View of Olympic Village Station, a stop on Vancouvers Canada Line subway. The dimpled drain mat at the left tunnel entrance was used to waterproof the bored tunnel going under False Creek.
When the jobsite is measured in miles, and the specs call for literally acres of waterproofing, it takes a special kind of waterproofing contractor to ensure the project goes smoothly. Recently, two Canadian cities—Vancouver, B.C.; and Calgary, Alberta—have expanded their light rail transit systems, and both asked the same company to provide more than a million sq. ft. of waterproofing.
Vancouver’s Canada Line
The light rail project in Vancouver was started in 2005, as part of the city’s preparations for hosting the 2010 Winter Olympics. The 12 miles of track would connect downtown with the airport and the nearby city of Richmond. During the planning stages, the line was known as the “Richmond-Airport-Vancouver Line”, or RAV-Line, but was later changed to “Canada Line,”
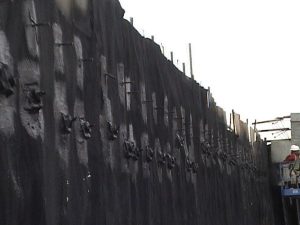
The cut -and-cover tunnels used shotcrete and soil nails for retention. This meant extensive detailing was needed to ensure the waterproofing was secure.
SNC-Lavalin, a Montreal-based engineering and construction company with operations around the globe, served as general contractor. Instead of funding the projects primarily through bonds, SNC-Lavalin agreed to build the job on the condition that they operate the line for 35 years.
Of the 12 miles of tunnels, almost half (more than 9,000 meters) would be underground. SNC quickly determined that it would be cost-prohibitive to seal the entire length of underground tunnels.
Instead, designers specified that the tunnels would be sealed at the construction joints only using waterstops. The nine underground stations, on the other hand would be completely waterproofed, along with a few isolated sections of tunnel, such as areas with perched water tables, and the section of track bored underneath creeks and rivers. The “portals” —tunnel entrances where the tracks emerge at grade— would also receive treatment.
Even with this reduction in scope, the amount of waterproofing needed was mind-boggling. The stations were two or three stories deep, with more than 100,000 sq. ft. of surface that needed treating at each one. It totaled more than a million square feet of work. To make the scope of work manageable, each station was bid out as a separate project.
Dawson Bradley Waterproofing of Chilliwack, B.C., got the nod to do the waterproofing on three stations—Broadway, Yaletown and Millennium—using a system marketed by Epro Services, Inc. a Kansas waterproofing supply company.
“Those were all cut-and-cover stations,” says Dave Polk, president of Epro. “But the stations are in downtown Vancouver, and meant digging out entire streets.”
As the excavation progressed downward, walls were stabilized with soil nails and shotcrete, so by the time the crew from Dawson Bradley arrived, they were waterproofing against an uneven shotcrete surface punctuated by literally thousands of soil nails. They waterproofed the job blindside against that surface.
The first step was hanging a dimpled drainmat against the shotcrete. The next step was carefully detailing around all of the soil nails, and seaming and detailing seams in the dimple board. Once the drainage composite was in place, they sprayed on the waterproofing membrane.
Crews could then set the rebar and apply the final layer of concrete, shot onto the wall as high-pressure shotcrete.
Polk explains, “With this method, the concrete fills all the way to the back of the dimples, so there’s tremendous bonding between the structural wall and the waterproofing.”
Waterproofing began in the closing months of 2007, and despite the scale of the task, was completed 18 months later. The entire line, which was scheduled to open in November 2009, was completed four months ahead of schedule. In Feb. 2010, when the Winter Olympics were in full swing, the new subway averaged well over 200,000 riders a day.
The line remains popular with locals. More than 100,000 people board the light rail every day, kept dry by an innovative combination of concrete, drainmat, and waterproofing.
Calgary’s LRT
Six hundred and fifty miles to the east, Calgary, Alberta is also expanding its light rail transit (LRT) system. Running west from the city center, the West LRT line will serve an area that is expected to grow from 90,000 to approximately 120,000 residents in the next 20 years.
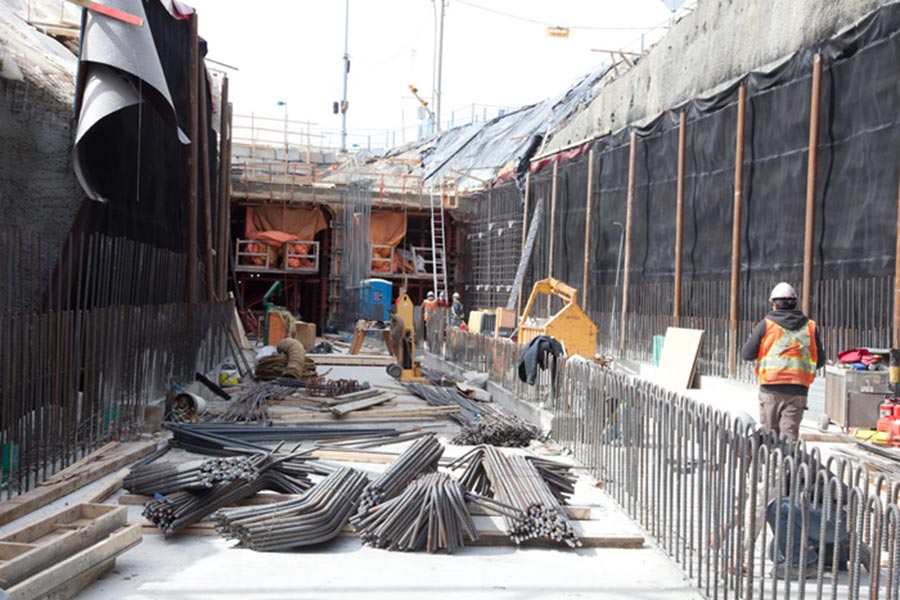
Sheets of drainmat hang on the wall in preparation for the spray-applied waterproofing.
In late 2007, the city approved funding for construction and asked engineering firm Hatch-Mott-MacDonald to manage the bidding, which was done as a design-build job.
The waterproofing portion of the work was complex and massive. A one-mile (1.5 kilometer) section of the tunnel was below the water table, so all walls, floors, and ceilings would have to be completely waterproofed. Additionally, several of the stations would be built on “brownfield” sites. One is near a former automobile repair yard, another on the site of an old dry cleaning business, so those stations would need a gas barrier as well.
In total, the job called for more than a million square feet of waterproofing.
Because it was a design-build job, the waterproofing contract was bid as a single job, rather than as individual stations as in Vancouver.
To tackle a job that massive, Mike Downey Contractors of Calgary teamed up with Seal It Waterproofing of Wichita, Kansas. This joint venture won the contract, choosing the same waterproofing system from Epro that was used on the Vancouver subway.
“Calgary was cut-and cover,” says Polk, at Epro, ‘but it was a little different than Vancouver because it involved waterproofing the entire tunnel all in water table conditions, and also in contaminated sites.”
Polk adds that the deepest areas reach 60 feet below grade, and that parts of the line are a dual tunnel layout.
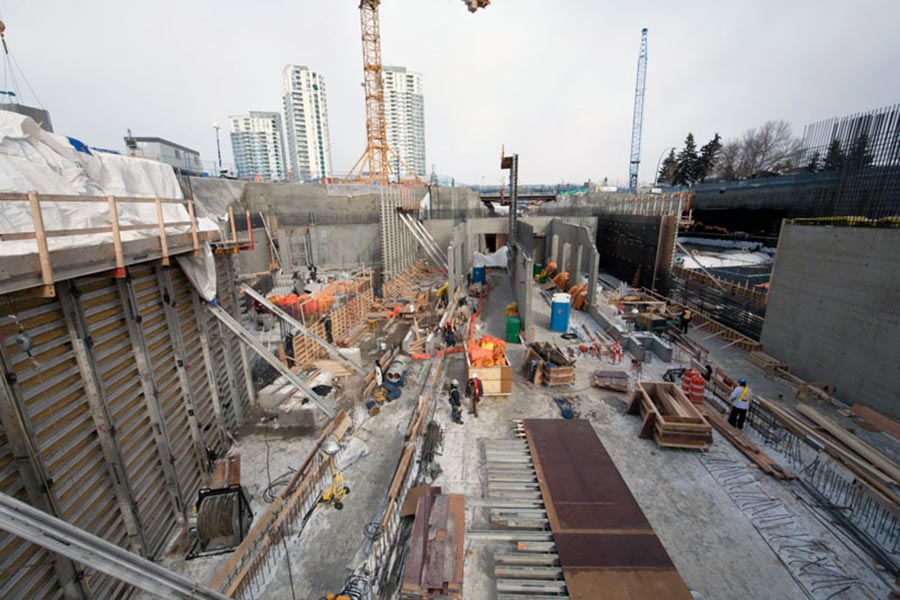
Westbrook Station near downtown Calgary required special waterproofing materials to deal with the contaminated soils onsite.
Work began in the summer of 2010, and is expected to last about 15 months.
Like the Vancouver job, the soil is secured using shotcrete and soil nails, but because of the water conditions, the waterproofing technique was much different.
“We’re doing underslab on everything,” says Polk. “It’s a 60-mil HDPE film, and that underslab system is bath-tubbed up the wall to water table height.” It’s brought up over the dimple drain mat, and takes the place of the spray membrane below the water table. Above the water table, a spray membrane is used as in Vancouver.
Once the walls are in place, the roof is poured in place. The concrete is placed in 14- or 20-meter sections using slip-forms. The forms are designed so that the top two feet of wall are poured as part of the roof assembly. By placing the cold joint on the smooth face of the wall, it’s easier to waterproof.
The roof experiences a tremendous amount of construction traffic during the backfill process, so the membrane chosen had to be extremely durable.
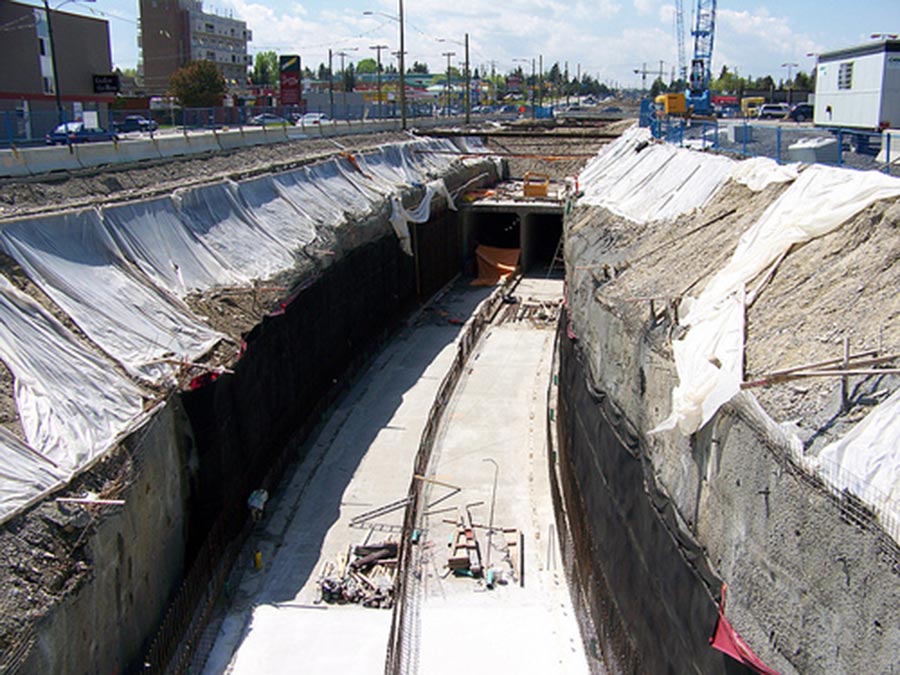
Unlike the Vancouver job, West LRT required waterproofing floors, walls and ceilings along five miles of tunnel.
“We start with a spray-applied liquid membrane, and then lay down a fabric reinforcement,’ says Polk. “Then we spray another membrane over that, which creates a reinforced monolithic membrane that will stand up to site conditions. That gets covered with a 15-mil polyolefin film, and then a heavy duty drainage composite, which we tie into composite on the walls.”
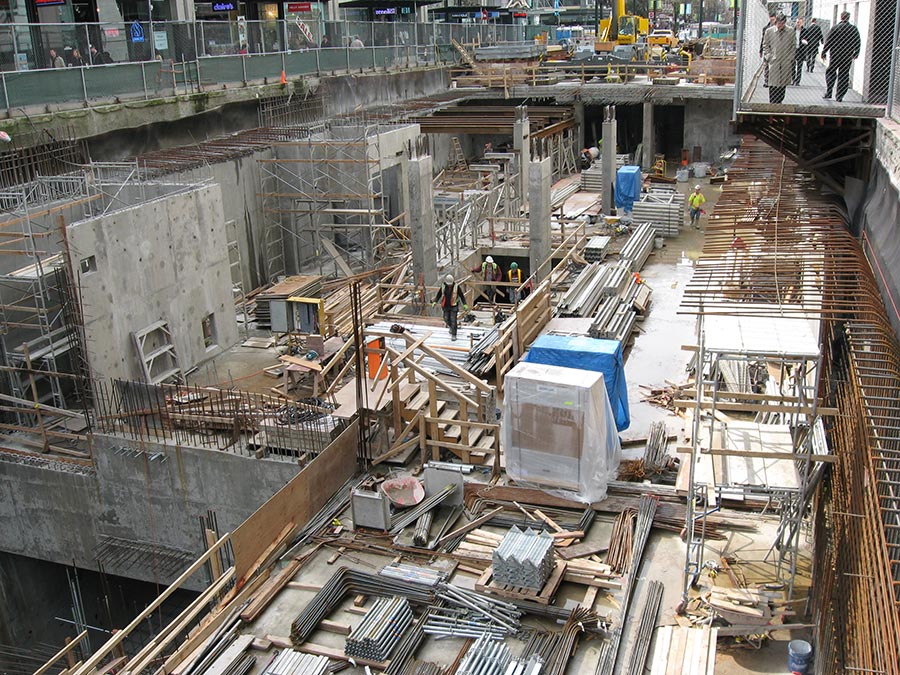
Vancouver’s City Street Station extends more than sixty feet below grade on three separate levels.
Interestingly, one of the contractors working on this massive project started their company as a residential waterproofing business. Mike Downey, of Mike Downey Contractors, says hemade his reputation by specializing in a quality waterproofing system that works. “I don’t try to do everything,” he says. “I have a system that I’m very familiar with, and stick to that.”
Based in the Wichita, Kansas area, he got a break when a competitor underperformed on a tunnel job and the GC called Downey to finish the work. That led to additional work, and by the time the West LRT line went to bid in 2008, Downey had a portfolio of completed jobs that included water table work, cut-and-cover tunnels, and contaminated sites.
“It just happened incrementally,” says Downey. “If you do quality work using quality products, and keep an eye on the bottom line, success will naturally follow.”
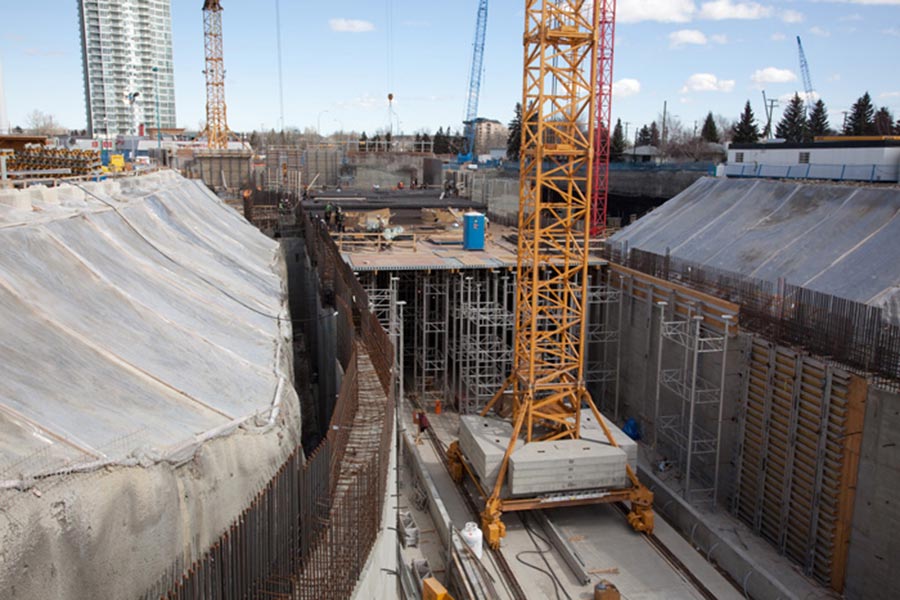
Installing the roof on Calgary’s Westbrook Station.