By Vanessa Salvia
Application of MFM Building Products’ Ultra HT. The beige metal roof can be seen on the lower portion of the building.
It may seem unnecessary to waterproof a metal structure, since metal is inherently waterproof. Metal structures are typically affordable, low-maintenance, quick to build, and weather resistant on their own. But there are some factors that affect their structural and waterproofing integrity.
Since a metal structure bakes all day in the hot sun, the materials need to be formulated for high temperatures. In past years, contractors would use traditional saturated felt or granulated underlayments under metal roofing and parapet walls capped with metal. What they found, says David Delcoma, the product marketing manager for MFM Building Products, is that the waterproofing membrane that they were putting underneath wasn’t designed to be under metal. “The softening point of the mastic was not sufficient to handle the heat and you would end up with mastic bleed-out onto the surface of the building,” he says. “That kickstarted the need to have a special waterproofing barrier specific to metal.”
Roofing Underlayments
Delcoma says that in terms of metal buildings, the roof and the walls are concerns. “A metal roof must have a special underlayment because there’s so much heat,” Delcoma says. “These are applied directly to the roof deck and act as air barriers, which need proper ventilation to dissipate the heat regardless of the final roofing surface, whether that be metal, tile, asphalt or metal shingles or wooden shakes.” For metal or tile, a self-adhering underlayment must be able to withstand temperatures above 230 degrees Fahrenheit.
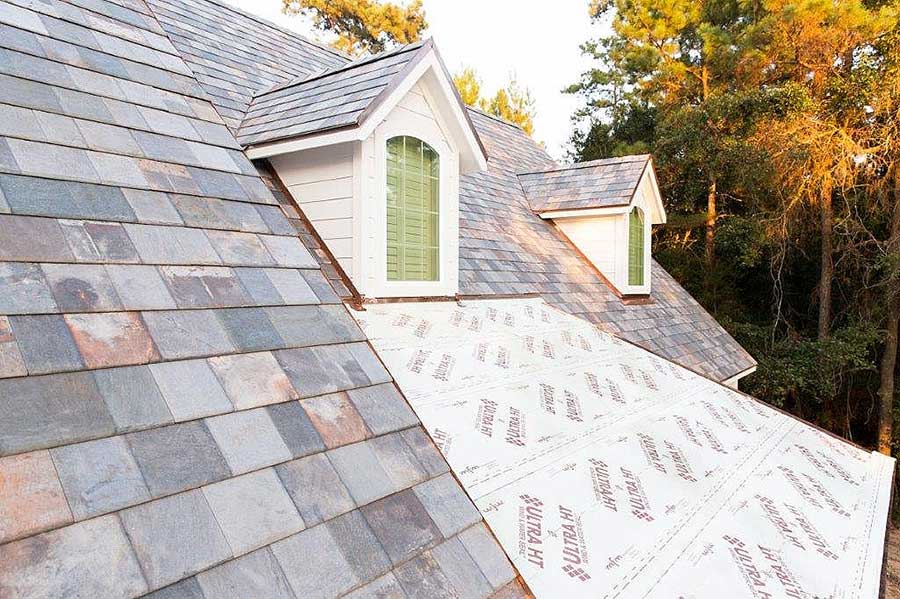
Application of MFM Building Products’ Ultra HT Wind & Water Seal Underlayment on a residential home roof.
Roof coatings are designed to take the sun’s heat, but using something reflective, in silver or white, would be a good idea. Reflectivity would lower cooling costs. A metal roof with no protection would likely rust, and condensation would build up on the metal surfaces.
Metal Sidewall Protection
High temperature rated self-adhering roofing underlayments are also being used on buildings clad with metal panels or on parapet walls capped with metal. Again, the problem is the heat build-up under these systems. If using a self-adhered product, you must provide proper ventilation and make sure the membrane is rated at 230 degrees Fahrenheit or above.
MFM Building Products has a new high-temperature roofing underlayment called Premium HT Tile & Metal. This self-adhering (peel and stick) underlayment is intended to be used as a whole-roof underlayment. Its high-grade, reinforced polyester fabric is laminated to a high-temperature asphalt adhesive system which is also fiberglass-reinforced. It will withstand the high temperatures created by metal and tile roofing up to 250°F (121°C). The glue, or mastic, that holds the self-adhered products on must be formulated for high temperatures. “Otherwise it will liquify and run right down the front of your siding, which has happened!” he says with a laugh.
There are three types of roofing underlayments that are on the market. One is traditional felt paper that is saturated in asphalt. It’s nailed to the roof with shingles placed over it. Another is synthetic underlayments similar to a plastic sheet that is also nailed to the roof with the roofing products over the top. The final type is the self-adhered, which are typically a more expensive option. “The peel-and-stick underlayments will protect the structure from any kind of weather before, during, and after the final roofing or sidewall system is installed,” Delcoma says. “Especially in today’s climate of building materials, there can be long delays before the materials are delivered so you want to provide as much protection as possible until the roof and sidewall systems are installed.
Metal Walls
Most metal buildings are built slab-on-grade, so any joint between where the concrete stops and the metal starts needs waterproofing attention. “That’s typically covered by caulking,” says Matt Veazey, president of Rubber Polymer Corp. “I would use a UV-stable product. Any of our water-based products like Rub-R-Wall Aqua would do the trick.”
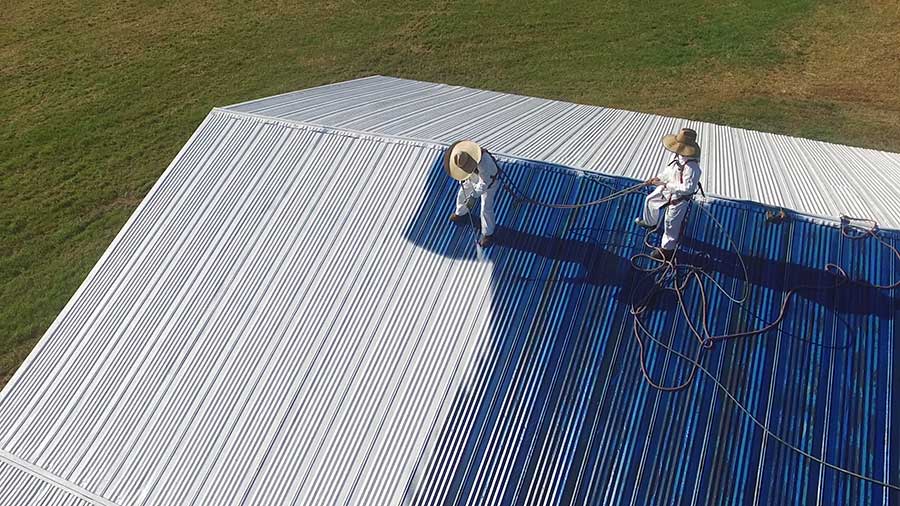
Spraying Ames Research Laboratories’ Maximum Stretch Elastomeric Roof Coating & Sealant onto a metal roof.
Additionally, doors, windows, vents, or any transitions from the roof above or floor slab below will be a concern for weather and moisture. With metal structure walls being so vertical, water entering the structure wouldn’t be as much of a concern. That said, it would make sense to install overhangs, gutters, and downspouts to divert water away from the building. With a metal roof, you would definitely address seams and fasteners, especially if there’s less pitch. These could be caulked and sprayed with a waterproofing membrane. “With the seams, you may caulk them then lay some mesh tape down, and then spray over that,” says Veazey.
Vapor Retarders
Condensation occurs when warm moist air, and cool surface temperatures meet. Visible condensation occurs on surfaces below dew point temperatures. Concealed condensation occurs when moisture condenses on an interior surface. Proper ventilation is one key way to minimize condensation in a metal building.
Another way is to use vapor retarders to inhibit moist air from passing into the inner regions of the roof or wall system. Vapor retarders are rated by the amount of moisture that can pass through them. The lower the “perm rating,” the less vapor transmission will occur. There are various types of vapor retarders including structural membranes or other impermeable materials. Depending on the material used, any seams must be sealed, such as with side-laps with peel and stick tabs or insulation tape.
Evaluating the Roof Needs
Joseph Butterfield, a sales representative with Ames Research Laboratories, a manufacturer of elastomeric waterproofing coatings for basements, foundations, and roofs, says they look at a few criteria to determine the best product to use on a roof. Over time, metal roofs tend to expand and contract due to temperature differences, which not only causes the panels to rust but can also cause the seams to become weak and ultimately fail. “When inspecting a metal roof, it’s always important that you check for drainage issues, panel corrosion, and rusty/loose fasteners,” Butterfield says. “More times than not, water leakage in a metal roofing system is caused by deteriorated panel seams and flashings. We look to see if there are any cracks or voids and determine if they are leaking.”
If the surface area is significant, Butterfield recommends that it be primed first with a waterproofing primer like Blue Max Liquid Rubber. The primer helps fill any cracks or voids, strengthens the seams, prevents further rust from showing through, and reflects up to 88% of the UV. After the waterproofing primer goes two coats of a sealant, such as Ames’s Maximum-Stretch, a white elastomeric rubberized acrylic roof coating and sealant. Using a product with extremely high elasticity allows the roof to expand and contract due to temperature fluctuations.” These coatings form one continuous watertight seal and are designed to extend the overall lifespan of any metal roofing system, old or new,” Butterfield says.
Summer 2021 Back Issue
$4.95
Selecting Dehumidifiers
Options for Structural Repair: Crack Repair, Carbon Fiber, Piering, Grouting
Waterproofing Metal Buildings
Mold Growth in New Construction
Waterproofing and Renovating the Empire State Building
AVAILABLE AS DIGITAL DOWNLOAD ONLY
Description
Description
Selecting Dehumidifiers
By Vanessa Salvia
Many homeowners think they can buy a dehumidifier off the shelf of a big box store and plug it in down in their basement. But there are many problems with this approach, including inadequate drainage, inadequate air movement, lack of air filtration, and sometimes catastrophic failure.
Options for Structural Repair: Crack Repair, Carbon Fiber, Piering, Grouting
By Vanessa Salvia
Here’s a primer on the four major aspects of repair when there is a structural or non-structural issue with a basement. It takes some skill to discern which approach is best, especially with regard to cracking, and the experts we talked to broke it down for us.
Waterproofing Metal Buildings
By Vanessa Salvia
Metal structures have a lot of advantages, but when it comes to waterproofing they need special consideration. Many waterproofing membranes aren’t designed to be under metal. Since a metal structure bakes all day in hot sun, the materials need to be formulated for high temperatures.
Mold Growth in New Construction
By Michael Rubino
A mold expert explains how owners of new homes are regularly encountering major mold issues. Just because a home has no water damage doesn’t mean it is immune to mold.
Waterproofing and Renovating the Empire State Building
By Vanessa Salvia
One of the most iconic buildings received a much-needed facelift. A recent waterproofing and renovation project restored the Art Deco luster of the Empire State Building, the world-renowned 102-story skyscraper in New York City.
Additional Info
Additional information
Magazine Format | Digital Download Magazine, Print Mailed Magazine |
---|