By Vanessa Salvia
Photos courtesy of EPRO
EPRO’s PreTak product is used on an office development situated on a former gas station and car service facility in Los Angeles. PreTak is a pre-applied vertical and horizontal HDPE sheet waterproofing membrane combined with a pressure sensitive adhesive backing that mechanically bonds to cast in place concrete and shotcrete in both blindside shoring and underslab applications.
In urban construction and infrastructure projects, space constraints often necessitate innovative building techniques. One such method, blindside waterproofing, has become increasingly prevalent in recent years. This article explores the fundamentals of blindside waterproofing, its applications, challenges, and recent developments in the field.
What is Blindside Waterproofing?
Blindside waterproofing is a type of application that’s necessary for single-sided form walls,” says Scott Schendel, director of product development for EPRO, a waterproofing company established in 1993 in Wichita, Kansas. EPRO does a lot of this type of waterproofing all over the country, primarily in larger urban areas. They frequently work on cut-and-cover tunnels, subway stations, and similar types of infrastructure.
Blindside waterproofing, also known as pre-applied waterproofing, is a technique used in construction scenarios where traditional post-applied waterproofing methods are not feasible. This method is typically employed in zero-lot-line construction or where structures are built against soil or other materials, such as basements, underground parking garages, and tunnels.
“In such cases, the typical process of waterproofing — applying the membrane after the walls have been erected — becomes impractical,” says Cory Deyell, DMX sales manager for North America. “Instead, blindside waterproofing is applied to the retaining wall or excavation support system before the concrete walls of the structure are poured.”
The term “blindside” stems from the fact that the waterproofing is applied “in the blind” – meaning the substrate receiving the waterproofing isn’t visible during application. In this process, waterproofing materials are applied to the shoring system before the concrete foundation walls are poured, or more typically, shotcreted.
Applications
Deyell says that in urban or confined construction sites, where there is limited access to the foundation’s exterior walls, blindside waterproofing becomes essential. Blindside waterproofing creates a barrier that protects against hydrostatic pressure and prevents moisture from penetrating the concrete, he says. “Unlike traditional waterproofing, blindside systems are installed before the walls are built. This ensures the foundation remains protected from the earliest stages of construction, preventing future water damage.”
In many high-density areas, there is minimal space between the building foundation and surrounding structures or property lines, Deyell says. “Blindside waterproofing allows the structure to be built right up to the boundary while still providing essential waterproofing,” he explains.
The Blindside Waterproofing Process
Unlike traditional post-applied methods where waterproofing is applied to an existing concrete substrate, blindside waterproofing involves applying the waterproofing material to the shoring system, then pouring concrete or applying shotcrete against the waterproofing. This reverse order presents unique challenges and requires specialized materials and techniques.
Challenges in Blindside Waterproofing
Blindside waterproofing is typically considered more challenging than post-applied waterproofing. “After that wall is in, there’s no way to inspect the waterproofing after that wall is formed and poured,” explains Schendel. “That’s not true with your typical post-applied system. But in this scenario, you can’t, you’re in the blind. You’re applying the concrete to the waterproofing, and you are assuming and hoping that the concrete has made full contact with the pre-applied blindside waterproofing system.”
This makes it all the more important to ensure that the waterproofing is done effectively and properly. The shotcrete method of applying the concrete is becoming much more prevalent. Shotcrete doesn’t require formwork, and is often used because of the cost savings. But of course, that means the installer is essentially shooting rocks at the waterproofing system, which can damage it.
Schendel explains that sometimes the shotcrete doesn’t consolidate as well or reach behind the rebar, which creates what’s commonly called shadowing — essentially a void behind that rebar. “When there’s a void, that means the structural concrete is not coming in contact with the waterproofing membrane,” says Schendel. “And the reason that can be problematic is that, especially in a hydrostatic condition, you’ve got constant positive side hydro pressure that’s being exerted against that membrane. And if there’s a void space, it has a potential to rupture the membrane, especially if there’s a seam in that particular area.”
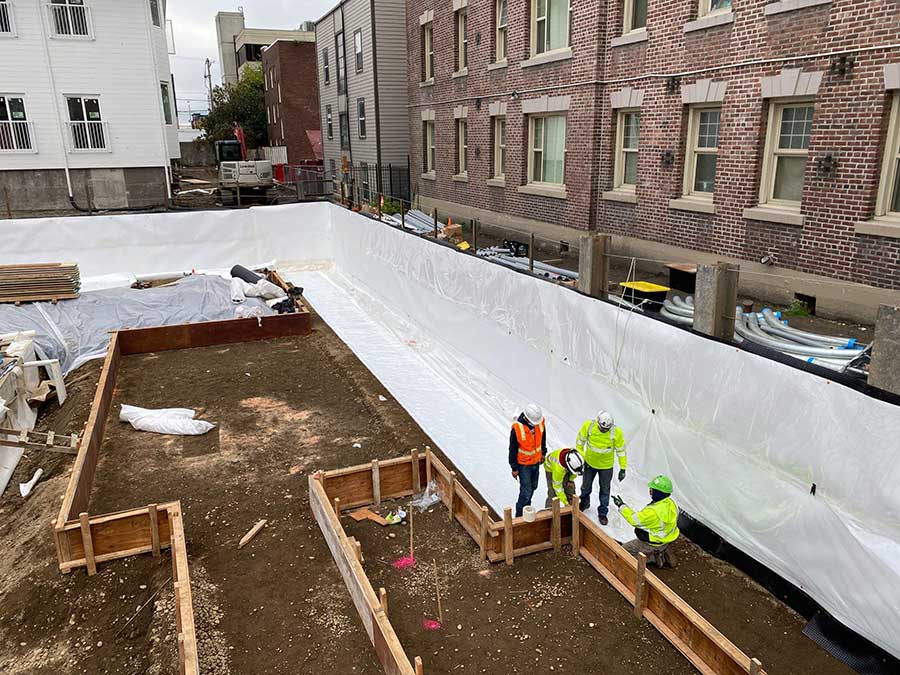
EPRO’s PreTak product is used on Roystone Apartments, an eight-story mixed-use apartment building in Seattle.
Choosing Materials
Given the potential for damage, and that you can’t check the work once installation is complete, it’s crucial to choose a durable material for your waterproofing, and puncture resistance is an important aspect of that. A second crucial aspect is very strong seams in the waterproofing system. Schendel suggests following different ASTM tests that test seam peel strength. Also, strive to reduce the number of seams in the overall system by choosing wider rolls.
Some projects have deep foundations which are in the water table, which creates direct hydrostatic pressure. “You need a very robust system for that application,” says Schendel, whereas with others that may just have nuisance water, the demands are not as tough. “We have varying levels of protection based on what’s necessary for the site conditions.”
EPRO’s PreTak pre-applied sheet membrane utilizes a pressure sensitive adhesive that fully adheres to fresh concrete, whether it be shotcrete or poured in place. Complete and continuous adhesion to the concrete substrate prevents lateral water migration in both blindside shoring and underslab applications. Installation is productive and reliable with up to 8-foot-wide rolls to minimize seams; fewer seams means the likelihood of water infiltration is diminished. “PreTak has a special-formulated acrylic Hydrolap dual-factory adhesive edge,” says Schendel. “The PreTak Hydrolap tenaciously seals seams even in environmentally challenging, wet conditions, creating a performance leading adhesive-to-adhesive lap seam bond. This ability to install in a range of conditions helps projects stay on schedule despite what Mother Nature may have in mind.”
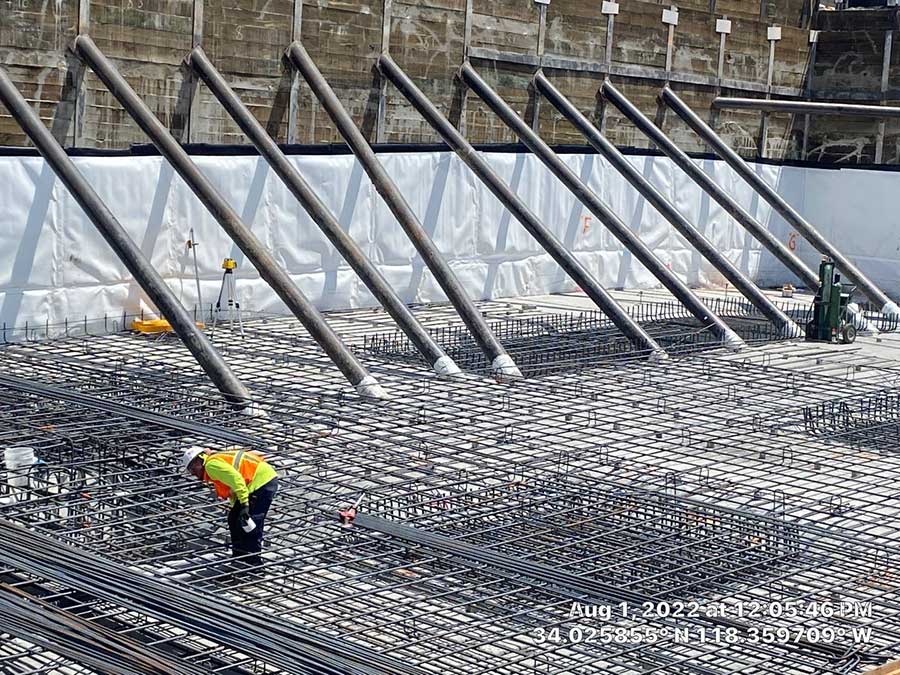
EPRO’s PreTak product is used on an office development situated on a former gas station and car service facility in Los Angeles.
DMX Drain Boards are specialized drainage boards that work in tandem with waterproofing membranes to provide a dual-layered defense against water intrusion. Drain boards are designed to direct water away from the structure. “DMX Drainage Boards have a filter fabric that is heat bonded, not glued, to the 10mm drainage board dimples,” says Deyell. “The Filter Fabric prevents soil from entering the drainage core, creating an air gap between the drainage core and the surrounding soil, allowing water to flow freely to designated drainage systems rather than accumulating near the foundation.”
Drain boards protect the waterproofing membrane from impacts, ensuring its integrity remains intact throughout the construction process. DMX Drain Boards are made of high-density polyethylene (HDPE), a material that is both strong and flexible. “This ensures long-term durability, even in challenging soil conditions, providing reliable drainage and protection for years to come,” says Deyell. “DMX Drainage Boards can be made up to 33,000 pounds per square feet of compressive strength, designed to stand up to the harshest site conditions.”
DMX uses a specially formulated polyethylene that provides high environmental stress-crack resistance to alkalis and acids found in the soil. DMX does in-house testing for compressive strength, Notched Izod (a single-point test that measures a material’s resistance to impact), Melt Flow Index, density testing, and tensile strength.
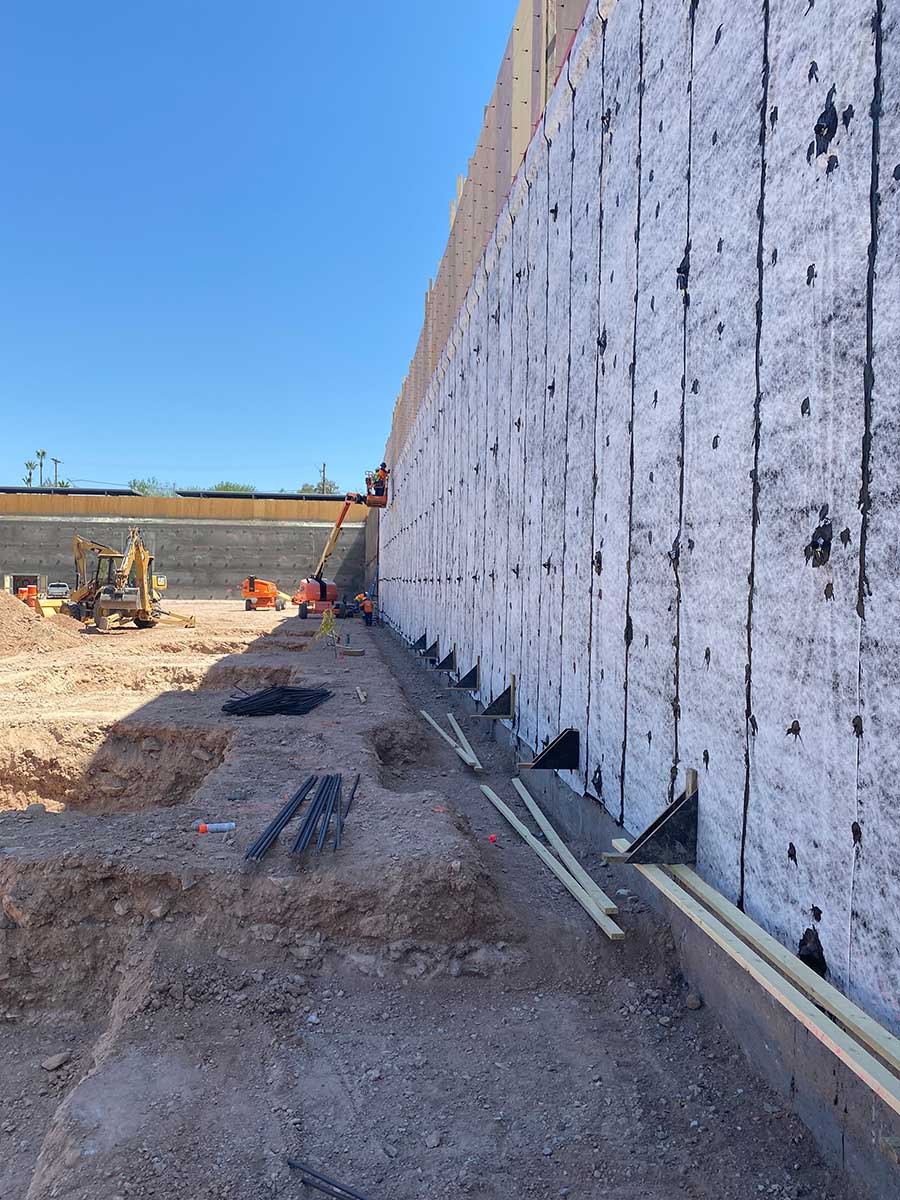
Blindside waterproofing from W.R. Meadows was used on The Grove, a mixed-use campus with office spaces, a boutique hotel, luxury residences, and upscale dining and retail, in Phoenix, Arizona.
Conclusion
As urban development continues to push the boundaries of construction techniques, blindside waterproofing remains a critical component in many projects. While it presents unique challenges, ongoing advancements in materials and application methods continue to improve its effectiveness and reliability. For contractors and builders working in tight urban environments or challenging geological conditions, understanding and properly implementing blindside waterproofing techniques is essential for ensuring the long-term integrity and durability of their structures.
Winter 2025 Back Issue
$4.95 – $5.95
Trade Show Preview
Blindside Waterproofing: Techniques, Challenges, and Advancements
Foundation Repair Using Push Piers And Helical Piers
The Commercial Built-Up Roofing (BUR) Systems
Built-Up Roofing 101 from CertainTeed
Description
Description
Trade Show Preview
Explore waterproofing-related businesses and educational sessions at the upcoming trade shows, including World of Concrete.
Blindside Waterproofing: Techniques, Challenges, and Advancements
By Vanessa Salvia
In urban construction and infrastructure projects, space constraints often necessitate innovative building techniques. One such method, blindside waterproofing, has become increasingly prevalent in recent years.
Foundation Repair Using Push Piers And Helical Piers
By Patrick Nevison, P.E.
This article takes a close look at helical piers and push piers, and explores the differences and uses of each type of foundation repair system.
The Commercial Built-Up Roofing (BUR) Systems
By Rose Morrison
Built-up roofing systems offer various options to meet different building needs and environmental conditions, with benefits that few other roofing types can match.
Built-Up Roofing 101 from CertainTeed
By Abby Feinstein and Ted Winslow
Built-up roofing or BUR consists of multiple layers of hot asphalt being applied between ply sheets thereby building up a waterproof roof assembly.
Carbon Fiber: The New Standard in Structural Repair for Basements
By Vanessa Salvia
In recent years, the field of basement and foundation repair has seen a significant shift towards carbon fiber technology.
Additional Info
Additional information
Weight | N/A |
---|---|
Magazine Format | Digital Download Magazine, Print Mailed Magazine |