By Vanessa Salvia
Photos courtesy of Polyglass USA
Polyglass VertiWrap VPL air barrier membrane permits the passage of water vapor, while acting as a barrier to air and liquid water (above and below).
The fundamental role of air and vapor barriers in building construction remains critical, but the industry continues to evolve with new products and installation techniques. While revolutionary changes may be rare in this field, incremental improvements and installation innovations are making these essential building components more effective and easier to install. Industry experts shared their insights on current trends, common challenges, and best practices for these essential building components.
When it comes to air barriers, contractors have several options across a broad price spectrum. Shaunn Wentworth, New England territory manager for Pecora Corp., explains the range by saying that at one end of the scale is mechanically fastened building wrap and at the other end is fully adhered peel and stick sheet membranes. “People staple building wrap, obviously putting holes with each staple into their wrap,” he says. “Peel and stick membranes are very expensive and labor intensive.” Fluid-applied products, he notes, hit “the cost sweet spot right in between with no sacrifice in performance.”
Understanding Air and Vapor Barriers
Iltaz Alam, senior product manager of GCP, explains the basic distinction. “Every barrier is an air barrier, and then it depends what type it is, whether it is allowing vapor or it is not allowing water vapor. In cases when it allows vapor, it is called a vapor permeable air barrier. And in case it is not allowing water vapor, it is called a vapor impermeable air barrier.”
While the concept might seem straightforward, Alam notes that complexity emerges in the details. “It sounds very simple because you can have a sheet-applied air barrier or a liquid-applied air barrier. But when you get into the details, that’s where it starts to become complex.”
Fluid-Applied Systems and Their Advantages
Fluid-applied barriers offer unique advantages, particularly in complex architectural situations. As Wentworth explains, “Anything that juts out from the plane of the building, what we call “bump outs” above windows, anything that juts out beyond the flat plane of the building has to be worked around with a sheet membrane. Whereas with our material, where it’s generally applied with a roll or a spray, you don’t have that same amount of work of trying to cut it into shapes and make it work around all the different corners.”
Chemistry and Weather Considerations
The chemical composition of fluid-applied barriers can significantly impact their functionality. “Most of the fluid applied are water-based products, which means you can’t use them over the wintertime,” Wentworth notes. “Once you get below 40 degrees Fahrenheit, you can’t use them.” However, newer hybrid formulations can be applied in much colder conditions, some down to 5 degrees Fahrenheit, offering greater flexibility for year-round construction.
Another key distinction lies in application thickness. “Most of the other fluid-applied products out there require a thick mil application,” Wentworth explains. While some products require 40 mils thickness or greater, newer thin-mill systems require only 10 to 14 mils. This difference makes it easier to verify proper application. “If the material looks opaque, then it’s a good indicator,” he says. “You can be reasonably assured that it’s been applied at the proper thickness.”
Regional Considerations and Building Design
Climate and building use play important roles in determining the appropriate barrier type. As Alam explains, “If you are in a high-temperature, high-humidity region, you would use a vapor-impermeable membrane, because you need to prevent moisture from entering the building envelope while stopping the air leakage to minimize the load on HVAC systems.”
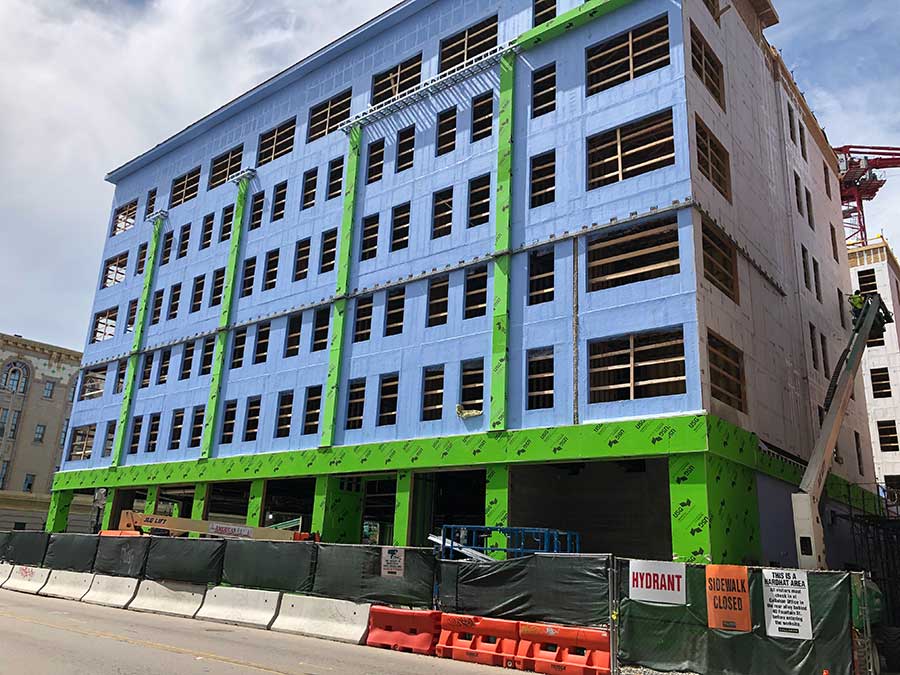
Pecora’s Pecora XL Perm Air Barrier is a primerless, single component, high performance fluid applied STPU (Silyl Terminated Polyurethane) vapor barrier. Photos courtesy of Pecora Corp.
Construction Sequencing and Project Management
Proper sequencing remains important regardless of the barrier type chosen. As Wentworth emphasizes, “You can’t start waterproofing the walls until you have a roof on.” This sequencing affects crew sizing and project timeline decisions.
“You can only go as fast as the framers who are putting up the building ahead of you,” he says. “They want to get the electricians and the plumbers and everybody going as quickly as possible. And they can’t get in and do their thing inside the building until we tighten up the outside.”
The requirements change significantly for different building types. “If you are in a colder region where there is not a humidity problem, but you are building a cold storage, for example, or you are building a data center where you are always running air conditioning inside… in those conditions, people prefer to design their wall in a way that restricts air movement from inside to the outside,” Alam adds.
For coastal regions, different considerations apply as the air barrier selected must address specific challenges related to high humidity, salt air, and frequent exposure to moisture. “You will have to allow the water vapor to escape from the building,” Alam notes. “Otherwise, when the temperature goes down and you are running AC inside your house, it will condense and become water, and that will create mold. In those situations, you have to allow a vapor-permeable air barrier that will restrict air movement, so it will not have a big load on your air conditioning. But at the same time, you will avoid any condensation between your walls.”
New Developments and Innovations
Mark Franciosi, Technical Services Leader – Building Envelope Solutions, of Polyglass USA highlights integrated products and panelization, an emerging trend in construction methods. “The need for labor considerations is more relevant now than ever,” Franciosi says. “The shortage of skilled labor continues to trend and manufacturers are faced with finding ways to integrate product assemblies to assist with keeping construction schedules on track and reducing the need for laborers to complete the work on time and on budget.”
In addition to integrated assemblies, the panelization market has seen growth. This trend, while not entirely new, has gained momentum in recent years due to continued challenges in constructability in urban environments that have logistical challenges. “It’s not a new concept, but we’re just seeing a lot more of it in the past probably three or four years,” Franciosi explains.
Brian Carey, product manager for Carlisle Weatherproofing Technologies, points to innovations in board stock air barriers. “The newer developments are the board stock air barriers. It’s about time and labor savings because you’re going to put up your continuous insulation and a durable and continuous membrane air barrier in one single step, instead of doing it in two steps.”
The advantage of this approach becomes clear in practical application. As Carey explains, “It’s actually much easier to install a self-adhering sheet when it’s already adhered to a board than trying to put it on loose,” he says. “Picture trying to hang wallpaper versus trying to hang foam board. One’s a flimsy thing with glue on the back of it and it’s hard to get on without wrinkling. The other one is a board that goes on nice and easy.”
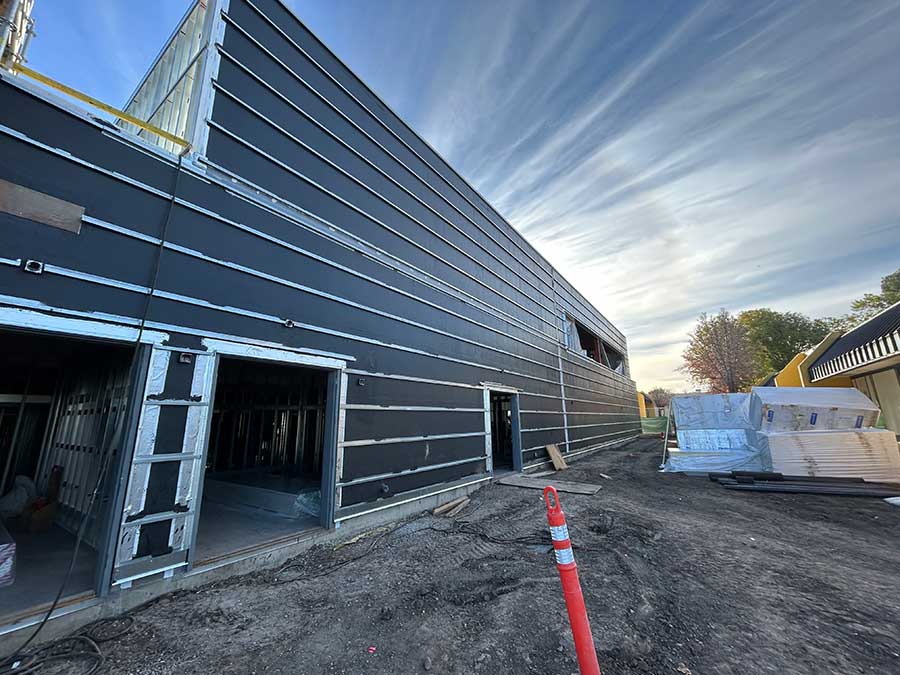
GCP’s Perm-A-Barrier VPL 50RS UV Stable Membrane is a fluid applied, one component, STPE (Silyl Terminated Polyether) vapor permeable air and water barrier Photos courtesy of GCP Applied Technologies
Product Innovations
Manufacturers continue to develop products that address specific challenges. Alam highlights recent advancements. “Perm-A-Barrier VPS 30 is a very good example of the advancement into the air barrier industry,” he says. “It’s a primer-less membrane. So whether you are doing the application as low as zero degrees Fahrenheit or as high as 104 degrees Fahrenheit, you can easily use that product without any primer. Perm-A-Barrier Ultra is another example of recent development in the air barrier industry; this product withstands very high heat up to 300F, making it a suitable choice for parapet application.”
Franciosi notes improvements in acrylic technology: “Historically, one of the main technologies in the market for air and water barriers has been acrylic-based, fluid-applied coatings. And one of the downfalls of that type of chemistry has been that it doesn’t have very good early rain resistance… Polyglass has been able to formulate some acrylic-type technologies that have a pretty significant impact on early rain resistance.”
Common Challenges and Installation Mistakes
These experts highlighted installation mistakes that can compromise barrier effectiveness. David Delcoma, operations manager for MFM Building Products, emphasizes the importance of proper ventilation. “The number one key to using a self-adhered membrane is proper ventilation,” he says. “Anytime a vapor barrier is [installed], you have to have proper ventilation of the roof, of the side wall, of the foundation.”
Delcoma shares a cautionary tale: “We had a builder who was installing hollow wooden posts on the front porch of a house. He put our membrane inside of it, but what he didn’t realize is any moisture that gets in there has nowhere to go, and it will eventually work its way through the overlaps. And it began to rot inside because he had no ventilation.”
Carey identifies chemical compatibility as a crucial consideration. “The wall membranes will touch a lot of different things… windows, roof, adjacent waterproofing systems, all kinds of different sealants and flashings in particular, that may or may not be compatible with the air barrier membrane.” The consequences of incompatibility can be severe, let’s say, for example, with windows. If you have a building with a lot of windows and you use an incompatible window sealant. “The consequence of that is that particular asphalt-based membrane can liquefy and run out so that you get ugly, oily stains all over your building that will never stop bleeding out,” he says.
UV exposure is another important consideration. As Delcoma explains: “Most manufacturers state that their membrane can be exposed to the atmosphere for 30 days, 60 days, 90 days, 180 days, etc. That’s important, because what happens is the membrane is not designed to be exposed to UV any longer than what is recommended,” he says. “UV will start to break down the film surface. It’ll start breaking down the adhesive system underneath it, which can create potential leak points, especially at the overlap areas. To avoid a potential call back, you need to adhere to the recommended exposure time.”
Best Practices and Guidelines
The experts unanimously stressed the importance of following manufacturer guidelines and building codes. As Delcoma states, “Every manufacturer has installation instructions and technical literature that the installer really needs to pay attention to.”
Communicate with manufacturers. “Our technical service people probably take about a dozen calls a day from builders asking questions about how to use the product, and we love that,” Delcoma shares. “We don’t want a bad name. We don’t want somebody installing it incorrectly, and having problems but never contacting us.”
Proper sequencing is also key. Carey explains, “Sometimes installers will put the membrane air barrier on the wall, and the roof is wide open,” he says. “Even with the vapor permeable ones, if you get water going in behind it, it’s going to take a long time for that water to dry out, and it will probably ruin the substrate and the membrane.”

MFM’s Peel & Seal is an aluminum foil-faced membrane that is a vapor barrier. Photo courtesy of MFM Building Products
Looking Forward
While fundamental technologies remain largely unchanged, the industry continues to focus on improving installation efficiency and performance reliability. As Carey notes, successful air barrier implementation relies on four key principles. “Durability, continuity, moisture management, and fire safety,” Cary says. “Whatever you use, make sure that you meet all those things.”
The evolution of air and vapor barriers continues to prioritize these essential functions while making installation more straightforward and reliable. With proper attention to detail, appropriate product selection, and careful installation, these important building components can effectively protect structures for their entire lifespan.
The success of any air barrier system ultimately comes down to reliability and proven performance. As Wentworth notes about his repeat customers, “The proof is in the pudding when customers come back.”
Spring 2025 Back Issue
$4.95 – $5.95
Advancements and Best Practices in Air and Vapor Barriers
Moisture Management in Basements
The Role of High Voltage Electronic Leak Detection in Waterproofing Integrity
Case Study: GCP Waterproofs the Bronx Zoo River Under Crocodile Supervision
Case Study: EPRO Protects Over Half a Million
Description
Description
Advancements and Best Practices in Air and Vapor Barriers
By Vanessa Salvia
The fundamental role of air and vapor barriers in building construction remains critical, but the industry continues to evolve with new products and installation techniques.
Moisture Management in Basements
By Erika Lacroix
Basement moisture problems are one of the most common challenges in residential construction and remodeling.
The Role of High Voltage Electronic Leak Detection in Waterproofing Integrity
By Jim Campbell
Leaks in roofing systems can lead to costly damage, including structural compromises, mold growth, and significant financial losses due to unplanned repairs.
Case Study: GCP Waterproofs the Bronx Zoo River Under Crocodile Supervision
The Bronx Zoo, one of the largest metropolitan zoos in the world, faced a critical construction challenge in the spring of 2024.
Case Study: EPRO Protects Over Half a Million
Square Feet of New Los Angeles Construction
EPRO Services Inc. provided waterproofing solutions totaling over half a million square feet to high-profile Los Angeles sites.
Additional Info
Additional information
Weight | N/A |
---|---|
Magazine Format | Digital Download Magazine, Print Mailed Magazine |