, not to mention being visually detracting and unsafe. Using reinforced PVC to waterproof the entire deck avoids all this because it guarantees complete waterproofing of the deck. Further, the slip-resistant PVC ensures all safety requirements in all areas of the wet-zone are met including locker rooms and other indoor spaces.
The installation of reinforced PVC can even be done over cold joints in concrete and is not susceptible to freeze-thaw cycles. The PVC deck membrane also stabilizes the pool deck by preventing future water infiltrations. The reinforced PVC can also be easily combined with a gutter system to create a seamless watertight solution for the entire pool area.
Additionally, once the reinforced PVC is installed, the surface underneath the pool deck can continue to shift and crack but it will not affect the reinforced PVC pool interior itself. Further, in many cases, this reinforced PVC deck membrane often comes with a longer warranty than other deck options. In many cases, not only does the reinforced PVC interior pool finish help to solve a deck problem, but it can also make pool maintenance easier than a traditional concrete deck surface.
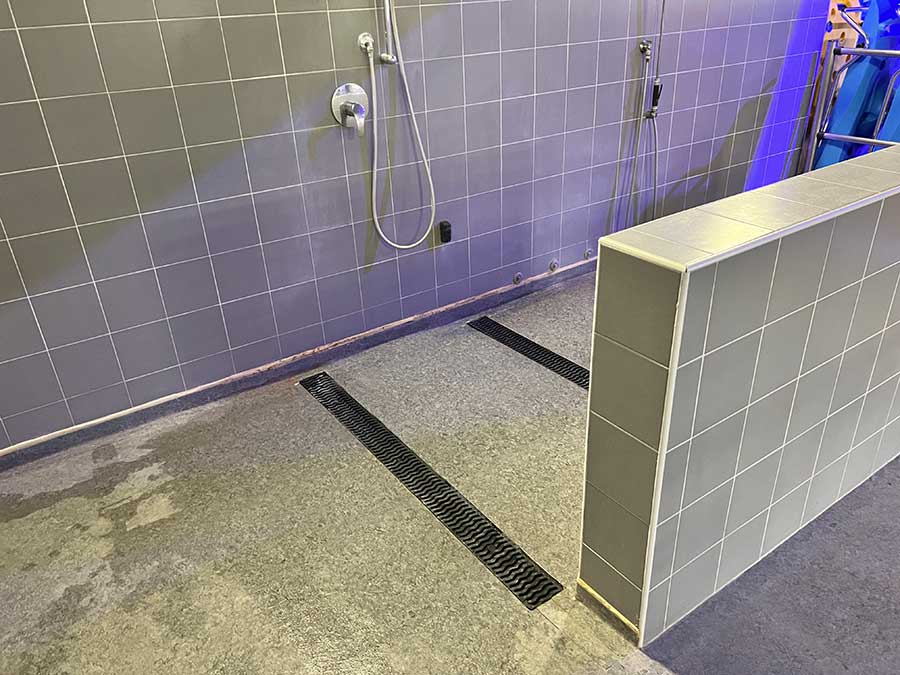
PVC membrane provides a durable, seamless, slip-resistant floor that is safer and more comfortable for bare feet.
Maintenance Benefits
PVC deck membrane material is very resistant to chlorine and stains, thanks to its highly protective acrylic lacquer coating. The membrane’s smooth surface prevents the accumulation of dirt and grime — reducing the need for frequent cleaning and maintenance. Unlike other decking products, there is no need to use acid or other dangerous and abrasive cleaners to keep the surface in perfect condition all year long. This can be especially appealing for commercial aquatic facilities. The PVC deck membrane offers a commercial-grade, long-term solution because it is not only thick and non-porous but also coated with a protective lacquer that resists chemical abuse, water absorption, and UV deterioration.
Safety Benefits
Reinforced PVC also offers additional safety benefits for decks experiencing cracking, flaking, delamination, and peeling which can particularly be appealing for commercial aquatic facilities. In some cases, the decks around pools can be the most dangerous part of any pool. Older, cracked, or peeling decks can lead to injuries due to slippery surfaces. Some cracks can even cut bathers’ feet. Reinforced PVC encapsulates the deck, making the area slip-resistant and waterproof. This option is ideal for decks experiencing cracking, flaking, delamination, and peeling.
Renovation Benefits
The use of concrete, stamped concrete, tiles, and flagstone have traditionally been the primary choices for surrounding pool and spa decks. However, once these surfaces become worn and cracked, aquatic facility managers seek ways to renovate these decks.
Unlike concrete decks, PVC membranes for pool and spa decks can be installed in almost any temperature. In fact, the PVC membrane eliminates the common cracking problems in concrete that occur with freeze-thaw weather.
Having a fully waterproofed deck has many advantages, including long-term structural advantages. For example, if the pool deck is not properly waterproofed, the water left by swimmers exiting the pool or splash-out or deck cleaning can penetrate the floor and infiltrate the substrate causing future maintenance issues to the structure. This risk is frequently underestimated by construction companies. Water on the deck that does not drain properly, over time can infiltrate the structure and deteriorate the pool, not to mention being visually detracting and unsafe.
Using reinforced PVC to waterproof the entire deck avoids all this because it guarantees complete waterproofing of the deck. When combined with a compatible gutter system it ensures seamless waterproofing from the pool to the deck. Further, the slip-resistant PVC ensures all safety requirements in all areas of the wet-zone are met.
PVC Deck Membrane Installation
If installed over existing concrete, the installation requires the following steps:
- Filling any cracks or holes in the surface
- Leveling and cleaning the surface
- Applying glue
- Applying an antimicrobial felt/geotextile layer
- Laying down and welding together the reinforced PVC
Commercial aquatic facilities benefit from the shorter installation time required; the only downtime is if the surface requires leveling, in which case, a leveling material is poured prior to the installation of the reinforced PVC. For instance, a 20×20-foot area can be lined and welded in a few hours when using a robotic welder.
Reinforced PVC for pool decks is also rolled out and heat-welded together on-site to ensure an accurate, smooth fit to the shape of the deck that is completely jointless. The process does require some skill, but many suppliers provide on-site training and initial installation assistance to pool professionals who are just getting started. Once trained, reinforced PVC can be installed year-round on indoor pools and even in cooler climates, such as late fall and early spring.
Deck preparation
It is essential to carry out a thorough cleaning of the entire surface, as well as of the pool area. It is important to remember the reinforced PVC membrane will replicate the shape of any imperfection or impurity. For this reason, and given the decking area is usually large, it is recommended to use an industrial vacuum cleaner, to remove both solid and liquid waste. Several extensive cleans will be carried out after each stage prior to the membrane application.
Geotextile application
The geotextile layer has the dual function of filling the step generated by the butt-welding strip, and of attenuating eventual irregularities in the underlying floor. If the existing floor should have strong irregularities, it is recommended to provide for prior repairs.
Before applying the floor adhesive, the surface must be thoroughly cleaned again, removing any debris from the leveler and other impurities that can cause both esthetic and adhesion problems. Once the pavement is leveled and free of impurities, pavement adhesive is applied.
The antimicrobial felt/geotextile layer is glued to the floor, making sure it coincides perfectly with the butt-welding strip, taking good care of not overlapping it, or leaving any space between.
Cutting and welding membrane into place
The reinforced PVC pool interior is rolled out in 5.4-foot (1.65-meter) wide lengths, cut to the dimensions of the pool deck, and then heat-welded together on-site to ensure a smooth fit. Since decks require a completely smooth finish, installers use what is commonly known as a “butt-welding” technique. To do this, installers butt the reinforced PVC edges against one another, rather than overlapping them. This creates a completely smooth decking surface.
Reinforced PVC is a practical solution for pool interiors because it can be applied over most existing pool shells to renovate deteriorated pools or to quickly provide an interior finish for new pools.
Matthew Sands
Matthew Sands has more than a decade of successful experience in the construction renovation sector of Renolit, having worked for one of the most well-known European flooring brands. Sands has overseen the renovation of several major projects including La Fenice Opera House in Venice, Italy, and LAC Cultural Center in Switzerland. He can be reached at matthew.sands@renolit.com.
Fall 2024 Back Issue
$4.95 – $5.95
Cool Roofs Can Revolutionize Your Customer’s Facilities to Beat the Heat
Enhancing Moisture Management with Latex Binders
Benefits of Opting for a Liquid-Applied Roof Coating Over a Complete Tear-off
PVC Membrane Solutions For Aquatic Facility Decks
Crystalline Waterproofing: The Science Behind It & Why It’s Important
Case Study: Terra-Lok Triumph
Description
Description
Cool Roofs Can Revolutionize Your Customer’s Facilities to Beat the Heat
By Kyle Ziebarth
As temperatures are reaching unseasonable highs in many areas of the country, more industrial and commercial building owners are trying to rein in out-of-control cooling costs.
Enhancing Moisture Management with Latex Binders
By Mike Christy
Latex binders are polymers that are found in various applications, including waterproof membranes, roof coatings, and waterproof barrier coatings.
Benefits of Opting for a Liquid-Applied Roof Coating Over a Complete Tear-off
By Edward Klonowski
Many commercial roofing manufacturers offer warranties on the lifespan of commercial roofs. But if your roof is damaged and not under warranty, you have options that may be more cost-effective and waste-avoidant.
PVC Membrane Solutions For Aquatic Facility Decks
By Matthew Sands
Decks around swimming pools and splash pads are often plagued with cracks, chips, broken tile, peeling paint, flaking, and delamination. A cost-effective solution is to cover the existing deck or flooring with reinforced PVC deck membrane.
Crystalline Waterproofing: The Science Behind It & Why It’s Important
By Cassandra Brown
Traditional waterproofing methods rely on a barrier system that prevents water from penetrating the surface. Crystalline waterproofing creates a permanent and self-sealing barrier within the concrete.
Case Study: Terra-Lok Triumph
King Mesa Gin in Lamesa, Texas, faced significant water intrusion in the basement’s “press pit,” threatening the safety of its personnel and the integrity of its equipment and products.
Additional Info
Additional information
Weight | N/A |
---|---|
Magazine Format | Digital Download Magazine, Print Mailed Magazine |