By Clark Ricks
A significant portion of concert hall at Sonoma State University sits below grade and below the water table. An innovative dewatering system had to be developed to keep the building dry. Here, Christopher Dinno explains foundation construction to a group of visitors.
The Green Music Center, a new 1,400-seat concert hall located in the heart of Northern California’s wine country, is a world-class facility with remarkable acoustics, beautiful architecture, and scenic views. One of the buildings most remarkable and important features, however, will go completely unnoticed by the tens of thousands of guests who will visit the facility.
Located at Sonoma State University, a significant portion of concert hall sits below grade. With a water table just five feet below the surface, an innovative dewatering system had to be developed to keep the building dry—and the concert hall quiet.
The idea of building a world-class concert hall in Sonoma County was first proposed in 2000, but funding and other concerns delayed approval until 2005, when the project was expanded to include a separate recital hall and academic buildings. Rudolph & Sletten, a general contractor familiar with building on the Sonoma State campus, got the nod.
Temporary Dewatering System
Before excavation could begin, a temporary dewatering system had to be installed. A series of 14 wells were drilled 20 to 30 feet deep and connected to water disposal lines. Because the California Water Quality Control Board prohibits dumping water into any natural creek or drainage, the lines were routed into the university’s stormwater drains. CWQCB inspectors made daily jobsite visits to ensure compliance until the permanent system became operational.
“When we first started those pumps, they were pumping 400,000 or 450,000 gallons of water per day,” says Grant Ricks, project manager for the job. “It stabilized at around 320,000 gallons a day—around 40 gallons per minute—but that was too much for the university’s wastewater system.” It would be too costly—and wasteful—to dispose of that much water every day for the foreseeable future.
Bentonite Slurry Wall
The project team quickly developed a solution: a bentonite curtain around the perimeter of the building. Bentonite is a naturally-occurring expanding clay. When mixed with water, the clay expands to form a nearly watertight barrier.
Using an excavator with a specialized bucket, contractors dug a trench around the entire footprint, 2 ½ feet wide and 30 feet deep. A water/bentonite slurry was pumped into the trench to keep the sides from collapsing.
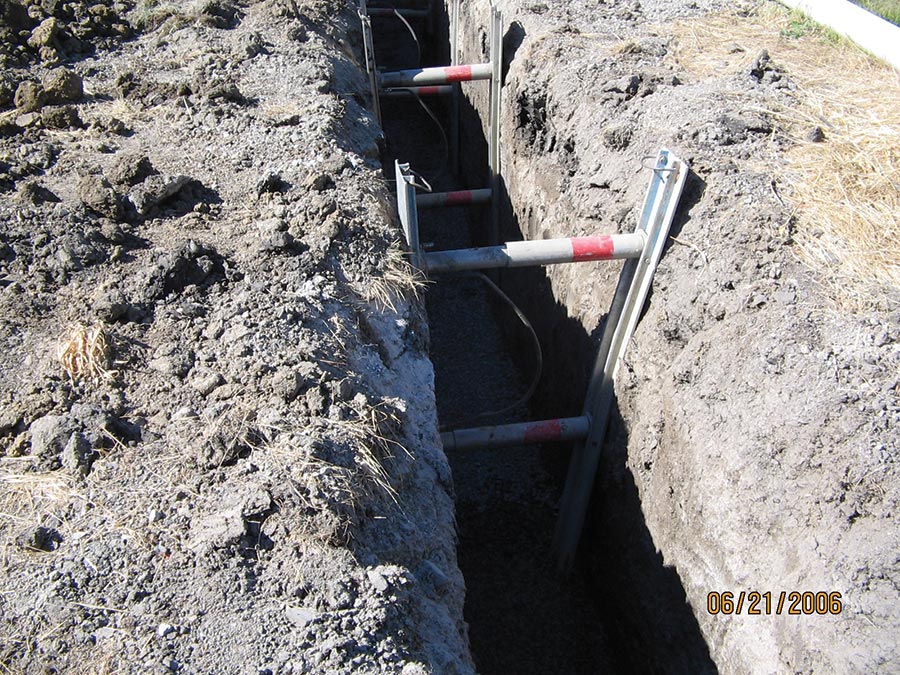
To reduce the load on the dewatering system, a bentonite slurry wall was installed around the building. A large track hoe dug a trench 2 feet wide and 25 feet deep.
“They pumped the water/bentonite mixture into the trench right after they initially started excavating,” says Christopher Dinno, senior director for capitol planning at the university. “They continued to excavate through the slurry, the water/bentonite mixture, until they get to the desired depth.”
The slurry was mixed with the excavated soil and then placed back into the trench to form the watertight curtain. In a video of the operation, available on our website, www.waterproofmag.com, shows how this took place.
“We pull out that material and mix it on the side of the trench,” he says. “We roll it with the track hoe to break up the material and get a nice mix, around a five-inch slump—and place in back in the trench using the bulldozer. The material slides in at about a 3:1 slope and pushes the water/bentonite mixture along. When the liquid gets too close to the surface, they extend the trench.”
The trenching operation was finished in about two weeks, and the bentonite performed flawlessly. When completed, the dewatering system that formerly processed 320,000 gallons a day was now handling only 40,000 gallons per day, most of it seeping up from below.
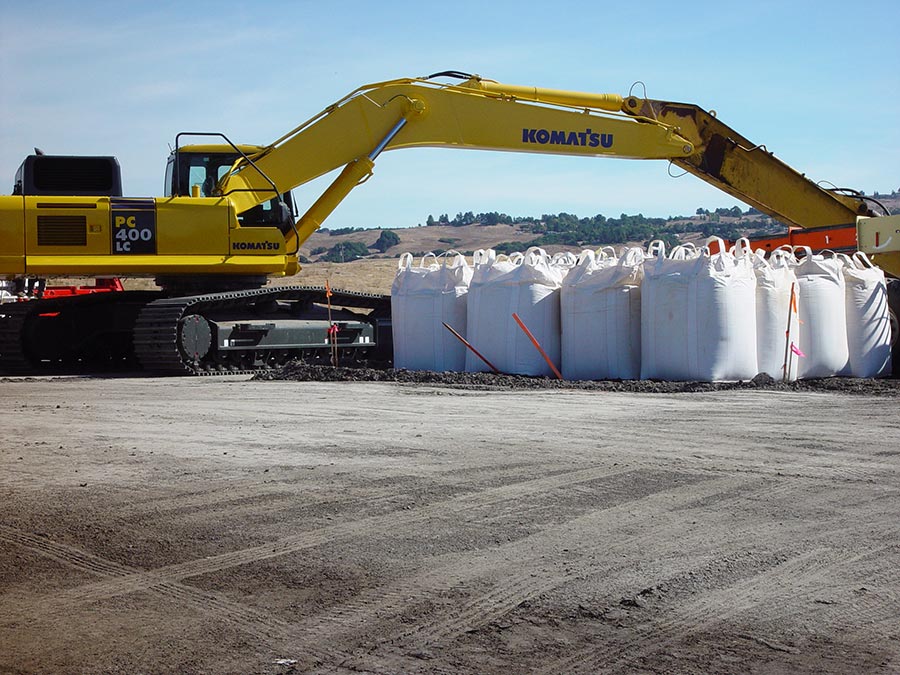
Bentonite arrived in large bags and was mixed with water and native soils to create an impermeable wall.
Foundation Work
While the slurry wall was being installed, Rudoph & Sletton continued the foundation work. The basement was excavated, and because of poor/expansive soils at the site, steel-reinforced concrete piles were driven deep into the ground for support. Native soil below the building was removed and replaced with several feet of pervious fill and a network of perforated drain pipe, part of the permanent dewatering system. Just before the slab was poured, workers installed a 10-mil underslab barrier from Stego to minimize moisture penetration.
Even with a complex dewatering system, designers recognized basement waterproofing would be critical, so they specified W.R. Grace for the waterproofing membrane, sealants and drain panel. Lawson Roofing did the install.
“The job was pretty straightforward,” reports Rich Lawson, owner of the company. “We did it in the early spring, so it was pretty wet. The bottom of the trench was 12 or 15 feet below grade, and it was really muddy. That made it difficult for some of the guys, but the actual installation was quite simple.”
Grace’s Bituthene® System 4000, a high-quality peel-and-stick membrane was applied to the exterior basement walls; Lawson sealed penetrations with their two-component liquid membrane sealant.
The sump pit, on the other hand, required the waterproofing to be installed before the concrete. Grace’s Preprufe® 300R, a product developed specifically for pre-applied and blindside applications, fit the bill. Preprufe® forms an aggressive adhesive bond with the concrete that ensures fully-adhered performance eliminating potential for water migration and egress.
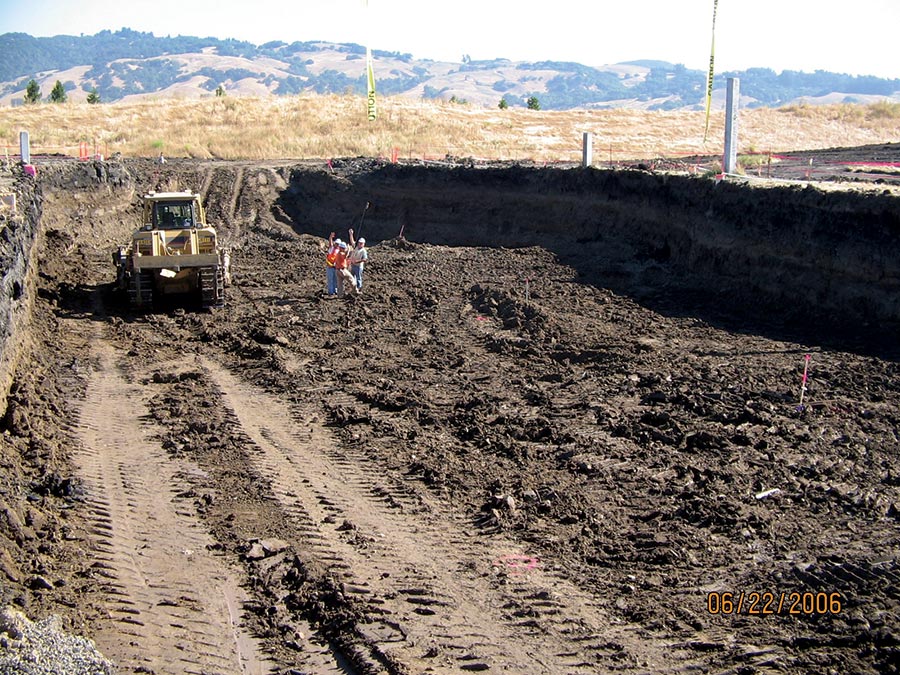
Temporary pumps removed up to 400,000 gallons of water a day to allow basement excavation to proceed.
Permanent Dewatering System
The sump pit is located in the concert hall basement, as far from the stage as possible, and is large enough to accommodate two sump pumps. Planners designed a redundant system so that even when one pump is offline for repairs, the other will keep the building dry. The Paco submersible lift pumps are wired so that if the water flows faster than a single pump can handle, the rising water in the sump will activate the second pump.
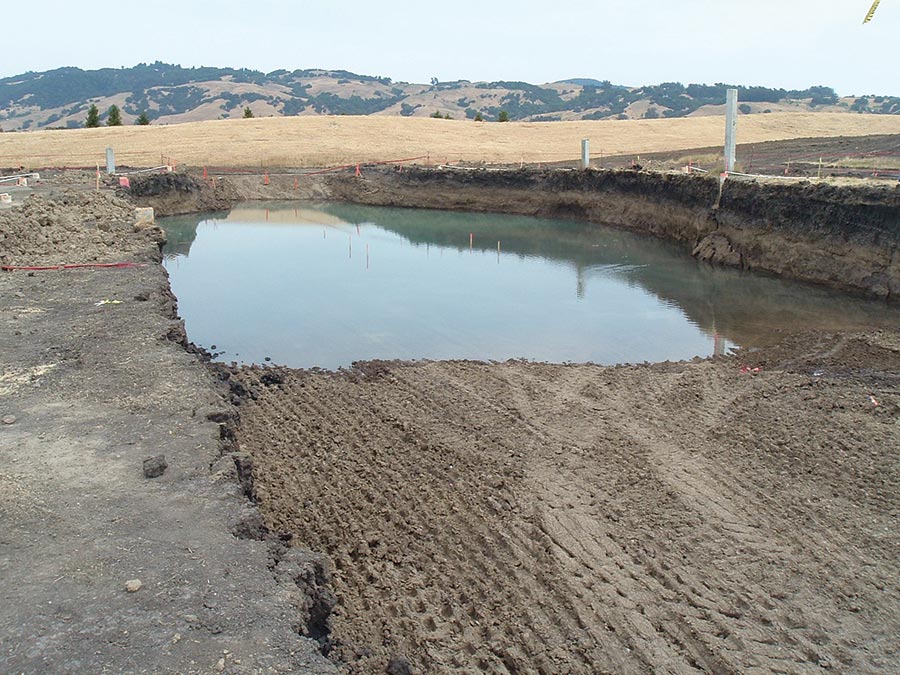
When the dewatering system was shut down overnight, the water table returned to its normal level, 5 feet below grade.
The system was installed in late 2007, and the temporary dewatering wells turned off. After 6 weeks of testing, the temporary wells were shut down permanently.
Soundproofing
The challenge for the designers, and for the acoustical engineer at Kirkegaard, was how to ensure that the noise and vibrations from the constantly running sump pumps and other mechanical equipment doesn’t disturb the sensitive acoustics in the concert hall.
With an overall cost of 110 million dollars, the university and its backers expect a world-class facility with the very finest sound quality. Modeled after Tanglewood, a performing arts venue in Massachusetts, the 1,400-seat hall features two balconies, behind-stage seating, and is expected to host some of the world’s finest musicians.
To isolate the concert hall from the sounds and vibrations of the mechanical equipment, the floor of the hall is actually a steel pan deck suspended four feet above the basement slab. Any vibrations or sounds from the mechanical rooms will be completely undetectable to guests in the hall.
The Green Music Center is expected to be completed in Sept. 2008.
Spring 2008 Back Issue
$4.95
Fixing a Broken Foundation
Sump Pumps Under the Stage
Built-Up Roofing: The Basics
AVAILABLE AS A PDF DOWNLOAD ONLY
Description
Description
Fixing a Broken Foundation
By Melissa Morton
Many waterproofers expand into the foundation repair business. From minor cracks to major underpinning work, here’s how to determine the severity of the problem, and the products and techniques used for repair.
Sump Pumps Under the Stage
By Clark Ricks
A significant portion of the new concert hall in Sonoma, Calif. sits below the water table. In order to keep the building dry—and the concert hall quiet—the building uses an innovative dewatering system.
Built-Up Roofing: The Basics
By Dan Calabrese
Considered the standard treatment for flat roofs, built up roofing is one of the oldest, most reliable, and overlooked methods.
Additional Info
Additional information
Magazine Format | PDF Downloadable Magazine, Print Mailed Magazine |
---|
FAST FACTS
- Project Name: Donald and Maureen Green Music Center
- Location: Sonoma State University, California
- Size: 1,400-seat Concert Hall
- Cost: $110 million
- Date: July 2006 – Sept 2008
CONSTRUCTION TEAM
- Design Architect: William Rawn and Associates
- Executive Architects: BAR Architects and A.C. Martin Partners
- Construction Manager: Rudolph and Sletten, Inc.
- Mechanical and Electrical Engineer: Flack & Kurtz and Ove Arup and Partners
- Civil Engineer: Brelje and Race
- Acoustics: Kirkegaard Associates
- Theater Consultant: Auerbach, Pollock, Friedlander