By Joe Dakin
An aerial view of many leaks in a roof.
Nearly all dictionary definitions state that a leak is the result of an accident — losing or admitting contents through a hole or crack in the barrier which was supposed to prevent those losses or gains. A leak is never a happy accident, and this is especially true with regard to our buildings, where a single leak can cause structural failure. To combat this risk to our buildings and their occupants, leak detection has become an important part of the real estate and construction industries.
For a long time, detecting leaks was done by visual inspection or using incredibly crude tools. This should not be acceptable to building owners in the modern age. Visual inspection is useless in most situations as the hole or crack is hidden below multiple layers which are costly to remove. Primitive tools for leak detection are also unsuitable, especially in modern structures that use complex roofing systems and feature green/vegetative roofs for aesthetic or environmental purposes. Finding a leak through six feet or more of overburden, using most available methods, simply does not work. Fortunately, there is a better way.
When Henry Ford revolutionized the motor industry, he did it by creating a system. The leak detection industry is undergoing a similar revolution, with the advent of Leak Detection Systems (LDS). Systems can be broadly categorized into either a “procedural system” or a “physical system,” the former requiring a change in behavior and the latter requiring the installation of equipment. Both of these categories apply to leak detection. A procedural leak detection system involves including specific steps in the construction process, while a physical leak detection system requires a network of sensors to be installed within the roof itself. To understand the value of both systems, we must first understand how and why leaks happen, and what the associated risks can be.
How Leaks Happen
Manufacturers of waterproof membranes have been innovating over decades, if not centuries, to produce materials which can withstand the elements and protect our structures (not to mention the people and property inside of them). There are hundreds of varieties of waterproof membrane available on the market, and when properly applied most of them will offer satisfactory protection. However, they are generally tested and rated in controlled environments with the best possible installation — this is not what happens in the real world.
Construction is a fractured industry, with different stakeholders operating in isolation from each other. The developer who invests a fortune to build a structure then passes off the execution phase to a general contractor (GC) who will then bring in a host of subcontractors (hereafter referred to as tradespeople) to complete all the necessary work that has been specified in the design phase by an architect. By the time the waterproof membrane is being installed, the project may have been under construction for a number of years, with hundreds of different trades crews coming and going. By this time, the GC is under significant time and financial pressure to complete the project. Roofs are very seldom covered all in one go, they are generally completed piecemeal as different trades complete a relay race around the roof deck. Site superintendents shuffle materials around to try and create the necessary windows of opportunity to complete work on the roof as well as protect the structure. However, they are at the mercy of delays in materials and labor, as well as events completely beyond their control such as the covid-19 pandemic. This order of operations is a system of sorts, but a very inefficient one, which creates abundant opportunities for damage to occur on the waterproof membrane.
Here is an example to illustrate the risk to the roof: A roofing contractor installs a liquid melt membrane in the northwest corner of the roof. They can’t cover it right away, as there is nowhere to store the insulation and other control materials on the roof. The next best thing they can do is move to the southwest corner, but first they have to wait for other tradespeople to finish installing windows and then move their equipment. In order to clear the southwest corner, the superintendent has the crane operator move a number of pallets and some HVAC equipment onto the northwest corner that has just been waterproofed. The roofer’s work (which may or may not have been tested for quality) is now used as a “staging area” for other trades people who are walking over the newly applied membrane. It is extremely common to find nails and screws embedded in the membrane, or pallets/heavy equipment making depressions or other deficiencies in the waterproof layer. There have been instances where tradespeople mechanically fasten their equipment right into the membrane.
As deadlines loom, these damages and deficiencies are covered up, hidden by layers of other material. Roofs are generally completed in the summer months and signed off before the rainy season when problems can set in. Leaks will not appear right away; it can take months if not years for moisture trapped in the roofing assembly to spread, by which time any warranty for workmanship has long since expired.
When moisture gets in, it spreads. Perhaps there is an incorrectly installed detail on the roof, a clogged drain, or perhaps it just takes time for moisture to filter down through the layers of the roof assembly. But when it eventually reaches the waterproof membrane — the last line of defense — those damages and deficiencies put in place years earlier become a problem. Moisture is driven by gravity to find the lowest point in the structure, eventually working its way into the roof deck itself. It can then be more time before this moisture begins to show inside the structure where an occupant may notice. The developer may or may not have sold the property on to another owner, the GC and the roofers have moved on to other projects. The building owner and occupants are now left with a leaky roof and a hefty bill for repairs or even full replacement.
The Costs Of Leaks
There are examples far and wide of the catastrophic structural damage that can occur from moisture ingress. On a fundamental level, we build our buildings from materials that are permeable, reinforced with materials that rust or rot. Moisture damage not only impacts the structure, but also the occupants; mold can flourish under damp conditions and cause long term respiratory issues, while repairs can displace tenants for weeks or months. Water damage increases in severity exponentially if not addressed in a timely manner, as it will spread throughout the structure. In Vancouver, poor design and installation of the building envelope combined with a coastal rainforest climate created a “Leaky Condo Crisis’’ which lasted for decades, the impacts of which are still being felt today. Billions of dollars in repair costs and insurance claims, whole buildings rendered unfit for habitation, and an ugly mark on the region’s construction legacy because water damage was allowed to wreak havoc.
Considering the risk endured by the waterproof membrane during construction, it is unsurprising that in many cases there will be cause to perform roofing repairs only five or ten years into the life of the building. Roofing assemblies range in their complexity, but none are simple. Evidence of water damage may be spotted in one area from the interior of the structure, however the cause of that damage could be in a completely different area on the topside of the roof. Only in very lucky situations is the cause of the damage visible to the naked eye, and even in those cases it may not be the only cause. The traditional process of locating a roof leak is simple and expensive. The building owner(s) incur the cost of hiring building envelope engineers, roofers, landscape architects, and many other costs as they tear up the roof to find the source of the damage. The occupants must endure noise and disruption, if not relocation for an unknown duration and the damage may not even be found. In the worst case scenario, the building may be condemned, or else the costs of repair bankrupts the owners. These risks are not simply academic; studies by the insurance industry have found that the number of annual water claims costing more than $500,000 has doubled since 2015, while those that cost over $1 million have tripled, according to 2019 data from Insurance Business America.
A Leak Detection System: Principles And Procedures
According to the Oxford English Dictionary, the first definition of a system is “a set of principles or procedures according to which something is done; an organized framework or method.” As illustrated earlier, construction is a complicated undertaking involving many parties following a system of sorts to complete the project. In this scenario, leak detection can be part of the system by incorporating a quality assurance scan into the construction schedule. All too often this is seen as “nice to have” by developers, and is value engineered out of the equation by GCs or roofers seeking to lower costs. This is a false economy for the developer, because the damages that can occur in the absence of a leak detection scan are the ones most likely to show in the short term, while the GC and roofers are still liable to perform re-work at a cost to themselves.
In the best case scenario, at least two leak detection scans are performed as part of a larger quality assurance system. The first should be performed as soon as the waterproof membrane has been installed by roofing contractors; the scanning report will show whether the workmanship is up to standard or whether there are deficiencies in the membrane. The second scan should be performed immediately prior to the covering of the waterproof membrane (on an inverted roof system) to identify damages caused by other tradespeople — this allows the roofing contractor to return and repair those damages. There are multiple options available for scanning at this stage, with an exposed membrane, however arguably the most effective is electronic leak detection (ELD).
ELD works by first isolating a section of the newly installed waterproof membrane using a perimeter cable. The roof deck is then wetted to create a conductive field across the surface of the membrane. The perimeter cable is then connected to the positive terminal of a power source, the negative terminal of which is attached to a ground source (usually a drain). This creates an electric field across the surface of the membrane, and because any hole in the membrane will allow the water to penetrate through, that hole will allow the charge across the water to dissipate into the grounded substrate of the roof deck, thus completing an electrical circuit.
A device sensitive to changes in voltage is then used to sample the charged field, and — because electricity is directional — the device is able to produce a vector which points the operator toward the leak. When using high voltage testing, a properly calibrated device not only locates holes, but also pinpoints where the membrane has been applied thinly and could easily become a leak due to construction activities or environmental damage over time.
Despite being seen as a luxury by some, a leak detection scan is the bare minimum that developers should expect in terms of a leak detection system for their roof. These scans generate reports that are invaluable when assessing the integrity of a membrane at a point in time during the construction schedule, and can be used to inform repairs. Scanning alone significantly reduces the risk of damage to our structures, but it is best employed as part of an overall quality assurance system. With the key principle being to treat the roof as an asset that should be protected, the key procedures include: checking the quality of the initial waterproofing installation, not using membranes as a staging area without considering how to protect it first, and not covering a membrane without first checking for damages.
A Leak Detection System: A Network
Now that we have covered principles and procedures that form the basis of a leak detection system, let us consider the second definition of a system: “A set of things working together as parts of a mechanism or an interconnecting network.” A leak detection system in this sense refers to a physical array of sensors embedded within the roofing assembly itself during construction. These sensors can be configured in a passive state, left to wait until activated, or they can be configured in an active state, constantly sampling the roof assembly. This kind of system is generally specified very early in the project at the behest of the architect or owner, and it exists for the life of the structure. Sensors measure a physical property, in the case of a leak detection system they are used in a variety of ways depending on the physical properties of the roof assembly, but the end result is the same, some form of measurement that can be interpreted to give an indication of the roof’s integrity.
Every roof is different, from its material properties and design, to its installation and geographic location. For this reason, a leak detection system is not a one size fits all product, but rather a network of nodes and data points that are compared and contrasted to produce intelligence. The sensors and data acquisition electronics are just the “eyes and ears” of a leak detection system, the “brain” is the process of tabulating data and analyzing trends. This analysis requires not just the stream of data from the sensors, but also the application of construction knowledge based on the individual roof’s characteristics (slope, drains, type of membrane, location, and many more).
A leak detection system is installed with foresight and generally shows its value years later, for example in the occurrence of a large-scale moisture intrusion event. In such a case, evidence of water damage is noted and the system can be used to narrow down the area for tear up. Rather than best guesses or random sampling, the team investigating the roof can instead target a specific area highlighted by measurements from sensors, saving significant time and cost. Some leak detection systems even incorporate augmented reality options, empowering roofing professionals to see the status of the assembly beneath their feet in real time — like having x-ray vision. In this scenario, a costly re-roofing project may be avoided to the benefit of all parties involved.
Owners do not need to wait for a water damage event to get value from a leak detection system. The sensor array embedded within the roof will measure the physical properties within the assembly, and with enough data points it is possible to chart a trend. Leak detection is a science, and trends can be analyzed against other data sets to aid with preventative maintenance. The cost-benefit of preventative maintenance has been widely explored elsewhere, simply put it’s the same philosophy as investing in regular oil changes rather than replacing your engine. A roof is easily as vital to a structure as an engine is to a vehicle, and should be treated as such. An LDS can also be used as a quality assurance aid when repairs have been made; it is difficult enough to find tradespeople to complete roof repairs, it is near impossible to know if their workmanship has solved the problem without waiting to see if damage occurs again. With an LDS embedded in the roof, owners can view the impact of repairs and rely on solid data to know if their contractors performed adequate repairs.
Summary
A procedural leak detection system involves planning and oversight, treating the roof as an asset that must be protected, and putting into place quality control measures such as a waterproof membrane integrity scan. In this kind of system, various leak detection tools can be used to produce a report or a pass/fail assessment — similar to checking a product on a production line for faults or defects. This kind of system can dramatically reduce the number of damages and defects which are otherwise prevalent on nearly every waterproof membrane installed on a construction site.
A physical leak detection system involves installing sensors and electronics into the roof assembly itself. The data from a physical system can be fed into an algorithm, or else reviewed by experts to determine the physical properties in the hidden areas of the roof. This kind of system can be used to inform building managers where preventative maintenance is required to improve the longevity of the roof, as well as guide repair efforts by providing an accurate location of the source of a roof leak.
A procedural leak detection system is only point-in-time, valid for the time of the scan or other quality control measures applied during construction. By contrast, a physical leak detection system is there for the life of the structure, capable of providing real-time intelligence on the status of the roof as required. Both systems are incredibly valuable to various stakeholders in the construction and real estate industries, where quality control and real-time information can be the difference between structural damage and a long-lived building.
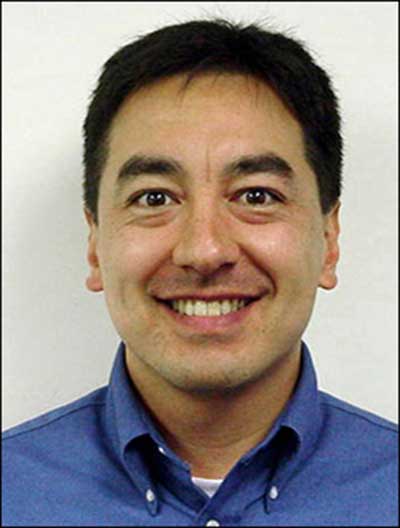
Joe Dakin
Joe Dakin has been communications manager at SMT Research since 2020, where he combines his passion for architecture with his love of technology. In his role he spends time on site; as well as helping to educate architects, building envelope engineers, and roofing contractors on the benefits of leak detection and structural monitoring. Learn more at www.smtresearch.ca.
How Stakeholders Benefit From A Leak Detection System
Architect
- Resilient structures that stand the test of time and protect the designer’s legacy
- Roof performance data across multiple buildings in different environments can aid future design
Membrane Manufacturer
- Product is protected, great reputation upheld
- Data on how teams are performing installation
- Empower repair / inspection teams with the most useful information
General Contractor
- Improved efficiency as re-work reduced
- Accountability for roofing contractors
- A great reputation for protecting structures
Roofing Contractor
- Less time wasted performing re-work
- Information on how different teams are performing
- Accountability for GC / other trades once work is completed
Developer
- Increased value of the structure
- Reduced insurance premiums
- Reputation for producing greener structures
Long-Term Owner
- Stay well informed on roof health
- Lower costs of roof investigation
- Lower insurance premiums
- Dramatically reduce the likelihood of structural damage
Occupants
- Less likely to experience mold / water damage
- Less likely to require relocation during repairs
- Less likely to incur special levy costs for roof repairs
The Planet
- Lower embodied carbon during construction (get it right the first time)
- Lower operational carbon as fewer large-scale re-roofing projects required
- Lower landfill contents from wet/damaged roofing and related products