By Vanessa Salvia
Rain screen furring strips installed over plastered straw bale wall just before vertical siding is installed.
Plant-based materials such as fibers made from straw, have been used as building materials for thousands of years. It wasn’t until mechanical methods developed for gathering, compressing, and baling straw (starting in the late 1850s but patented in 1910) that it became possible for straw to be used as a primary building block of exterior walls. John Straube, who wrote a paper called “Moisture Properties of Plaster and Stucco for Strawbale Buildings” in 2002, says that there was a short time when compressed straw bale homes were popular in Nebraska, but they fell out of fashion for nearly 50 years. In recent decades, these and other alternative systems have gained favor.
Alternative “natural” wall assemblies like straw bale or cob, are similar to traditional wood-framed walls in that they shouldn’t be placed below grade. They require a waterproof foundation and a waterproof roof that diverts moisture. Unlike traditional walls, however, these alternative structures are not designed to be waterproof.
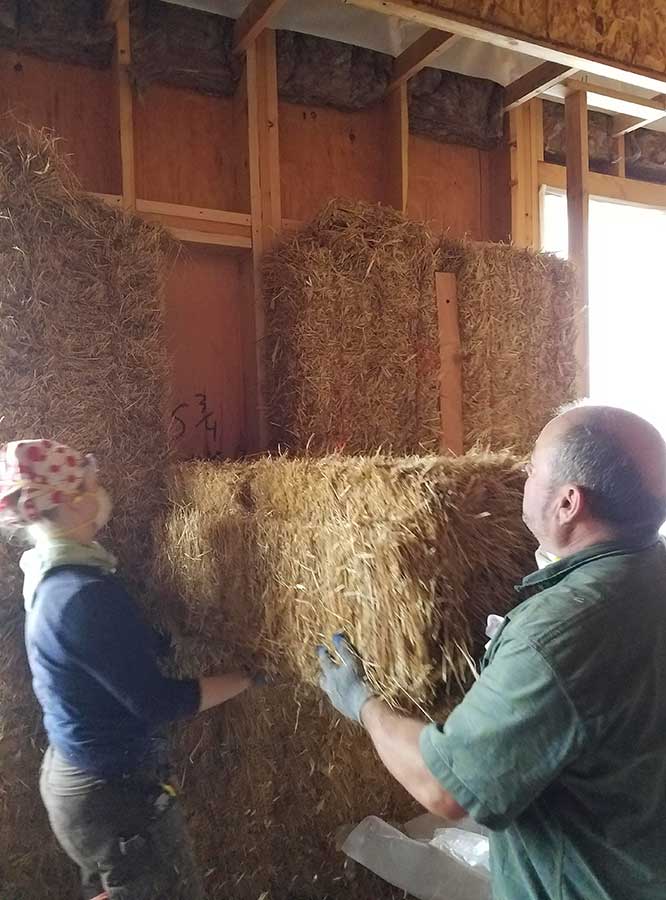
A straw bale-on-end being tipped into position against the interior of the plywood sheathing of the Mahonia Building. The vertical framing is on 24-inch centers, which allowed the crew to slip full 3-string bales (about 23 inches wide) between the studs. From the exterior, you cannot tell that the Mahonia Building is straw bale.
Any walls made from any plant-based building material, including wood, need a vapor barrier to avoid internal condensation. Insulated Concrete Forms (ICF blocks) don’t allow water to pass through their assemblies. “Liquid water and water vapor would have a difficult time passing through this kind of wall — which is why they are often found in below-grade applications, and when used for an entire house, the building’s HVAC design usually calls for another way to deal with interior water vapor,” explains Jim Reiland, owner of Many Hands Builders in Jacksonville, Oregon. Reiland is a general contractor specializing in rainwater catchment systems design, earth and lime plastering, and straw bale construction. Reiland is a member of the California Straw Building Association (CASBA) and a contributor and managing editor of the book Straw Bale Building Details: An Illustrated Guide for Design and Construction. He lives in a house with an ICF basement and straw bale first-floor walls. In his work, he has often built houses with ICF stem walls that support straw bale walls.
“Alternative wall systems such as cob, straw bale, and light-straw-clay, by design, aren’t water proofed in the same way builders waterproof ICF or wood chip block or monolithic concrete walls,” he says. Wall assemblies made with natural materials like straw are designed to be vapor permeable. Finishing these structures on both sides with some type of vapor-permeable plaster provides a protective coating, allows for vapor permeability, and increases fire resistance — according to 2018 IRC Code and Commentary Appendix S: Strawbale Construction, Section AS107 Fire Resistance, available at no cost from CASBA’s website, www.strawbuilding.org, a lime-plastered straw bale wall assembly has a 2-hour fire rating, and a clay-plastered assembly has a 1-hour rating, both of which compare favorably with conventionally framed and insulated wall systems, though not as high as buildings made with concrete walls.
“I use rigid foam insulation below grade,” he says. “Every building I have ever worked on has concrete in the foundation. Just about all of us use some sort of peel-and-stick membrane or paint-on flashing to waterproof foundations or vulnerable areas around windows and doors. There are just some things ‘natural’ materials aren’t very good at — getting wet and being unable to dry out is one of them.”
Any moisture in straw bale walls at the time the bales are stacked and plastered must be able to escape or dry out of the walls, Reiland explains, and if the wall’s moisture content rises well above 20% it becomes suitable habitat for mold.
Waterproofing Wood Chip Block
Faswall is a composite cement ICCF that is made with 85% mineralized wood and 15% cement. These blocks are stacked like ICF, with rebar placed and doors and window openings and utility and electrical conduits added. Then concrete is poured into the core. Although it is similar to an ICF block, the waterproofing strategy is more akin to an alternative building structure. On the foundation, Faswall recommends using a dimpled drainage mat over a secondary drainage plane, on-top of the Faswall composite. This secondary drainage plane can be a parge coat with paint-on waterproofing or MasterSeal, a mineral-filled asphalt emulsion sealcoat. “A parge coat is like a base coat stucco, with a paint on-waterproofing, on top and then a double redundant, 3D drainage mat over the top,” says Joseph Becker, ShelterWorks/Faswall’s technical/sales lead, and an active member of the Northwest Ecobuilding Guild. “That’s a pretty robust technique and some people balk, but for below grade basements and wet environments, a double redundant system in a critical situation like that is important for us.”
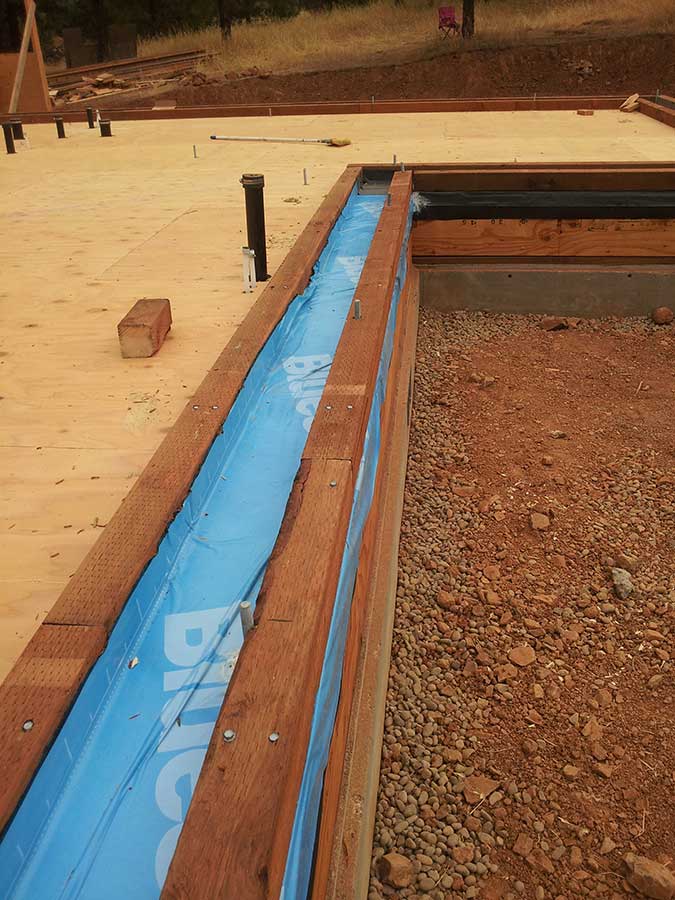
Peel-and-stick waterproofing membranes under the sill plates for straw bale walls on a raised floor.
For Faswall users, Becker recommends a double redundant, “vented rain screen” and siding, or stucco. The “vented rain screen” includes a vented air gap between a WRB (weather-resistant barrier) and the siding. That vented air gap prolongs the life of the siding and associated stain/paint by allowing moisture that gets behind the siding to drain or vent out. This could be as small as 1/16 of an inch up to a 1/2 or 3/4 of an inch. An air gap and a membrane underneath the siding is becoming increasingly common, especially in wet, stormy, wind-driven rain environments such as the Pacific Northwest.
“Above-grade waterproofing should be watertight, airtight, and vapor permeable,” Becker says. “An air gap between an airtight WRB and the siding makes it extra vapor permeable because you don’t have the siding pressed against it covered with four layers of paint.”
Above-grade stucco is a very common finish on Faswall, but that only provides a single drainage plane versus a double drainage of siding and a WRB, explains Becker. “If it’s really important, double redundant is good,” he says. “If it’s the desert of Idaho or wherever it’s really dry, a double redundant siding waterproofing is not as important as a single waterproofing layer such as stucco.”
Good Wall Design
Good wall design of these alternative assemblies includes proper siting, appropriate roof overhangs, and attention to detailing at windows and doors. “Exterior plasters are extremely effective at excluding water from wind-driven rain,” says Reiland. “However, most plasters applied directly to a straw bale wall are considered reservoir systems. By design, reservoir cladding absorbs moisture from wind-driven rain or splashes, then releases it when the weather turns dry and sunny.”
In rainy climates or highly exposed building sites, straw bale walls benefit greatly by adding siding as another exterior layer of protection. Reiland says an air-gap siding system consisting of cladding affixed over an air gap between the plaster and the siding, is effective in protecting the wall yet allowing water vapor from inside the wall to migrate out.
All of this is also true for light-straw-clay (LSC), although LSC’s dense and fire resistive nature prompt some builders to avoid the cost of interior or exterior plasters, and just install an exterior rainscreen siding and interior sheetrock. Any of the wall assemblies in question require the same roof and foundation that an ICF building would have. While it is imperative for these cellulose-based materials to stay dry, it is possible for these materials to have one wall that is vapor impermeable. “Generally though, almost all of these natural building systems need to have both sides be vapor permeable so moisture can escape the wall assembly,” explains Reiland. “That’s true whether the moisture was introduced during the time of construction or somehow leaks in during occupancy or during a storm of some kind.”
LSC walls are an infill system of loose straw lightly coated in clay that is packed into forms to insulate and enclose a building. The “light” refers to the light coating of clay on the straw’s fiber — just enough to make them stick together. The blocks are not light, weighing in at around 15 pounds per cubic foot. LSC is a good choice for adding insulation to existing walls because the walls can be furred out to any thickness by adding stud material to the desired depth of wall, although most LSC walls do not exceed 12 inches. One drawback here, however, is that LSC requires several months of drying time between installation and sheathing. If the site is not in a dry climate or is not adequately protected, early or unexpected rain can lead to wet walls that can’t dry out.
Adding Layers
It’s common in residential construction to add layers of coating in the form of paint. “If you put a few coats of latex paint on top of a sheetrock interior wall, that’s semi-permeable at two or three coats,” Reiland says. “Then the homeowners move out and someone else moves in and adds a couple more layers of paint — those walls become increasingly less permeable to the point that it becomes a vapor barrier.”
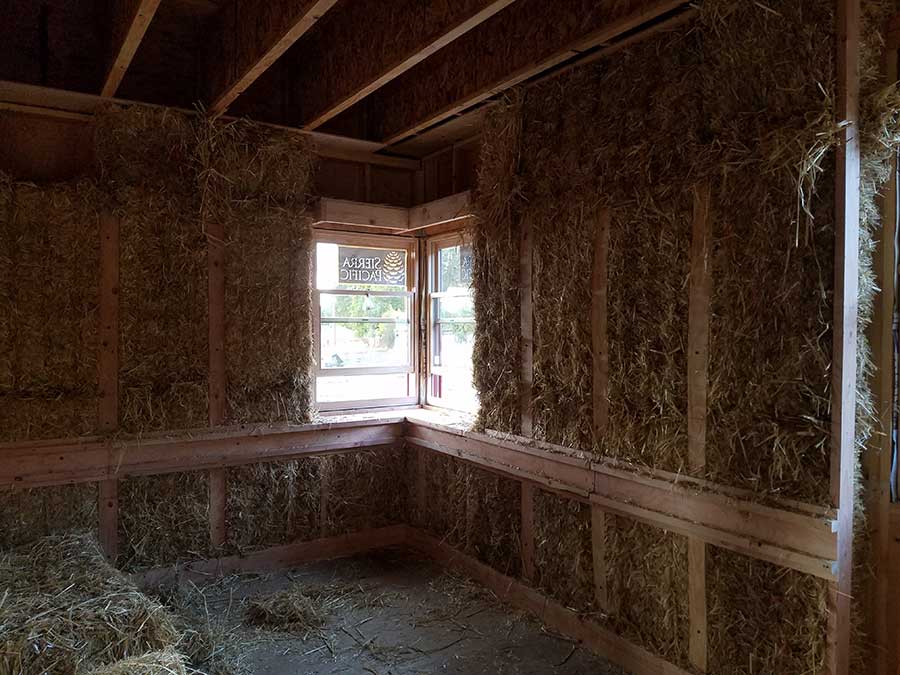
A mostly completed section of Mahonia Building wall. Some bales still need to be placed. They used vertical battens and long screws to secure the inside vertical edges of the bales to the exterior stud. Interior walls were covered with plaster made ofclay, chopped straw, and sand. The waist-height chase is for routing electrical.
Straw, straw clay, or cob can’t have that type of treatment on the inside. Instead, they need plaster on the interior and plaster of some sort and a rain screen on the exterior. “For a bathroom shower up against a straw bale wall, other builders have applied two coats of the interior plaster, added furring strips, then installed tile board and tile. That creates an air gap so if moisture does get through that tile, it wouldn’t go into the bale. It would drip straight down instead.”
Reiland helped construct the three-story Mahonia Building, which houses an organic wholesale food distributor in Eugene, Oregon. The Mahonia Building is a unique exception to this requirement in that it does not have an exterior plaster. Only the top two floors are straw bale.
“The interior is finished with a 1 1/2 inch-thick clay plaster,” says Reiland. “On the exterior, we put the bales right up against 1/2-inch plywood, which is at the very minimum of vapor permeability to just allowed for moisture to pass through.” The exterior is also building-wrapped over furring strips and metal siding over the sheathing.
In 2022, Reiland will be building a straw bale structure using a similar sheathing detail, but instead of furring strips and siding the plan is to use a drain mat suitable for a three-coat stucco. “This particular combination might not work as well in colder, wetter regions,” Reiland cautions.
The 1 1/2 inch-thick plaster is a typical thickness for that kind of building, but is unusually thick for conventional construction, Reiland says. “You find plaster thicknesses anywhere from a half inch to two inches thick or more,” he says. “Thicker plasters are generally desired on straw bale construction because the bale surface is uneven, unlike plywood.”
Different Permeabilities
Straub’s paper concluded that a 1 1/2 inch-thick stucco made of a mixture of cement and sand has a permeance of less than 1 US Perm. 3. As the proportion of lime increases in a plaster mixture, the permeance increases. The permeance of a 1 1/2 inch-thick cement and sand stucco can be increased to 5 or 10 US Perms by replacing half the cement with lime and to 15 to 30 US Perms by using a pure lime and sand stucco. Applying an oil paint to a 1:1:6 cement:lime:sand stucco will provide a permeance of less than 60 metric perms (1 US perms) and thus meet the code requirements of a vapor barrier.
Earth plasters, such as adobe, which are mixtures of clay, straw, and sand, easily resist 24 hours of constant wetting, Straube says, although the topmost 1/8-inch of surface becomes quite “muddy.” A lime wash over earth plaster increases the mechanical strength of the plaster once it’s wet, meaning that it increases the plaster’s resistance to erosion from rain. Read Straube’s paper here: https://tallerconco.org/wp-content/uploads/2017/05/Straube_Moisture_Tests.pdf
Failures of These Buildings
The Nebraska homes that Straube references in his paper were built in the late 1800s and early 1900s with conventional roof overhangs. “Several of these buildings are over 100 years old and still in use,” says Reiland. “When straw bale building was ‘revived,’ or rediscovered in the American Southwest in the 1980s, the thick walls resembled those found in vernacular adobe structures people knew and loved,” Reiland explains. “So long as the building design had sufficient roof overhangs to protect the walls from seasonal rain, they performed extremely well. Structures that used parapet roofs on pueblo style straw bale buildings didn’t fare as well.”
Pretty much any wall system, including stud wall and conventional insulation, that relies on nothing more than a coat of plaster to protect it from overhead rain is going to develop problems. The walls of traditional adobe homes were repaired each year, which, while a fairly easy fix, is not something our modern lifestyle accommodates.
“We need to design and build with materials while keeping in mind their strengths and limitations,” he says. “These are lessons that reinforce the often-heard mantra: buildings need a good hat, good boots, and a coat that breathes.”
Fall 2021 Back Issue
$4.95
Protecting a Foundation from Drought
Cool Roofing
Waterproofing Alternative Construction
Case Study: Pool Deck Crack Repair
Case Study: The Standard at State College
AVAILABLE AS DIGITAL DOWNLOAD ONLY
Description
Description
Protecting a Foundation from Drought
By Vanessa Salvia
Periods of drought evaporates all moisture from the soil, which creates cavities where water can collect. When rains return, the water will have ready-made channels to run through, and as the soil expands it can lift up the foundation in uneven ways.
Cool Roofing
By Vanessa Salvia
Just as wearing light-colored clothing on a hot, sunny day results in a cooler feeling on your skin, cool roofs can make any building feel more cool on a hot, sunny day. According to Energy Savers, standard or dark roofs can reach temperatures of 150°F or more in the summer sun while a cool roof under the same conditions could stay more than 50°F cooler and save energy and money by using less air conditioning.
Waterproofing Alternative Construction
By Vanessa Salvia
“Natural” wall assemblies like straw bale or cob are similar to traditional wood-framed walls in that they shouldn’t be placed below grade. They require a waterproof foundation and a waterproof roof that diverts moisture and unlike traditional walls are not designed to be waterproof.
Case Study: Pool Deck Crack Repair
The American Restoration company was hired to repair a cracking concrete slab around a swimming pool using Rhino Carbon Fiber Concrete Crack Lock stitches in conjunction with RCF High Strength Anchoring Epoxy Paste.
Case Study: The Standard at State College
The general contractor for the The Standard at State College high-rise building project needed a waterproofing solution that could be installed quickly and meshed with field requirements. CETCO was the only company with the product portfolio that met the various field conditions present including exposure, large voids, lengthy time frame, and weather.
Additional Info
Additional information
Magazine Format | Digital Download Magazine, Print Mailed Magazine |
---|