By Mike Ennis
Wausau High School in Wausau, Wisconsin, chose this EPDM single-ply roofing system for its superior puncture resistance.
It may be hard for some waterproofers to admit, but when it comes to commercial construction, roofing contractors are the industry’s closest cousins. The United Union of Roofers, Waterproofers and Allied Workers has kept this tradition alive. The union’s motto is “proud, professional and committed to excellence.”
Both trades are also combating a common enemy: water intrusion into the building envelope.
Today, one of the roofing contractor’s most powerful weapons in the war against moisture incursion is the single-ply roofing membrane. Without question, thermoplastic membranes have been the fastest growing form of low-slope roofing for more than a decade, while EPDM “rubber” roofing has maintained an impressive track record of performance.
Single-ply roof membranes were introduced in the early 1960s and began to grow in use after the oil embargo of 1973 inflated the price and restricted the availability of quality roofing asphalt for built-up roofing (BUR) applications.
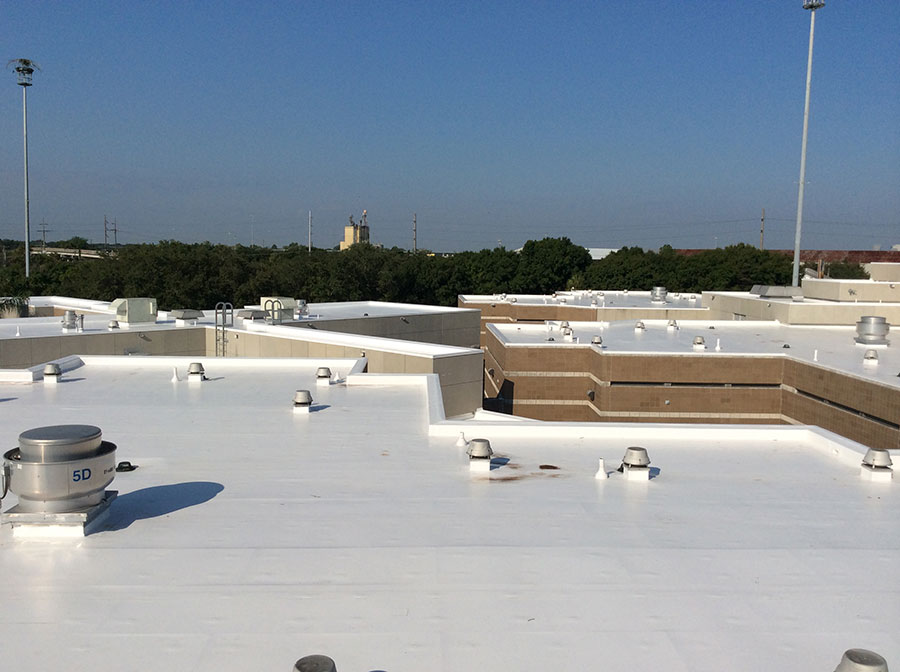
Thermoplastic membranes like PVC offer many benefits, including long-term weathering resistance, cold temperature flexibility, tear resistance, puncture resistance, chemical resistance and heat-seaming capability.
By 1984, Ducker Research Inc. (now Ducker Worldwide) predicted single plies (including PVC and PVC alloys, EPDM, Hypalon [CSPE] and CPE), would capture 25% of the low-slope market. By the middle of that year, single plies market share reached 35% of the roofs installed and Ducker Research soon revised its year-end forecast.
By 2006, thermoplastics’ market share had grown astonishingly. TPO and PVC alone made up about 30% of the commercial roofing market, according to Ducker Research. Along with EPDM, single plies were close to reaching 50% market share. At the same time,the Single Ply Roofing Industry (SPRI) reported that from 2005 to 2010, several billion square feet of single-ply membrane were sold in North America, the great majority of which have performed without issue.
Even in the frigid climates of northern Canada, single plies were making a big impact.
“Single-ply membranes, including thermoplastics and EPDM, have become a great addition to the roofing industry,” says Wendy Fraser, technical manager of the Canadian Roofing Contractors Association, headquartered in Ottawa, Ontario.
In response to single ply’s growth, SPRI, the association representing sheet membrane and component suppliers to the commercial roofing industry, was formed in 1980. SPRI is an accredited standards developer for the American National Standards Institute (ANSI). Over the past several years, SPRI has developed 12 ANSI standards, four of which have been adopted by the International Building Code (IBC).
Attributes of TPO/PVC Membranes
Some attributes shared by TPO and PVC membranes include long-term weathering resistance, cold temperature flexibility, tear resistance, resistance to puncture, chemical resistance and heat-seaming capability.
These membranes can be manufactured in a wide range of colors, do not cure after exposure to the elements and remain capable of hot-air welding throughout their service lives.
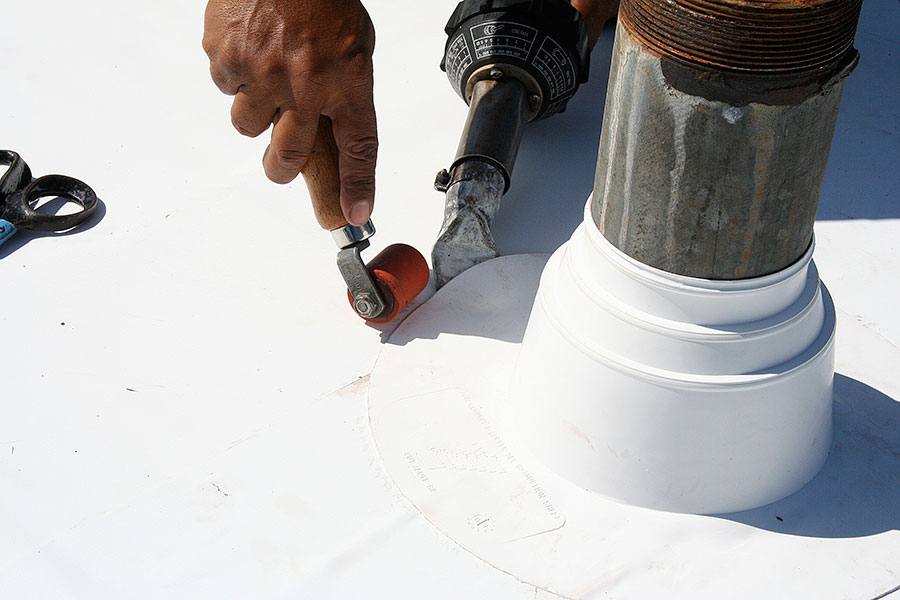
Prefabricated TPO/PVC accessories like the TPO pipe boot shown here continue to be a boon to roof designers.
Each TPO and PVC membrane has a unique formulation. TPO and PVC membranes also feature a reinforcement layer made of either polyester or fiberglass, incorporated at the factory using a variety of techniques.
Thermoplastic membranes are highly resistant to a variety of chemicals, and both TPO and PVC materials are formulated to be fire-resistant. When designed as part of an appropriate roof assembly, both TPO and PVC roofing systems can achieve Underwriters Laboratories (UL) Class A fire-resistance listings. Beyond fire testing, thermoplastic membranes have been approved by Factory Mutual Approvals and have wind-uplift resistance classifications exceeding 500 pounds per square foot.
The Evolution of EPDM
EPDM is a thermoset material that is cost-effective, simple to install, and quickly became known for its exceptional hail resistance, UV stability, and weathering resistance due to the cross-linked nature of its chemistry and the UV-absorbing power of its raw materials.
There are several main areas in which major enhancements have been made to EPDM system technology since it was first developed nearly 50 years ago.
The first area of improvement was in EPDM seaming technology. In the 1970s, EPDM seams were created using white gas and a neoprene-based splicing adhesive. However, the neoprene polymer in the splice cement could break down and lose strength with prolonged exposure to ponding water.
In the mid-1980s, a butyl-based splice adhesive was developed to be used in lieu of white gas to clean the seam area. Waterproofers may remember that butyl-based adhesives were used in pond liner applications and are very tolerant of ponding water. However, the seaming process still involved quite a few steps, leaving seams prone to variations caused by workmanship techniques and installation conditions.
It wasn’t for another 20 years that customized primers and double-sided seam tape emerged. These products dramatically simplified the seaming process and reduced workmanship errors.
Around 2005, seaming was elevated to the next level with EPDM sheets and factory-applied tape, in which splice primer and splice tape are pre-applied to one side of the sheet in a factory-controlled environment. Factory-applied tape not only improved seaming productivity by 65%, it also improved seam quality so dramatically that one major roofing manufacturer saw an 80% drop in seam-related warranty claims.
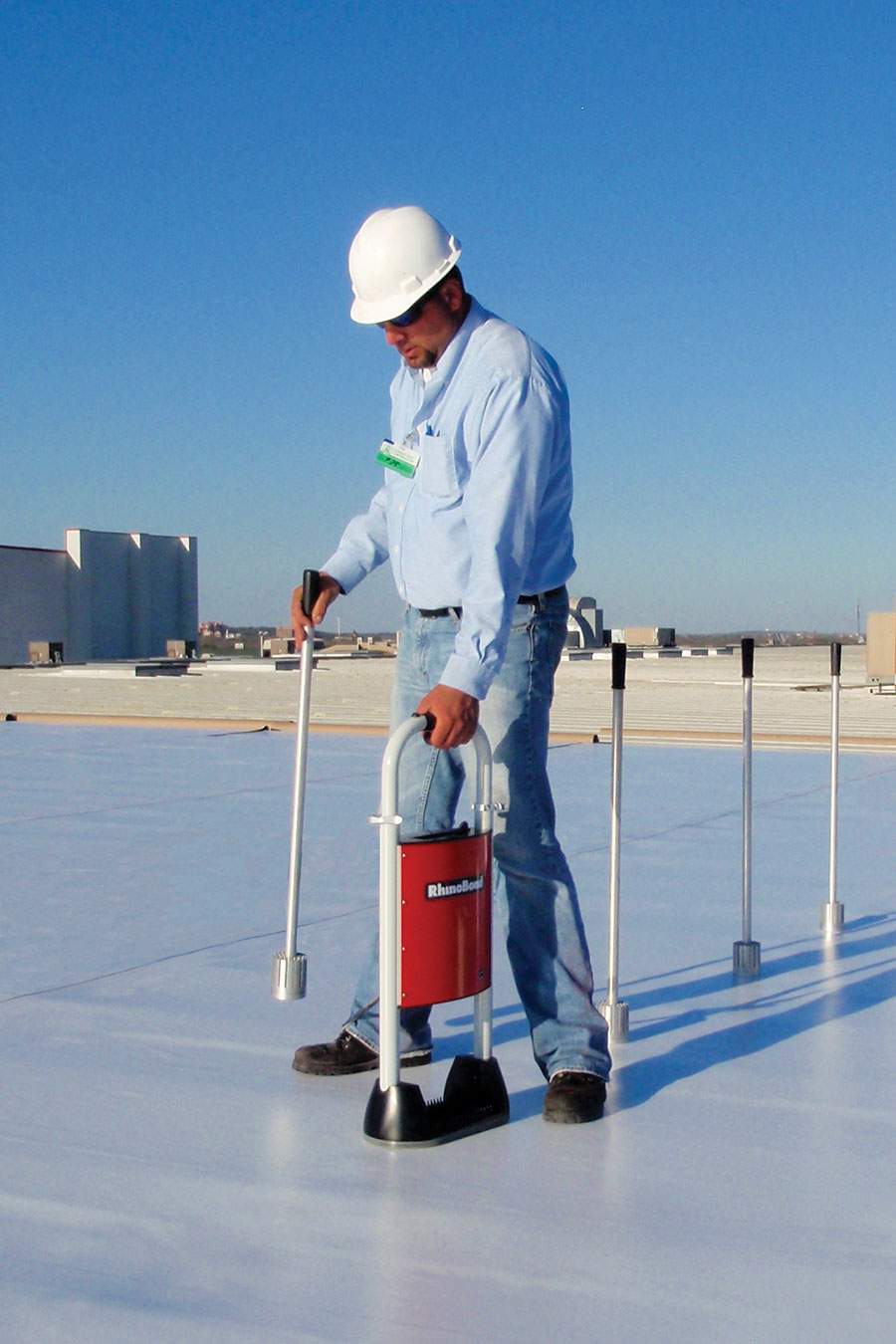
Another innovation that is gaining in popularity is induction welding of TPO and PVC thermoplastic membranes. A PVC application is shown here.
In 1989, reinforcing perimeter strips for EPDM were introduced. Today, the latest pressure-sensitive, six-inch x 100-foot or 10-inch x 100-foot pressure-sensitive, reinforced membrane strips come in rolls and are used to secure TPO membranes in the roof perimeter or at the base of a vertical wall.
Manufacturers introduced a reinforced EPDM sheet that contained an internal scrim for added toughness and durability in the mid-1980s. Today, contractors have the option of a 90-mil EPDM, which has twice the puncture resistance of the original 45-mil rubber.
In 1992, wall and curb flashing details were updated to require cured (as opposed to uncured) EPDM membrane for added toughness, durability, UV resistance, and weatherability.
In 2018, one manufacturer also introduced a Velcro securement system to fully attach fleeceback EPDM and TPO membranes to polyiso insulation without adhesives. This process eliminates temperature and VOC restrictions and features wind uplift ratings comparable to traditional adhered single-ply roof systems.
What Makes Single Plies Popular?
One factor driving the growth of single-ply membranes is the focus on the energy efficiency of buildings. Global warming has become a focus point for many property owners, specifiers and government agencies. Electrical blackouts caused by the increased use of air-conditioning have energy providers looking for ways to reduce peak electrical demand while designers attempt to limit a building’s carbon footprint. Highly reflective roof membranes can help alleviate the heat load placed on a building by reflecting sunlight and maintaining a lower surface temperature than darker colored roof surfaces.
Additionally, the U.S. Green Building Council (USGBC) created its LEED certification program for buildings that are designed, constructed and operated with sustainability in mind. The program assigns points for certain types of designs and provides a construction “point” for roofs that have high reflectivity, such as PVC and TPO membranes, as well as sustainable products like EPDM.
Perhaps what contributes most to the growth of thermoplastic and thermoset membranes is the variety of attachment methods.These include stone ballast or pavers; mechanical fasteners and plates and/or metal bars; induction welding components (TPO and PVC only); and adhered with bonding adhesives. Common adhesives used as bonding agents include solvent-based, waterborne and 100% solids-reactive products, including two-part and moisture cured/activated adhesives.
As waterproofers know from experience, certain geographies in the U.S. limit the maximum content of volatile organic compound (VOC) in various adhesives. As such, TPO, PVC and EPDM manufacturers have developed low-VOC water-based adhesives, low-rise foam and moisture-cured adhesives, and self-adhering membranes, inclusive of self-adhering flashings and details for roof system penetrations. These products can be used anywhere there are stringent low-VOC requirements that limit or exclude the use of solvent-based adhesives (subject to temperature and humidity limits).
Formulating chemists have engineered waterborne adhesives to sufficiently bond EPDM, TPO and PVC membranes to various substrates such as roof insulation, wood, concrete, lightweight insulating concrete and other surfaces. Again, these water-based adhesives are especially attractive when local air quality legislation restricts VOC content in bonding adhesives.
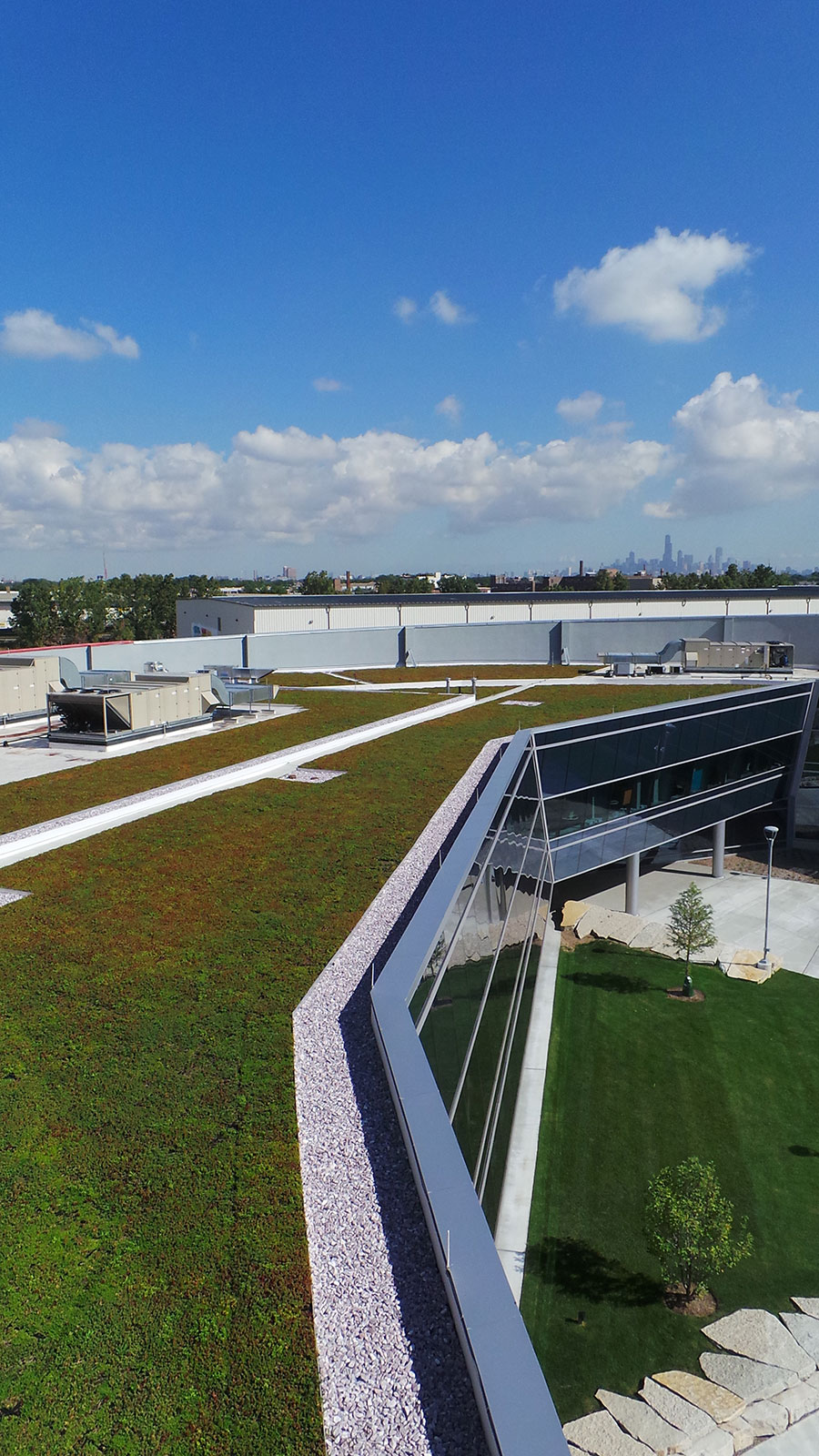
One factor driving the growth of TPO/PVC membranes is the “green” building movement and the increased use of reflective roofs. A TPO application with green roof is shown here.
Single-Plies Are Not A ‘Cure-All’
While the market has shown that the popularity and performance characteristics of single-ply membranes are clear, every roofing product exhibits strengths and weaknesses. While single-plies currently represent 67% of the low-slope membrane roofing market, there are installations where their traditional uses are not recommended.
All single-ply membranes rely on one layer of roofing material to waterproof the building. More traditional roofing options, such as built-up roofing and modified bitumen, offer redundancy in the form of multiple layers of roof membrane protection. Some asphalt-based product specifications also offer even greater puncture resistance and are more forgiving of rooftop abuse than standard thickness single-ply membranes.
Another installation where care should be taken is one with high heat loading combined with concentrated exposure to sunlight, although this is less of a concern in northern climates. Most roofing materials degrade over time when exposed to heat and ultraviolet light and their long term performance depends on formulation and onsite conditions, so high temperatures and high UV exposure—such as south- and west-facing walls in extremely hot climates— may warrant either a thicker membrane or a membrane formulated for such severe conditions.
Summary
There is one thing that has not changed in the low-slope roofing market over the years: the building owner usually gets the roof performance he or she pays for. Single-ply membranes can meet a variety of different building requirements by offering a range of options. It is also important to note that these high performance roofing membranes are compatible with the latest rooftop technologies, including solar arrays and vegetative roofing. Given the wide variety of installation options available, it is easy to understand why these membranes have continued to gain in use and provide long-term performance for building owners.
Mike Ennis is the Single-ply Roofing Industry’s (SPRI’s) technical director. He can be reached at info@spri.org.
Summer 2018 Back Issue
$4.95
Livable Basements
AVAILABLE AS DIGITAL DOWNLOAD ONLY
Description
Description
Additional Info
Additional information
Magazine Format | Digital Download Magazine, Print Mailed Magazine |
---|